click for more info :
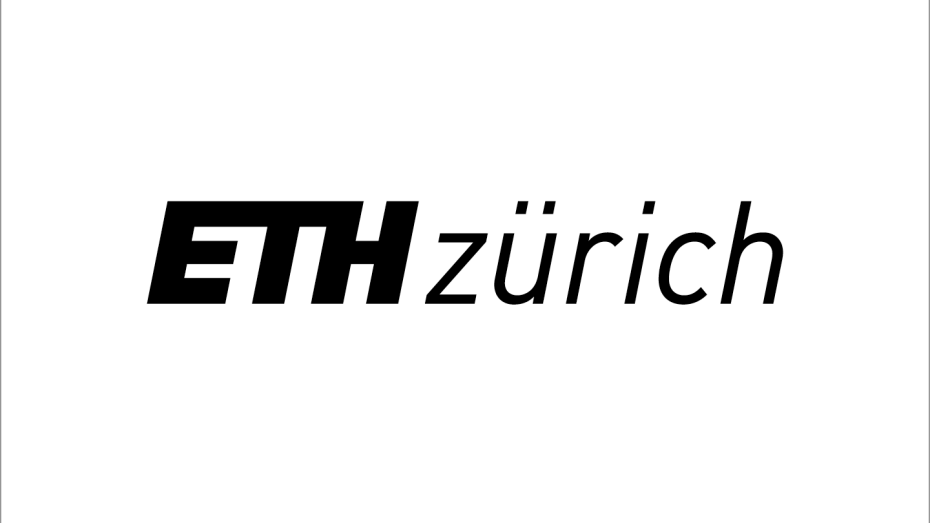
ETH ZURICH
Clay Rotunda
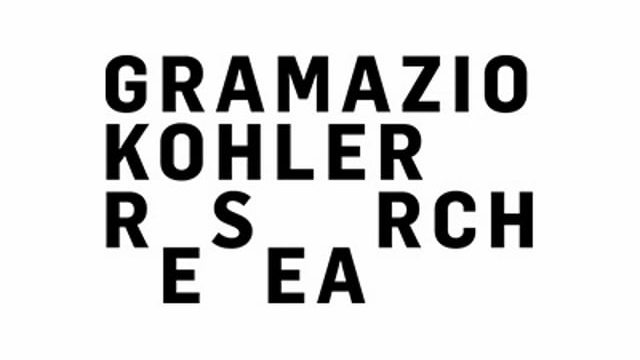
The Clay Rotunda is a free-standing earth-based cylindrical structure constituting the outer, soundproof shell of the SE MusicLab, a high-fidelity music auditorium built inside the newly refurbished Gurten Brewery in Bern.
The cylindrical structure combines clay, a sustainable building material, computational design techniques, and a fabrication method developed through generations of MAS in Architecture and Digital Fabrication at ETH Zurich.
The structure has a diameter of 11 m and reaches a height of 5 m, with a thickness of just 15 cm of unreinforced clay.
This method consists of picking and compacting into place clay cylinders with the aid of a mobile robotic arm, providing enough force to build up monolithic structures.
Location: Bern, Switzerland
Built for: SE Music Lab
Construction: 2020-2021
Credits & Publications
Fabrication, Process development, design: Gramazio Kohler Research, ETH Zurich
Client: SE MUSICLAB AG – Jürgen Strauss, Jost Kutter, Manuel Frick, Lorenzo Zanetta, Filippo Melena, Anna Imfeld-Aebischer, Markus Imfeld
Collaborators: Coralie Ming (project lead), David Jenny, Hannes Mayer, Edurne Morales, Anton Johansson, Indra Santosa, Jomana Baddad, Nicolas Feihl, Selen Ercan Jenny, Jesus Medina, Karol Wojtas
Support: Mike Lyrenmann and Philippe Fleischmann (Robotic Fabrication Laboratory, ETH Zurich), Andi Reusser (Institute for Building Materials, ETH Zurich)
Selected experts: Seforb Sàrl – Joerg Habenberger, Gotham design studio
Selected contractors: LEHMAG AG – Felix Hilgert
Industry partner: Brauchli Ziegelei AG, Wirz AG Bauunternehmung
Sponsors: Wirz AG Bauunternehmung, Welti Furrer, Eberhard, Siemens, Geberit, ETH Zürich Foundation
Photos: Gramazio Kohler Research
Publications: ArchDaily, Archello, Insight Architecture, Parametric Architecture
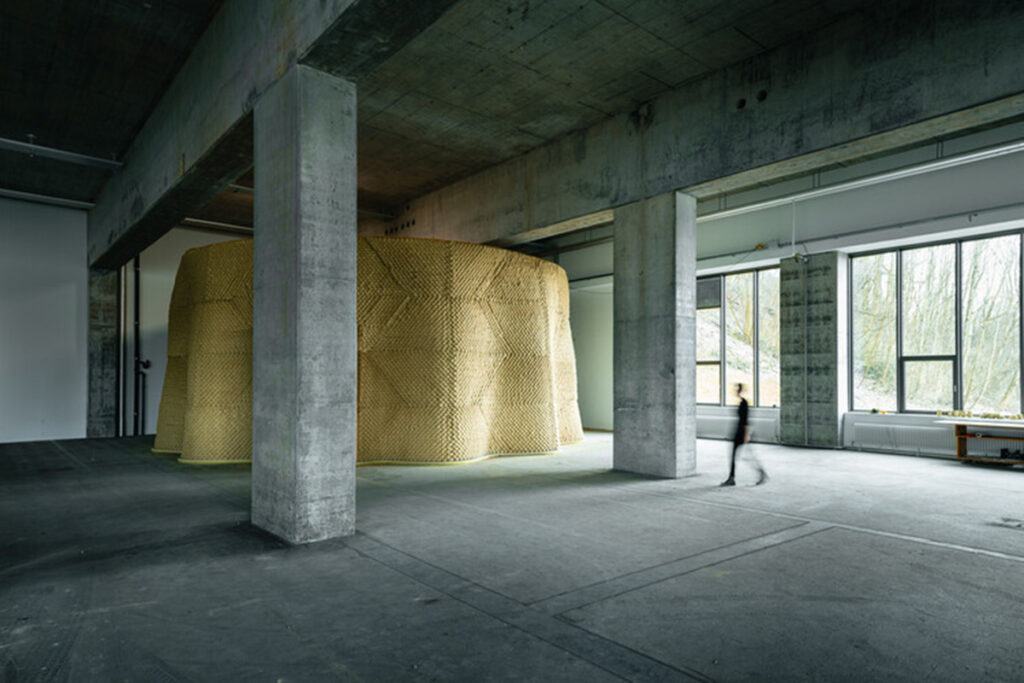
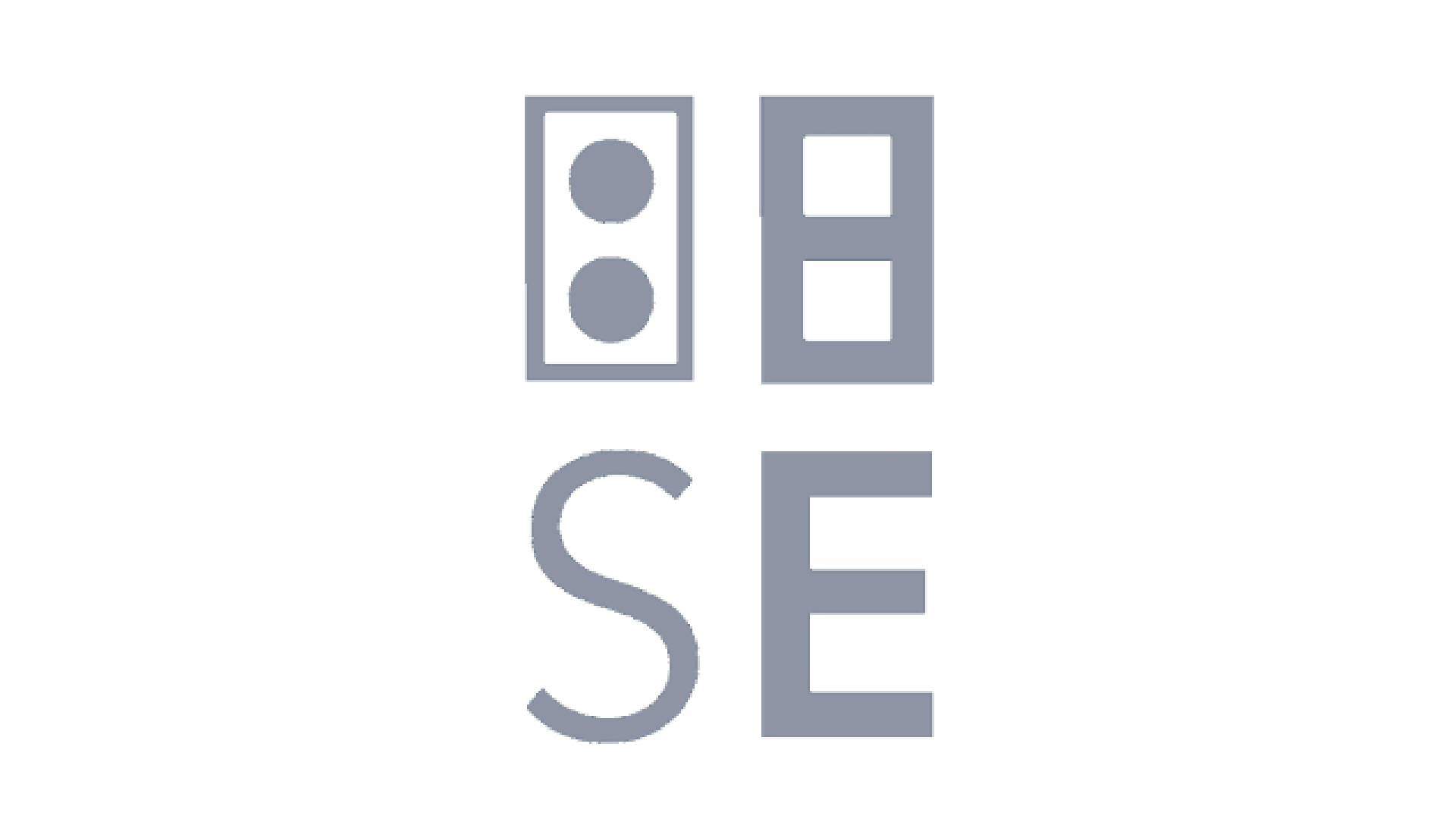
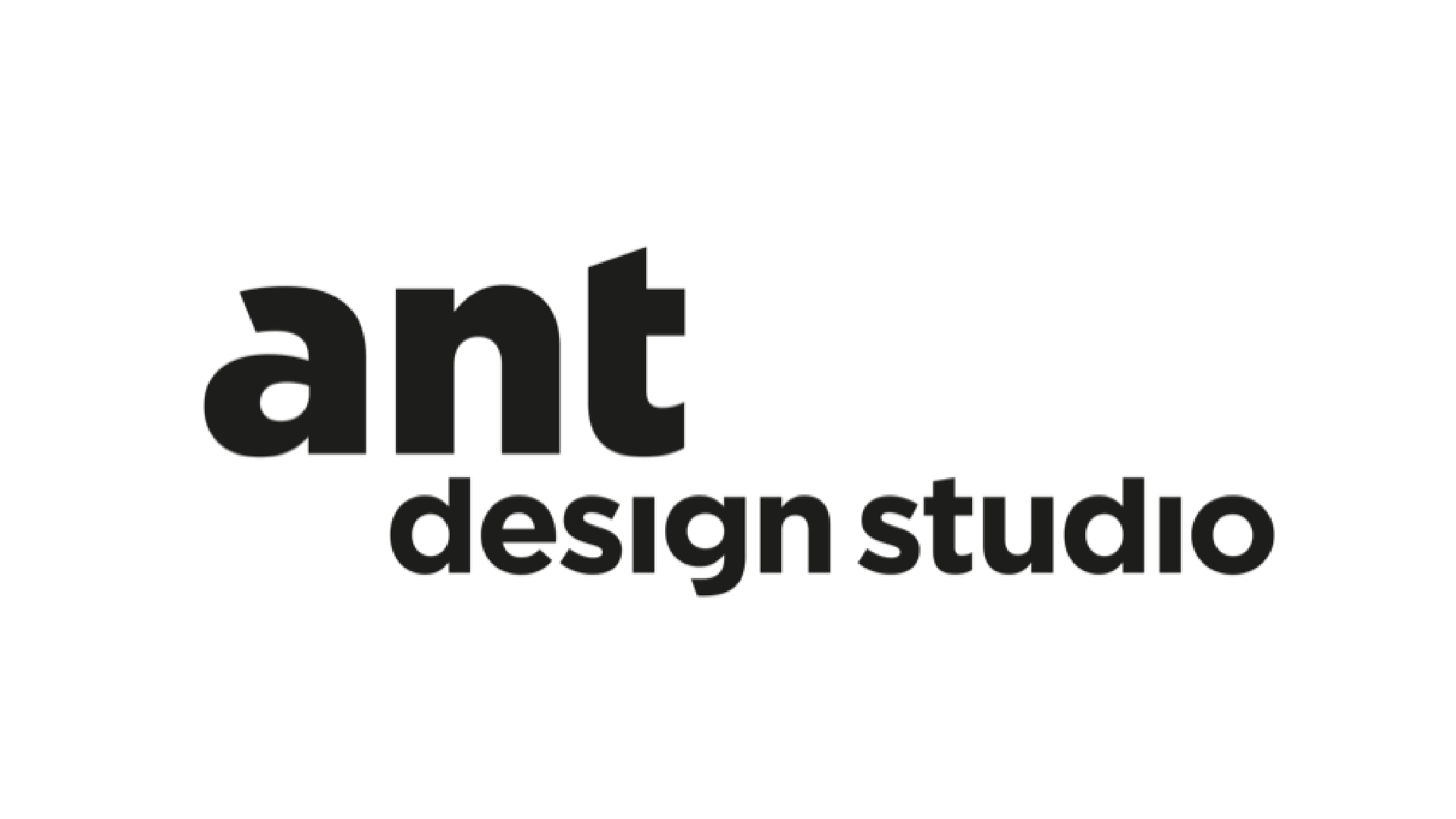
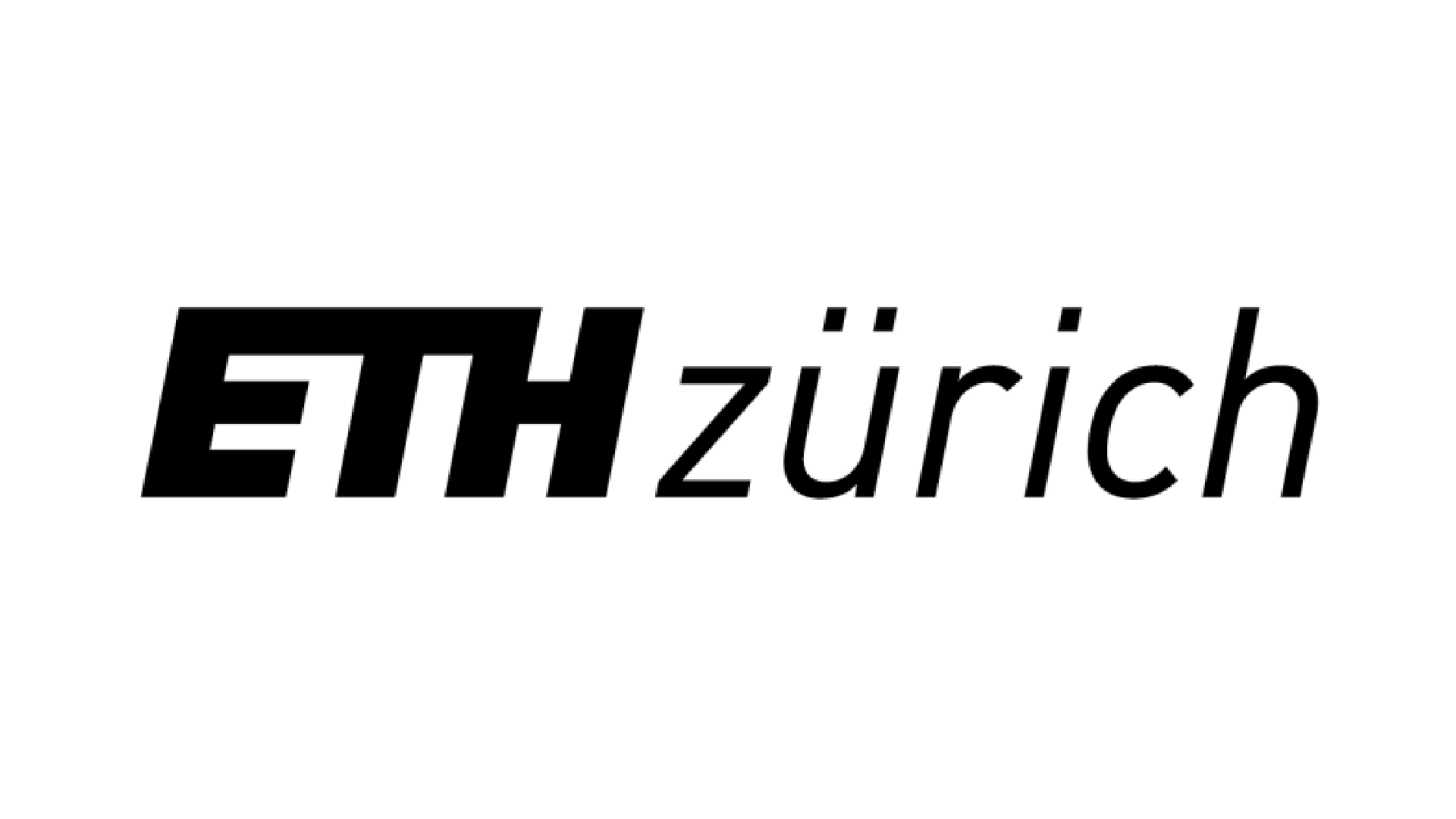
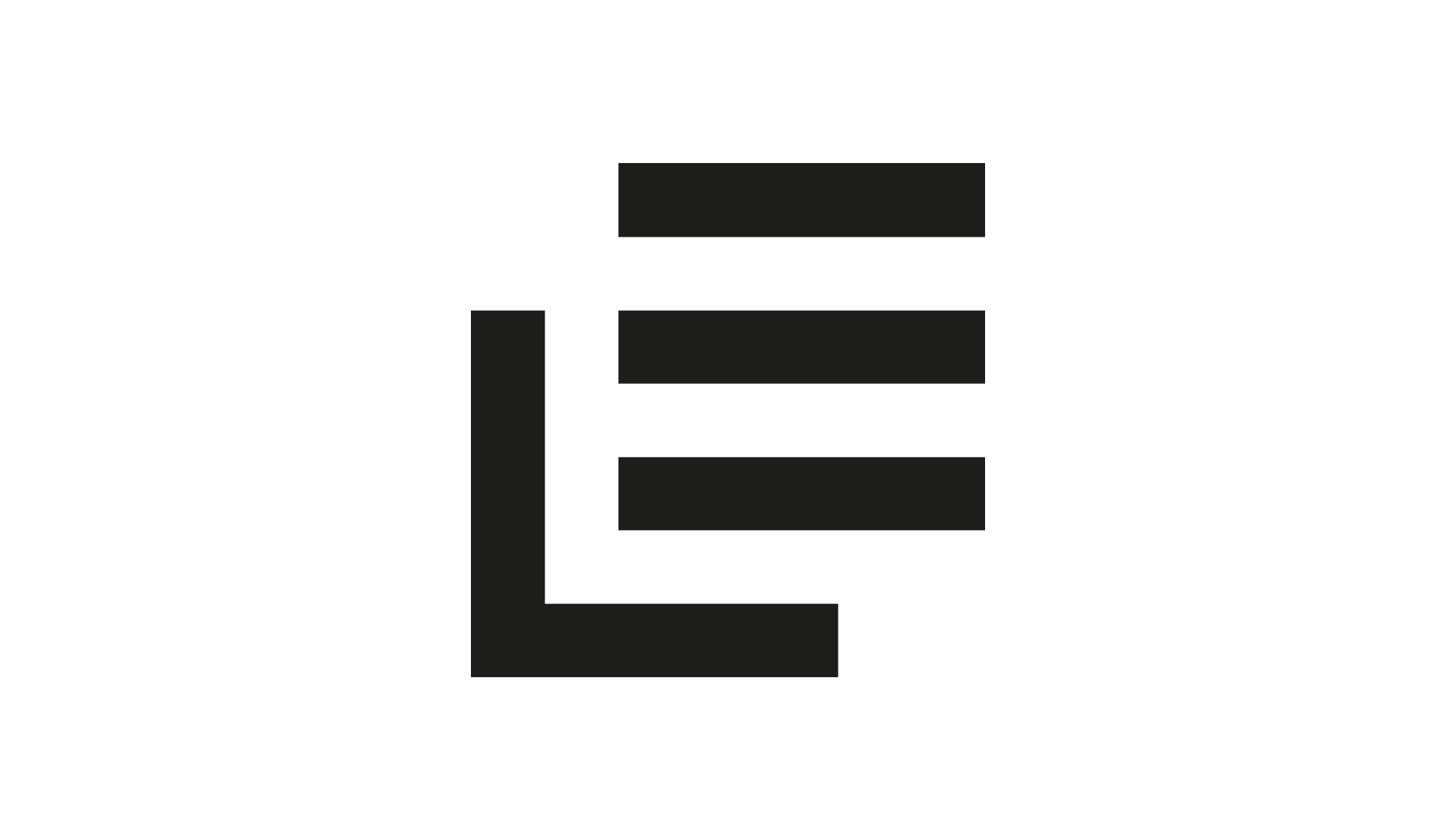
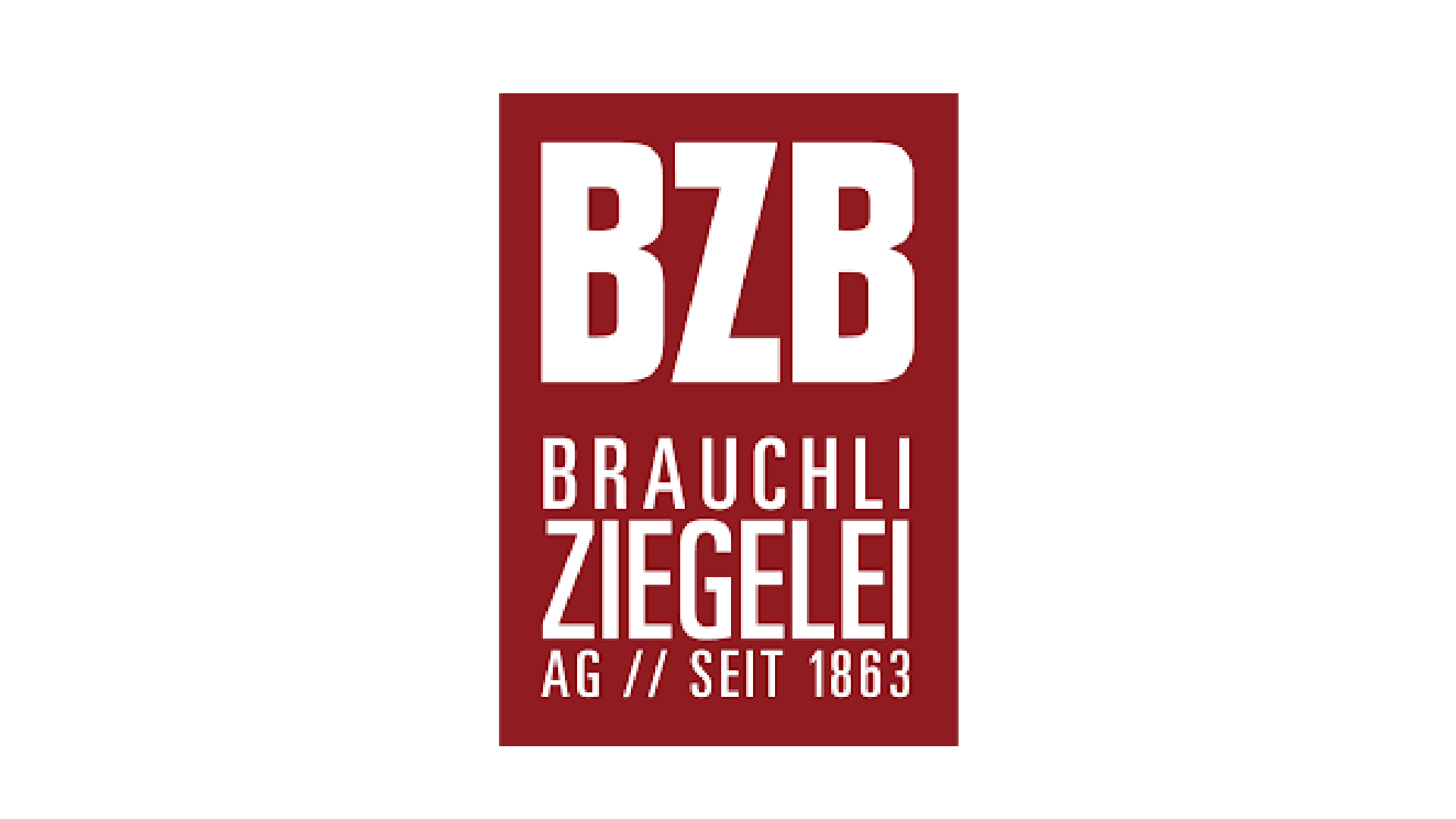
Digital Bamboo
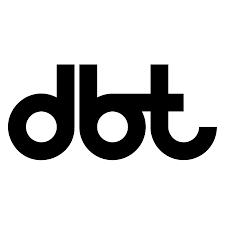
The pavilion explores using natural materials combined with digital fabrication technologies. This structure consists on a bamboo space truss, connected by 3D 380 bespoke printed joints (multijet fusion, direct metal sintering) and covered by a textile skin with a 3D printed reinforcement.
The use of computational design allowed optimization and formal exploration of complex structures. This high-performance structure cantilevers almost 5 meters in three directions, requiring minimal support. Post-tensioned cables reinforce the main load-bearing system. The geometry of the pavilion, consisting of more than 900 bamboo elements, was form-found using specifically developed digital tools.
Presented at: ZAZ (Zurich, Switzerland), Venice Biennale 2021 (Venice, Italy)
Construction: 2020, 2021
Credits & Publications
Fabrication, Process development, design: Digital Building Technologies, ETH Zurich
Teaching team: Marirena Kladeftira (Project lead), Matthias Leschok, Eleni Skevaki (Chair of Digital Building Technologies, ETH Zurich), Davide Tanadini (Chair of Structural Design, ETH Zurich), Yael Ifrah (MAS ETH DFAB coordination, Chair of Digital Building Technologies).
Support Structural Design: Dr. Ole Ohlbrock, Dr. Pierluigi D’Acunto (Chair of Structural Design, ETH Zurich)
Design Development MAS ETH DFAB 19-20 Students: Maria Pia Assaf, Jomana Baddad, Frederic Brisson, Yu-Hung Chiu, Rémy Clemente, Ioulios Georgiou, Mahiro Goto, Anton Johansson, Laszlo Mangliar, Dinorah Martinez Schulte, Edurne Morales Zuniga, Fatemeh Salehi Amiri, Emmanuelle Sallin, Indra Santosa, Eliott Sounigo, Chanon Techathuvanun, Ping-Hsun Tsai
Partnerships: HS High-Tech
Supporting technicians: Christian Egli, Tobias Hartmann, Michael Lyrenmann, Thomas Posur, Andrea Perissinotto, Andreas Reusser.
Photos: DBT (Marirena Kladefira, Dinorah Martínez Schulte, Amelie Bargetzi, Andrei Jipa, Matthias Leschok)
Publications: Voxel Matters
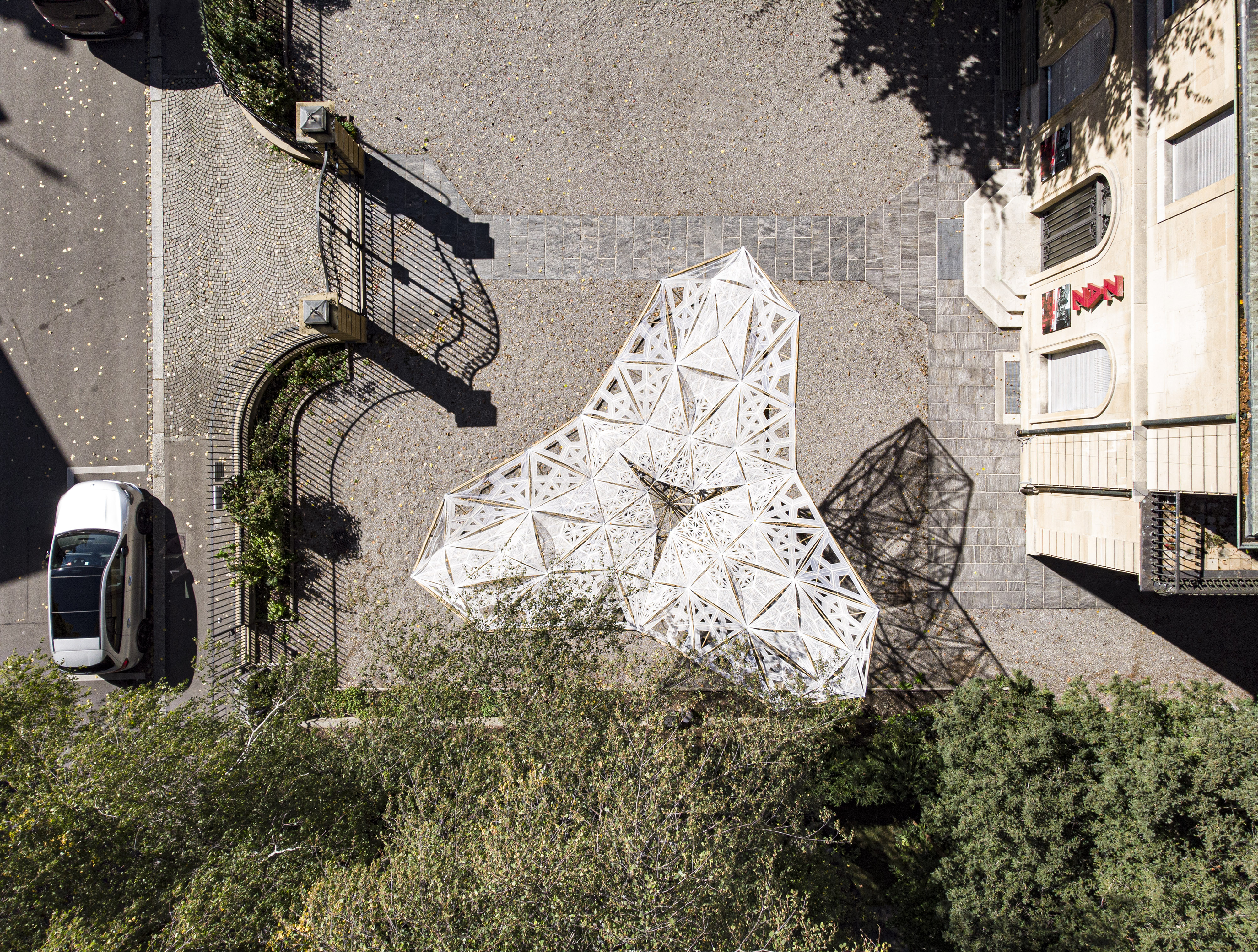
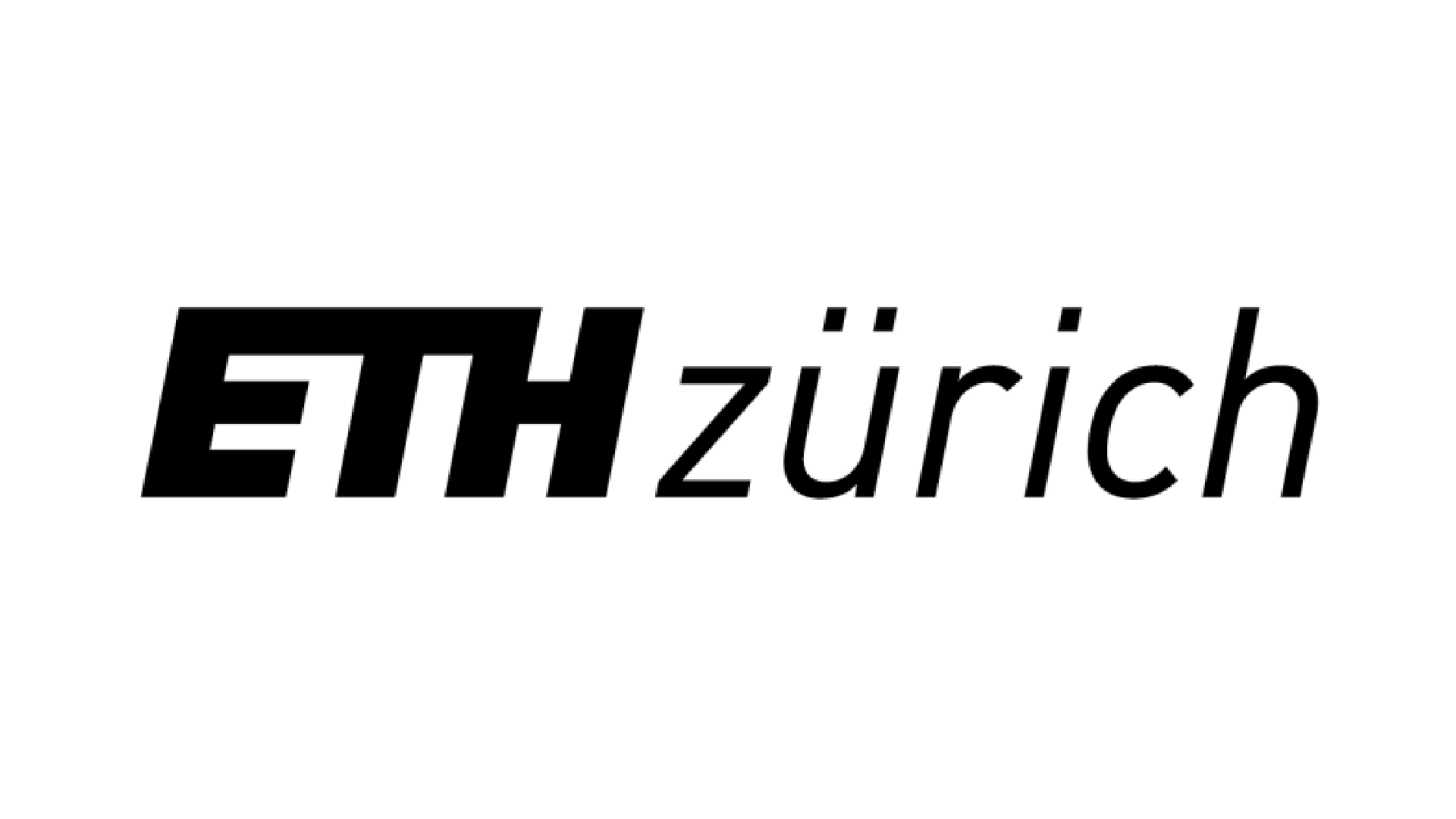
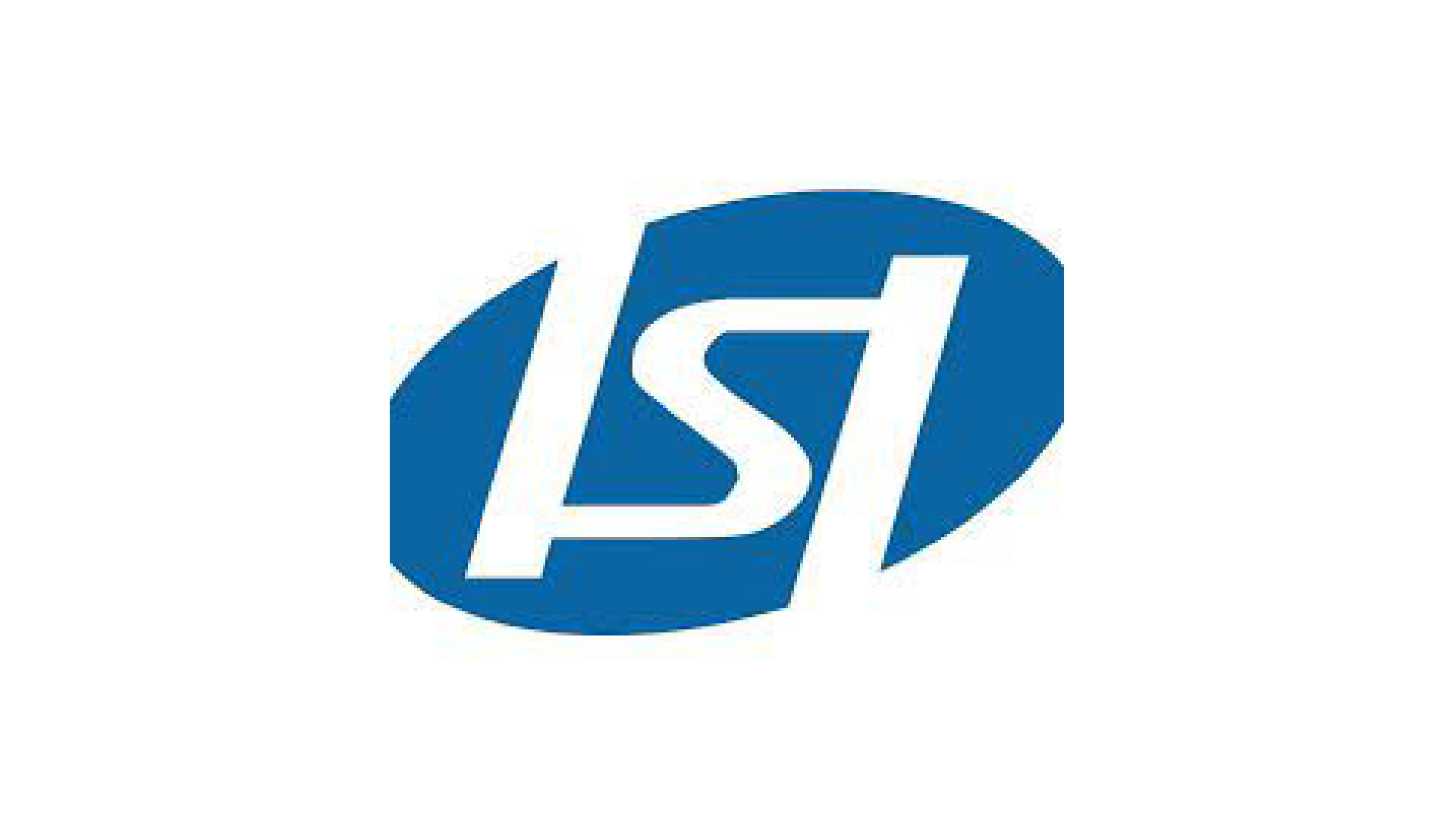
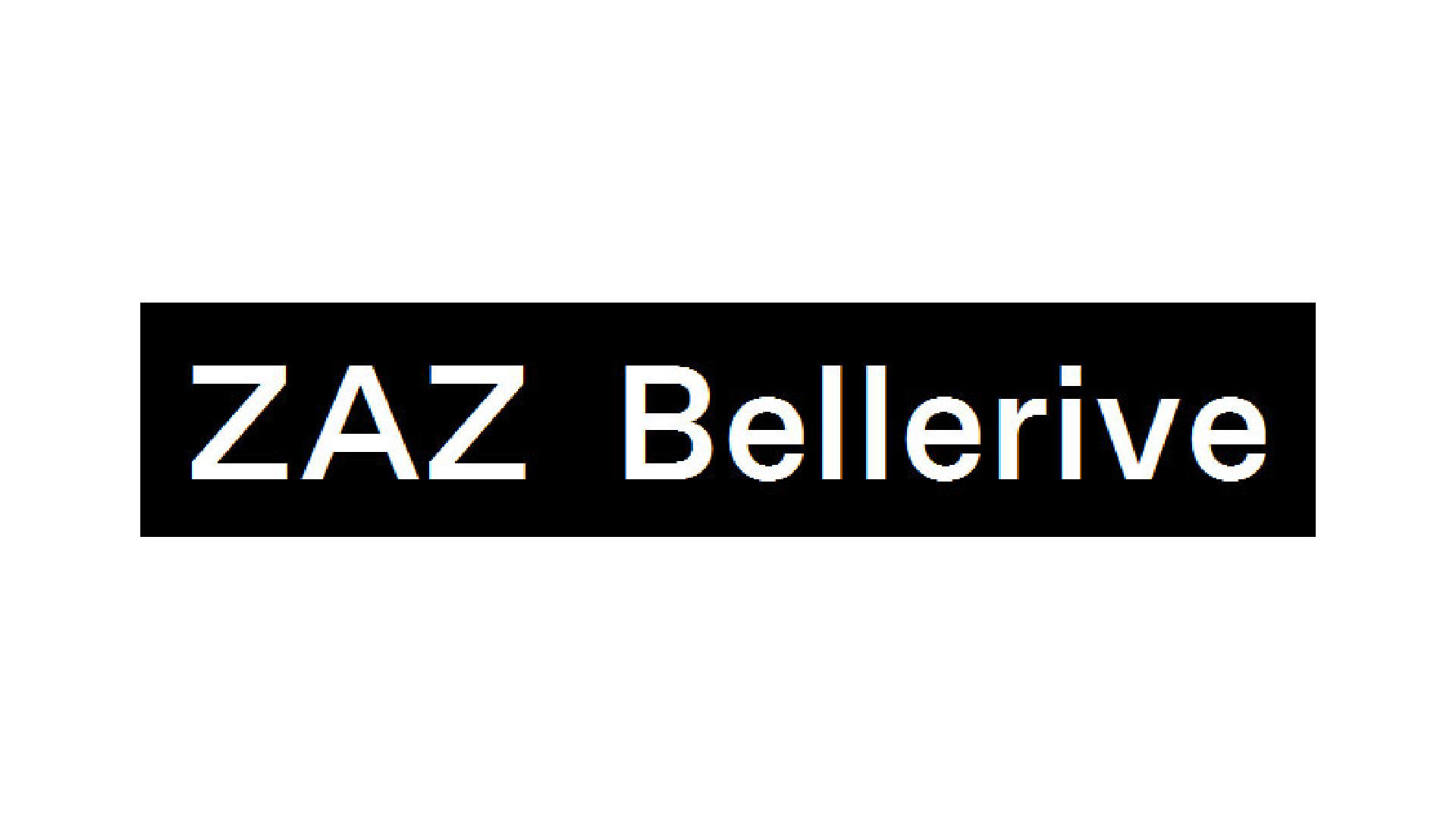
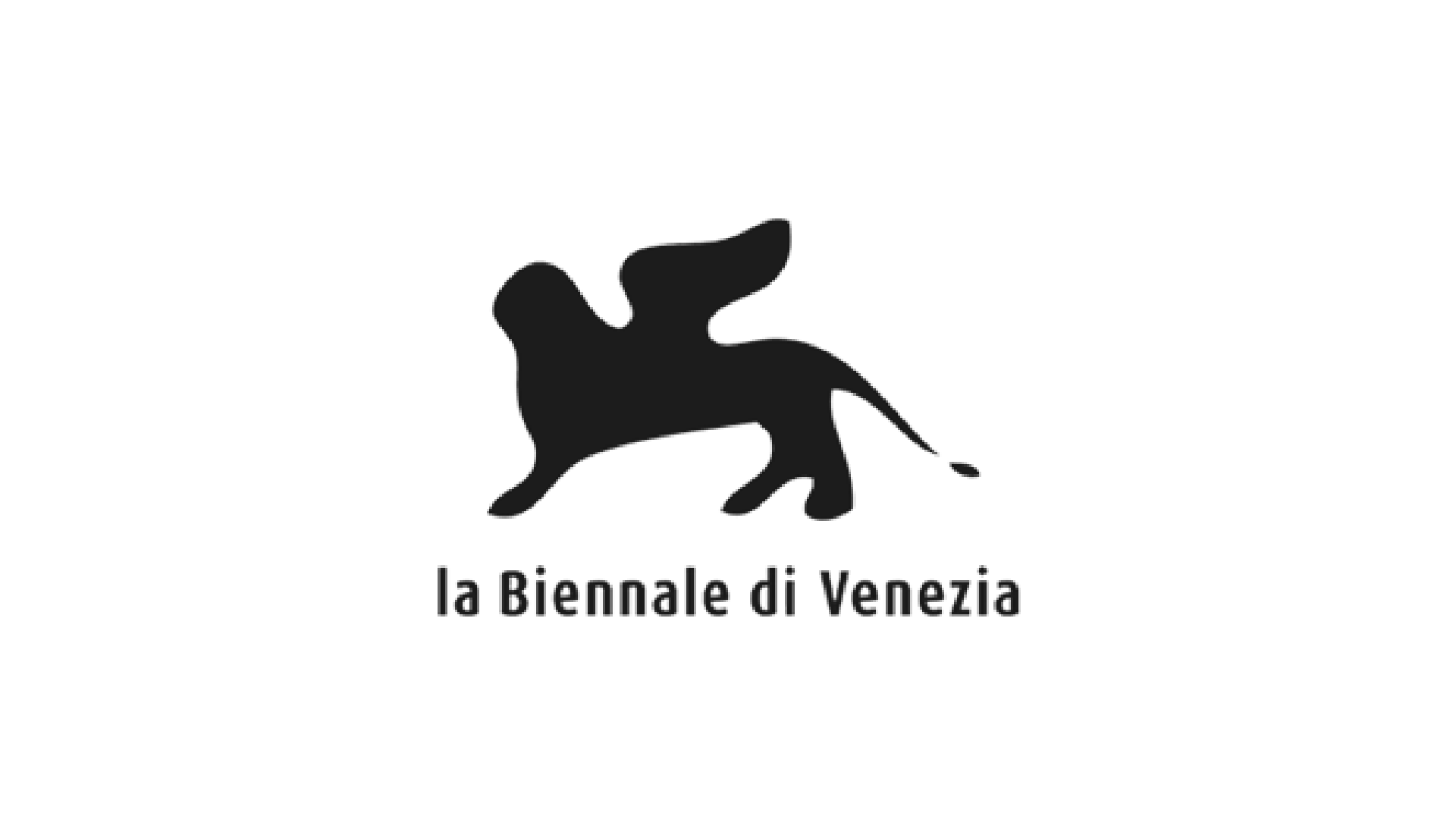
Discrete Concrete Spine
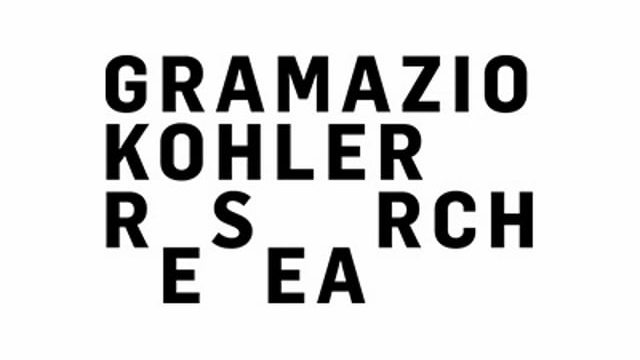
This project was inspired by double-curved architecture and the freedom of eggshell technology (concrete casting with 3D-printed plastic formwork). We decided to design an element that would not be limited by architectural archetypes: where the limit between wall, capital, and column dissolved.
The shape comes from the idea of a continuous nucleus based on a spine. This axis was then split vertically to generate the sections and horizontally to connect between the levels. This spine is then extruded to create a continuous horizontal area.
A post-tensioning cable is meant to connect and reinforce the elements, which are inter-connected through a male-female joint.
Developed at: MAS ETH DFAB 1920
Credits
Team: Laszlo Mangliar, Edurne Morales, Eliott Sounigo
Teaching Team: Gramazio Kohler Research, ETH Zurich – Joris Burger, David Jenny
Sponsors: extrudr and Lafarge Holcim
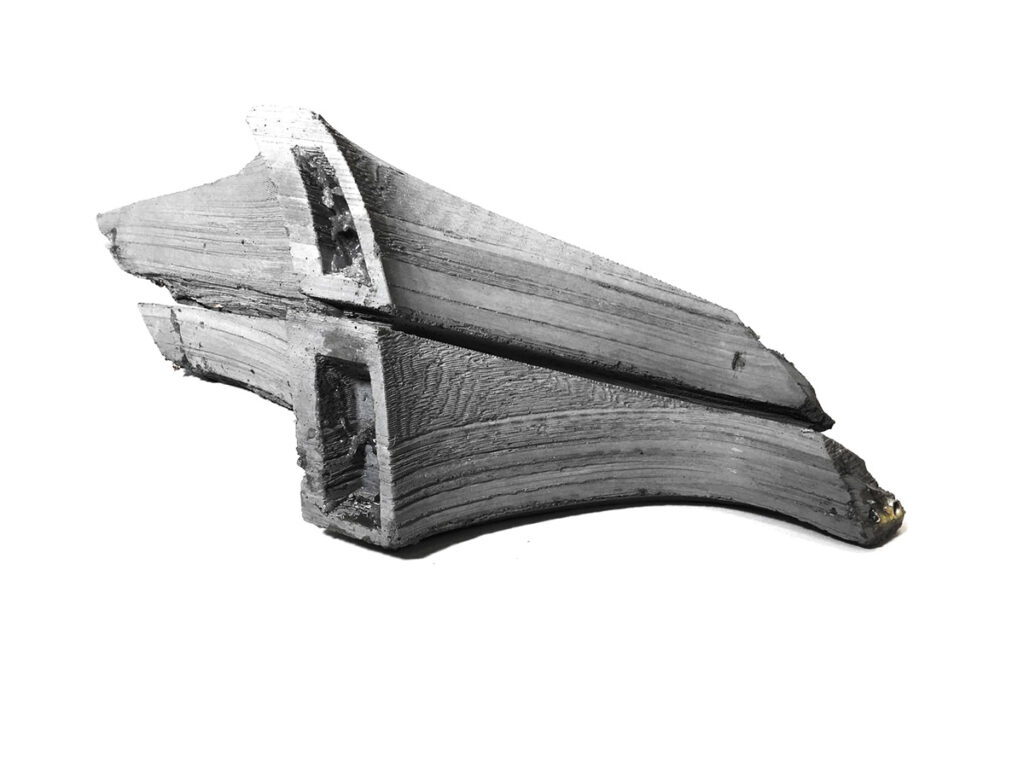
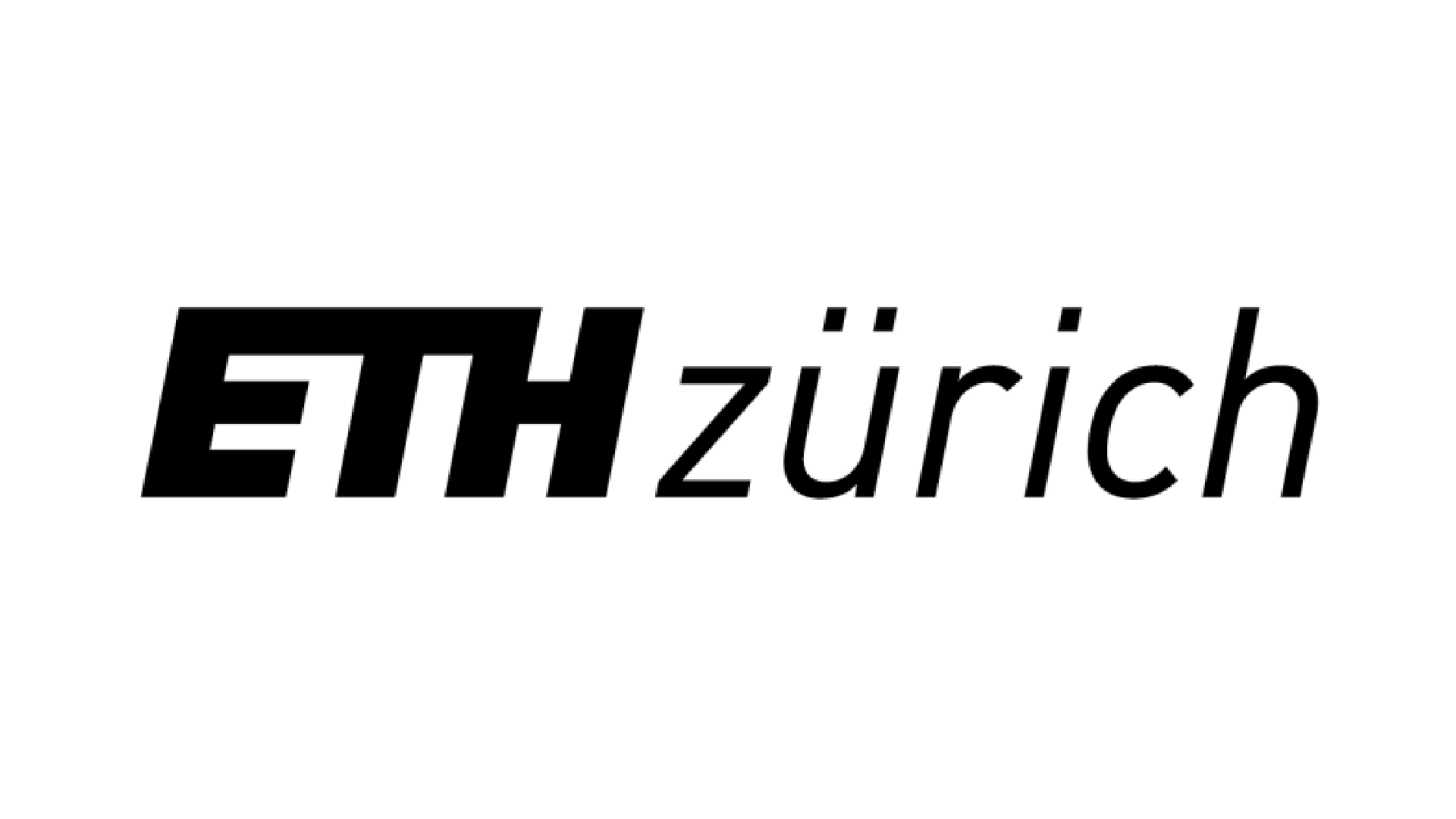
TropiCRETE
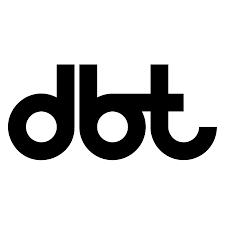
Facade elements fabricated using concrete 3D printing. The design concept focuses on countries with tropical weather, aiming to control the interior temperature by using an optimized element that answers to the radiation analysis of the particular location of the building.
The information is transferred to parameters that are used to control the openings of the segments.
Developed at: MAS ETH DFAB
Credits
Team: YuHung Chiu, Chanon Techathuvanun, Edurne Morales Zuniga
Teaching Team: Digital Building Technologies, ETH Zurich – Ana Anton, Eleni Skevaki
Photos: team and Axel Cretten
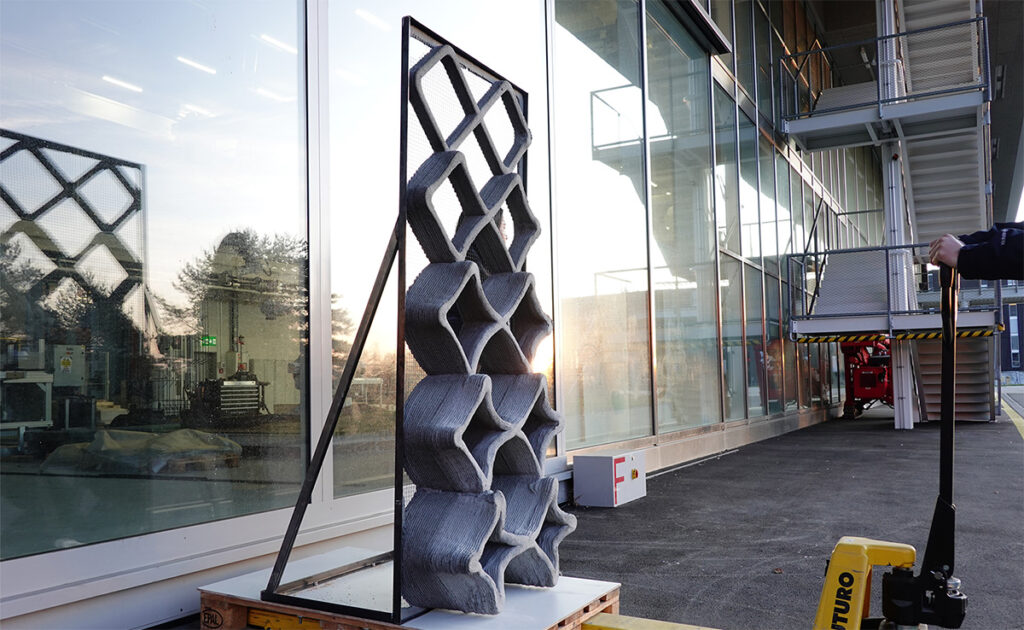
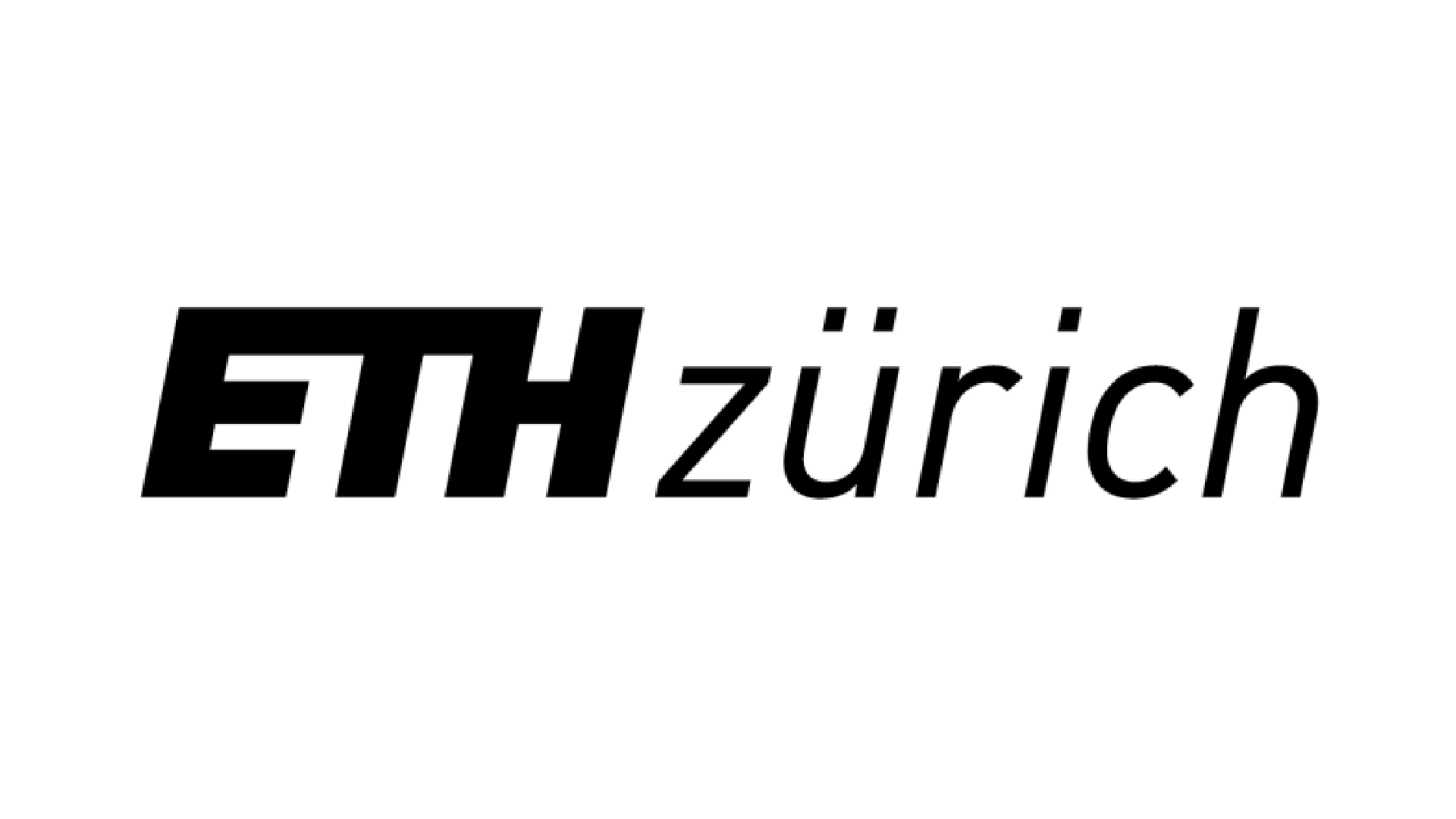
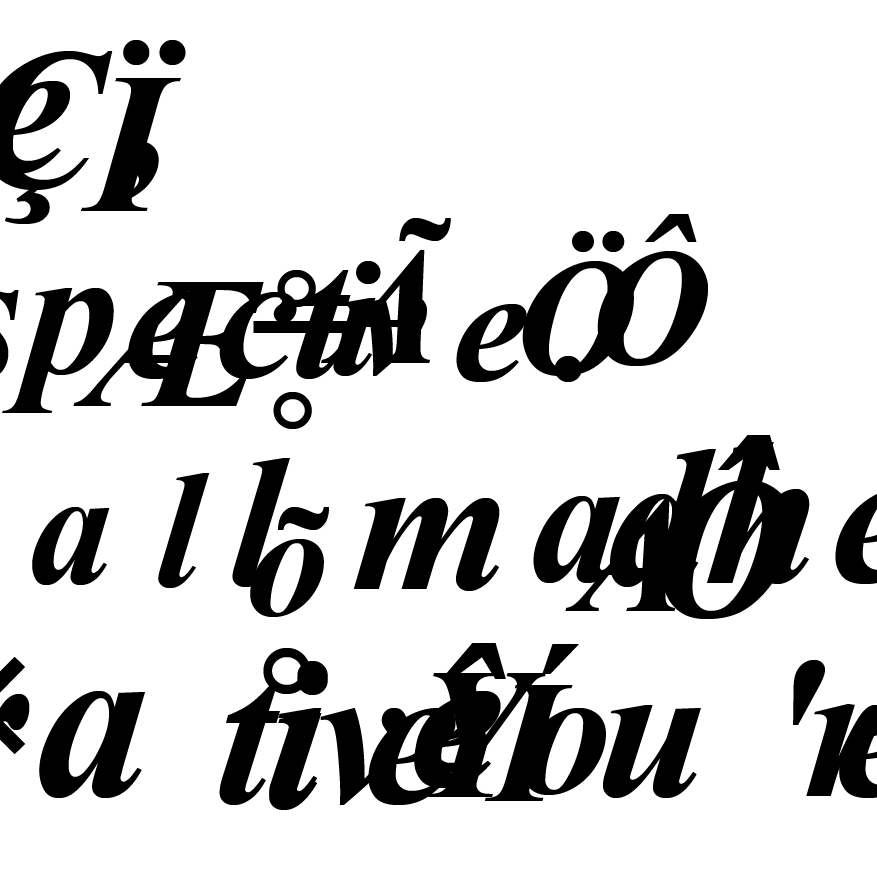
maeid
Magic Queen
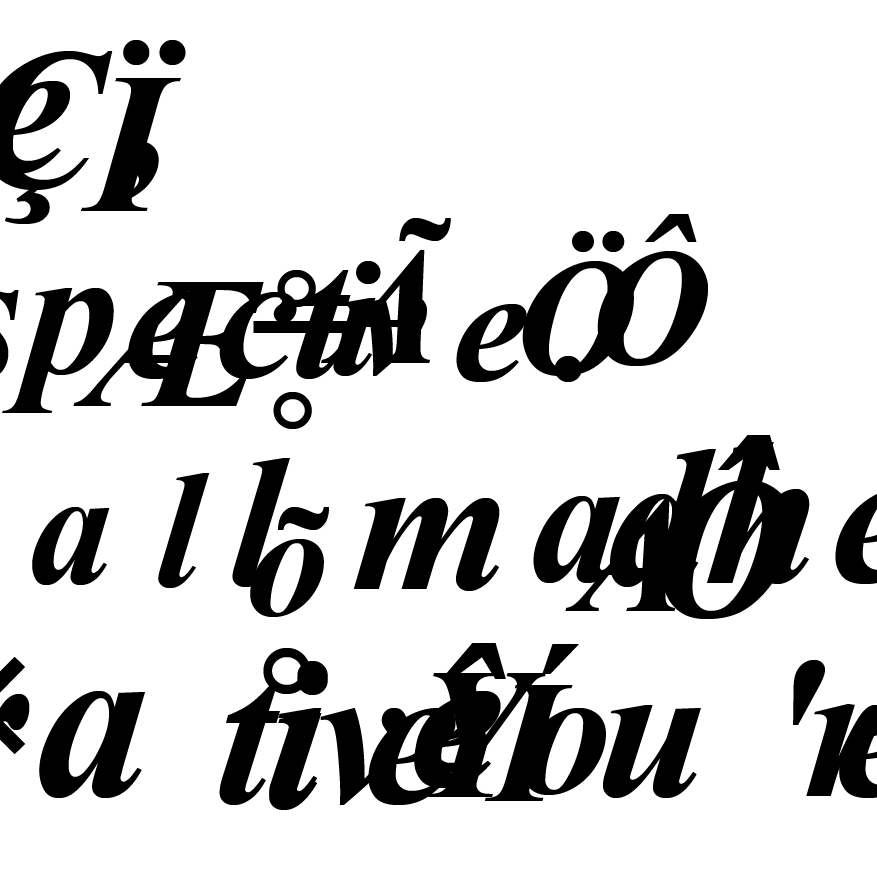
This hybrid environment seeks to incorporate and fuse biological systems with organic materials and machines, generating an ecosystem of empathy and coexistence with the creation of an ecology of non-human subjects. Nurturing, and restoring itself with the use of sensors and machine learning.
The landscape itself is built robotically with the use of natural binders and compaction, having the possibility of going back to nature after the exhibition. This process builds up organic figures of only previous digital existence.
Built for: Venice Biennale 2021
Credits & Publications
Fabrication, Process development, design: MAEID – Daniela Mitterberger, Tiziano Derme
Project Team: Alex Karaivanov, Noor Khadher, Andrea Cancian
Structural System: Johann Riebenbauer
Fabrication Team: Marina Edurne Morales Zuniga, Bahar Al Bahar, Rodrigo Perez Hernandez, Andreea Bunica
Student Workshop: Julian Edelmann, Federico Gomarasca, Raphaela Elisabeth Haller, Ludwig-Valerius Rieger, Thomas Victor Philippe Sicouri, Zeno ZoppiVisual Interface: Andrea ReniMusic and Sound Design: Lukas Lauermann, LOREM, Luca PaganAI and machine vision system: Martin Gasser
Supported By: ABB, Bundeskanzleramt Wien / Federal Chancellery Republic of Austria, Universität für Angewandte Kunst Wien, Stadt Graz, Land Steiermark, Leopold-Franzens-Universität Innsbruck – Institut für Experimentelle Architektur, Department of Microbiology
Photography: Zita Oberwalder, MAEID
Publications: Designboom
🔗 MAEID
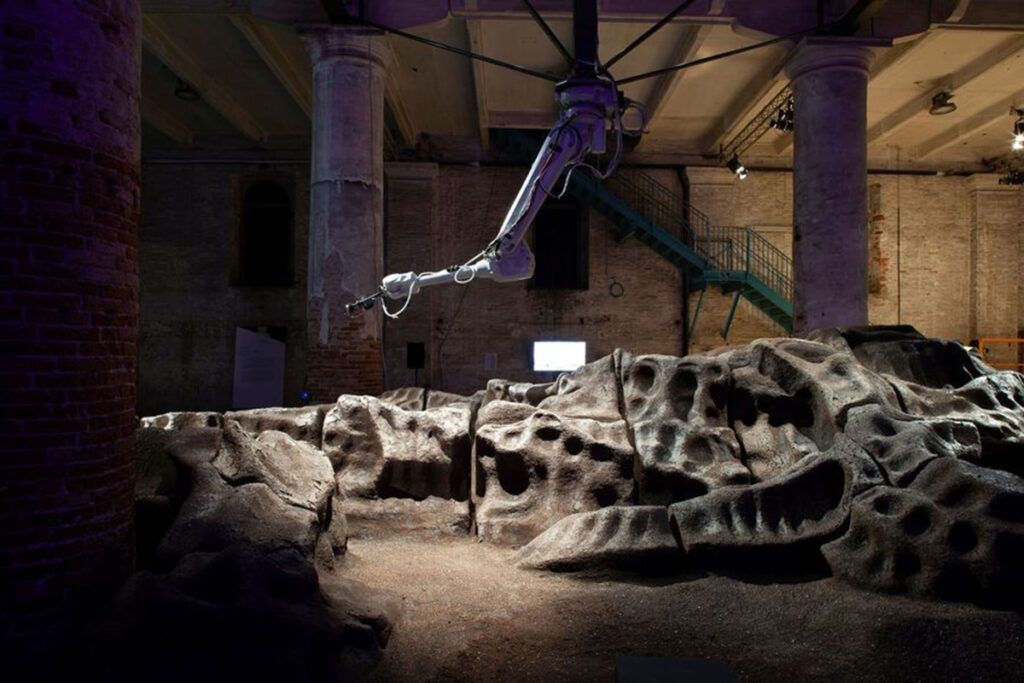
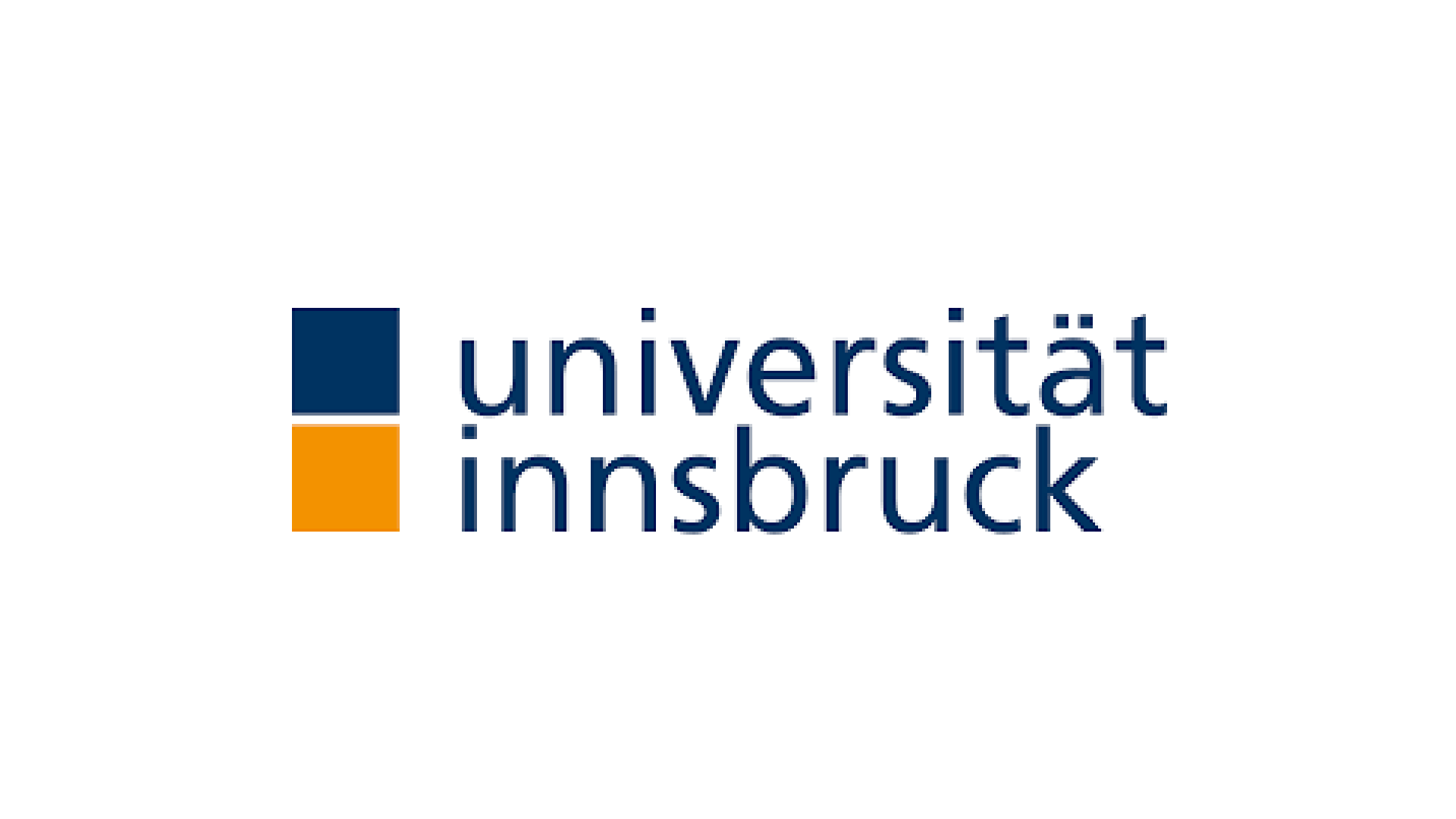
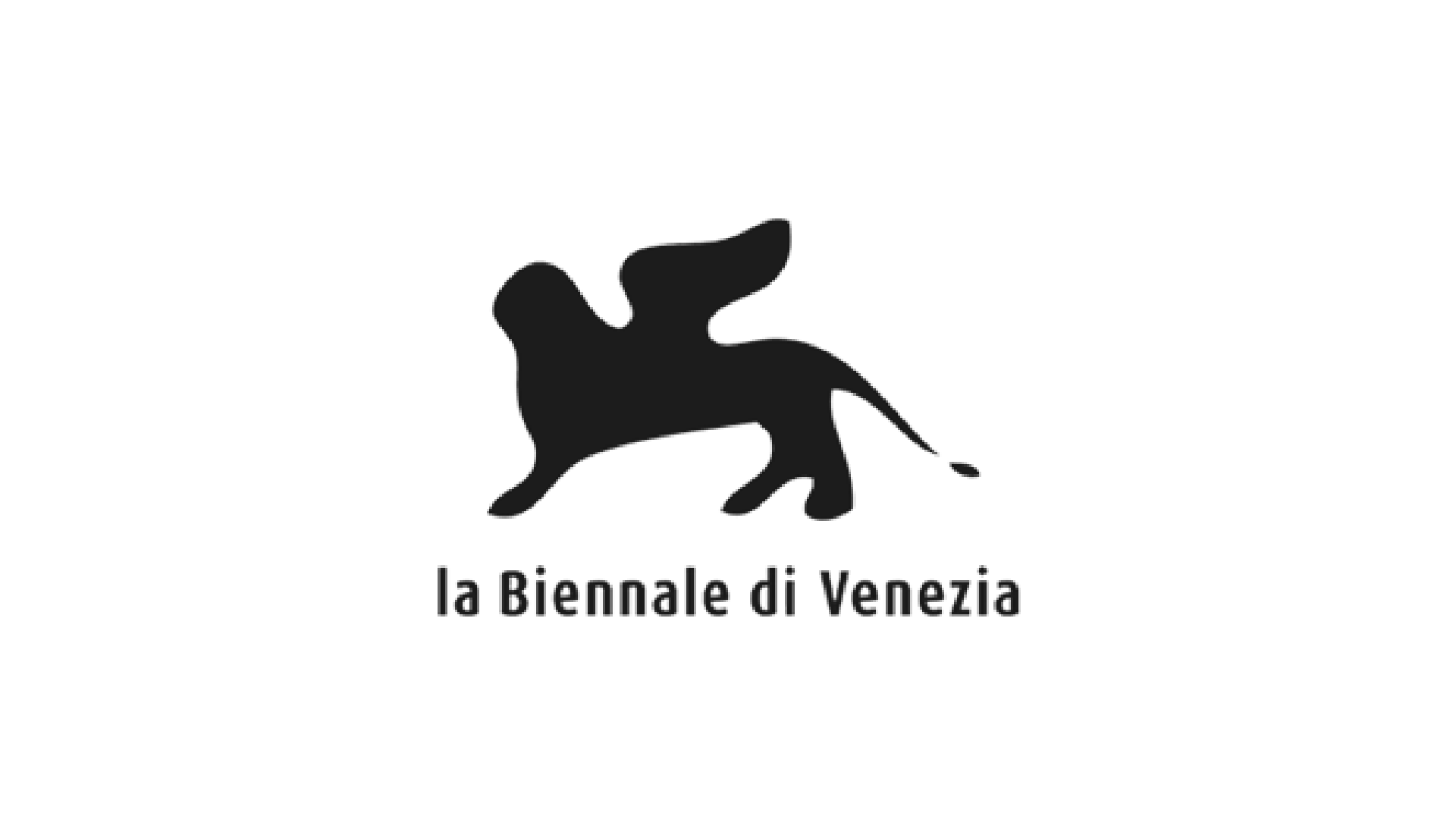
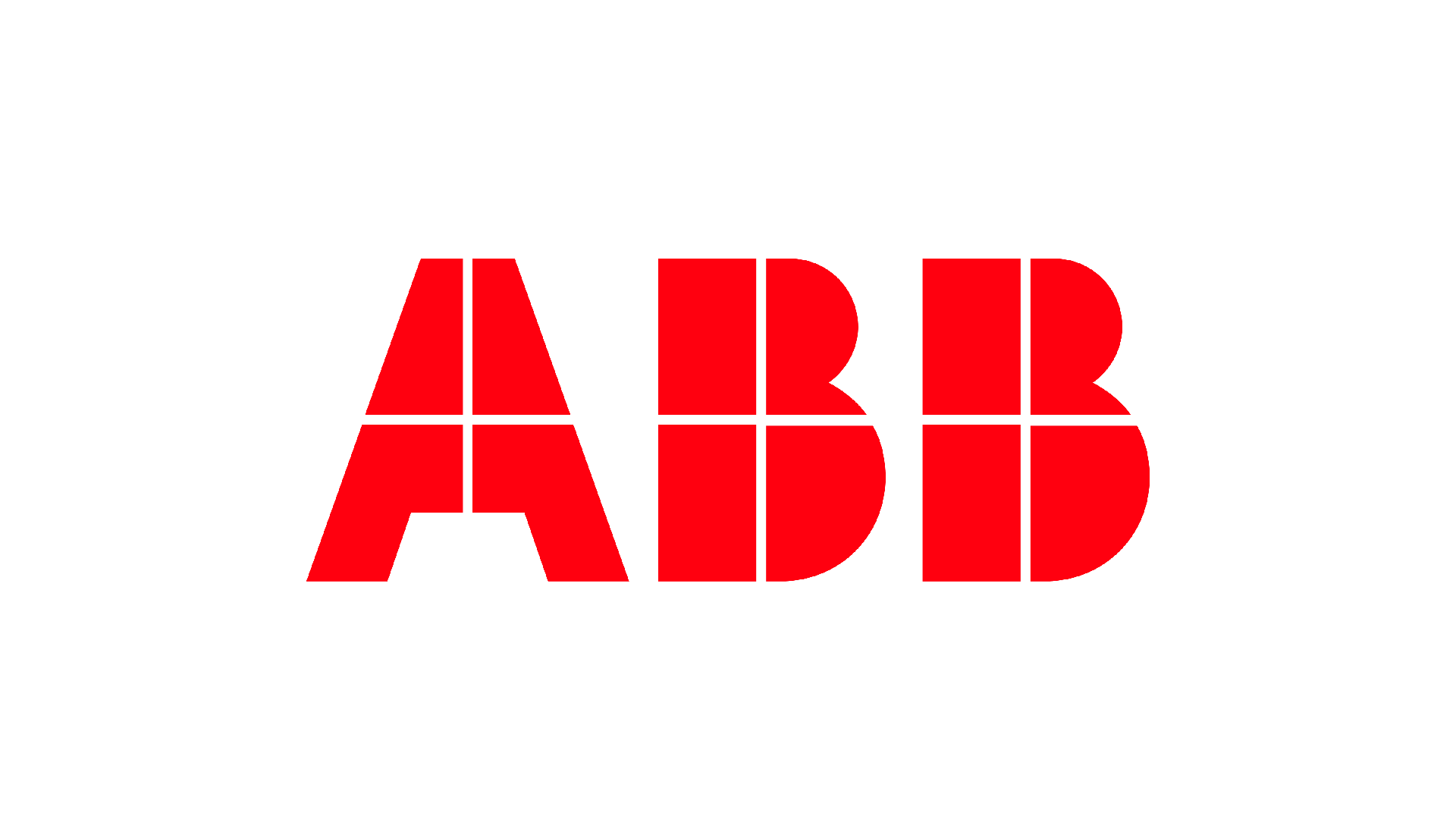
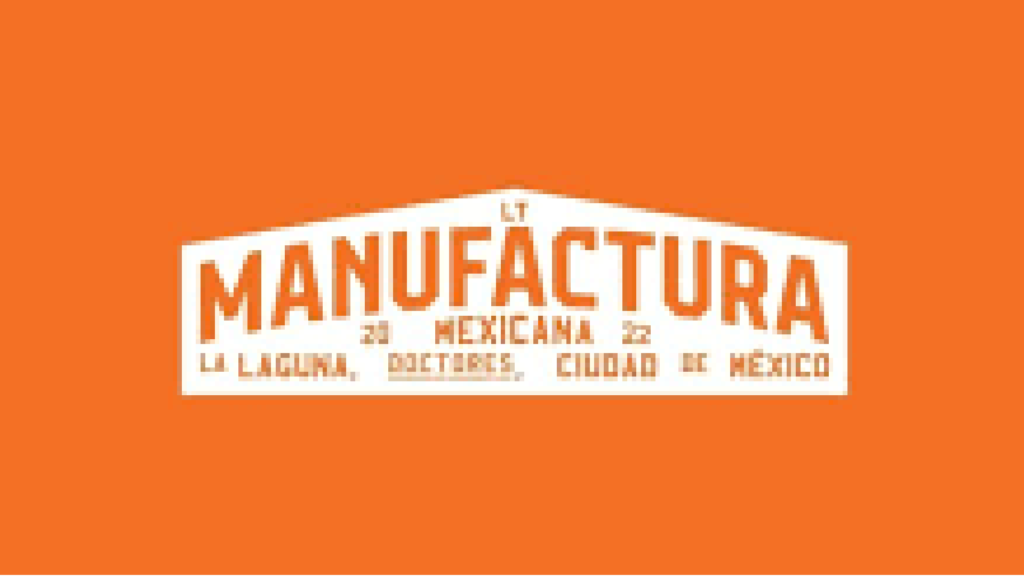
MANUFACTURA
EGGSHELL Brick
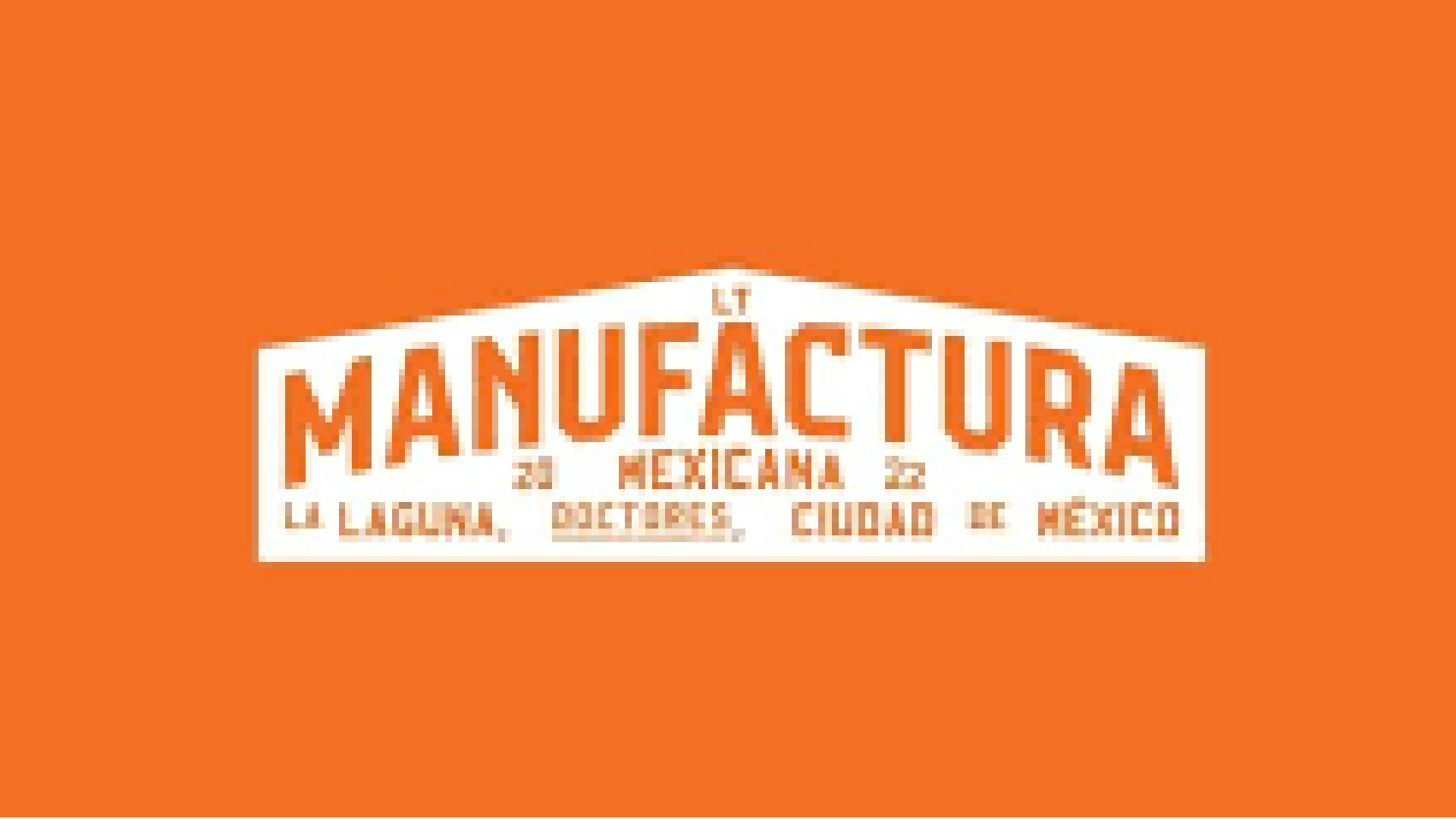
Mexico is one of the main egg producers worldwide, taking advantage of this we decided to develop a bio-composite that reuses eggshell waste.
Our waste is turned into robotically fabricated architectural elements… EGGSHELL Bricks, that can be completely decomposed and are completely organic.
This specific demonstrator consisted of a self-standing sine curve-based wall, based on 105 discrete bricks. All the waste used for the project was based on the donation of local businesses.
Presented at: Design Week Mexico 2022 (Colección Inédito)
Awards: Design Week Mexico 2022 (Honorable Mention), What Design Can Do (Finalist), 3D Pioneers (Finalist), Dezeen Awards 2023 (Nomination), Green Product Award 2024 (Finalist), Make It Circular Challenge (Winner)
Credits & Publications
Fabrication, Process development, design: MANUFACTURA + Montserrat Ayala
Project Team:
Manufactura – Dinorah Schulte (co-founder, project director), Edurne Morales (co-founder, computational design) y Eduardo Barba (co-founder)
Cal Viva – Montserrat Ayala (material development)
Collaborators: Santiago Rangel, Aleida Rahel Merkel y Natalia Juan
Material donation: Rosetta, Rosetta Panadería, LARDO, Rancho Rio Blanco y BOU
Photos: Arturo Arrieta, Enrique Aguilar, Elena Fierro, Dinorah Martínez Schulte
Publications: Green Product Award, Voxel Matters, 3D Printing Industry, The Praxis Journal
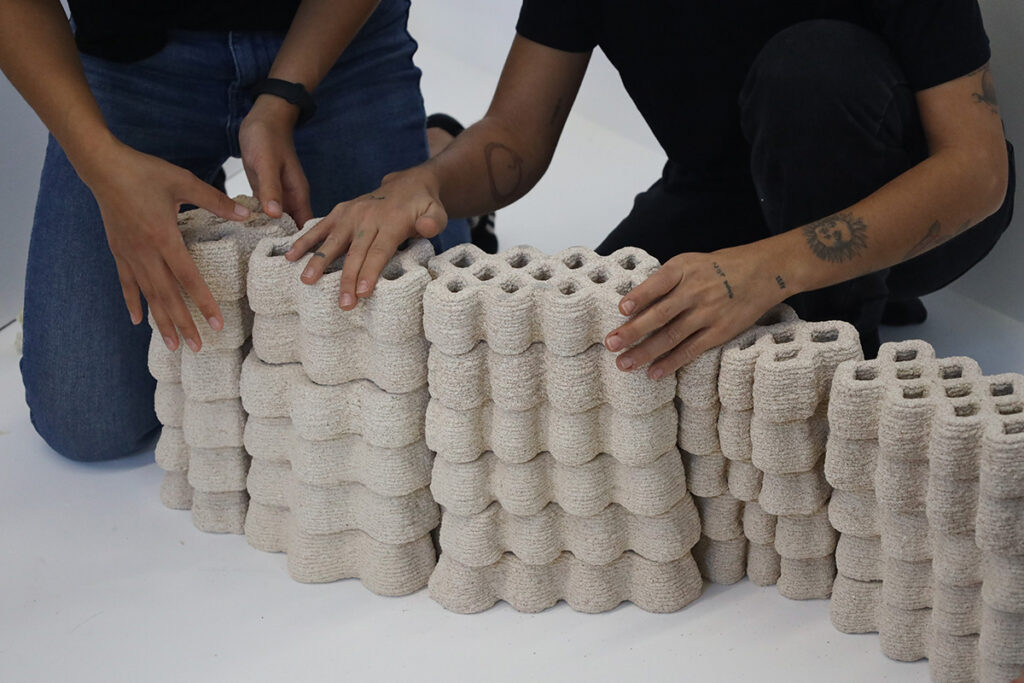
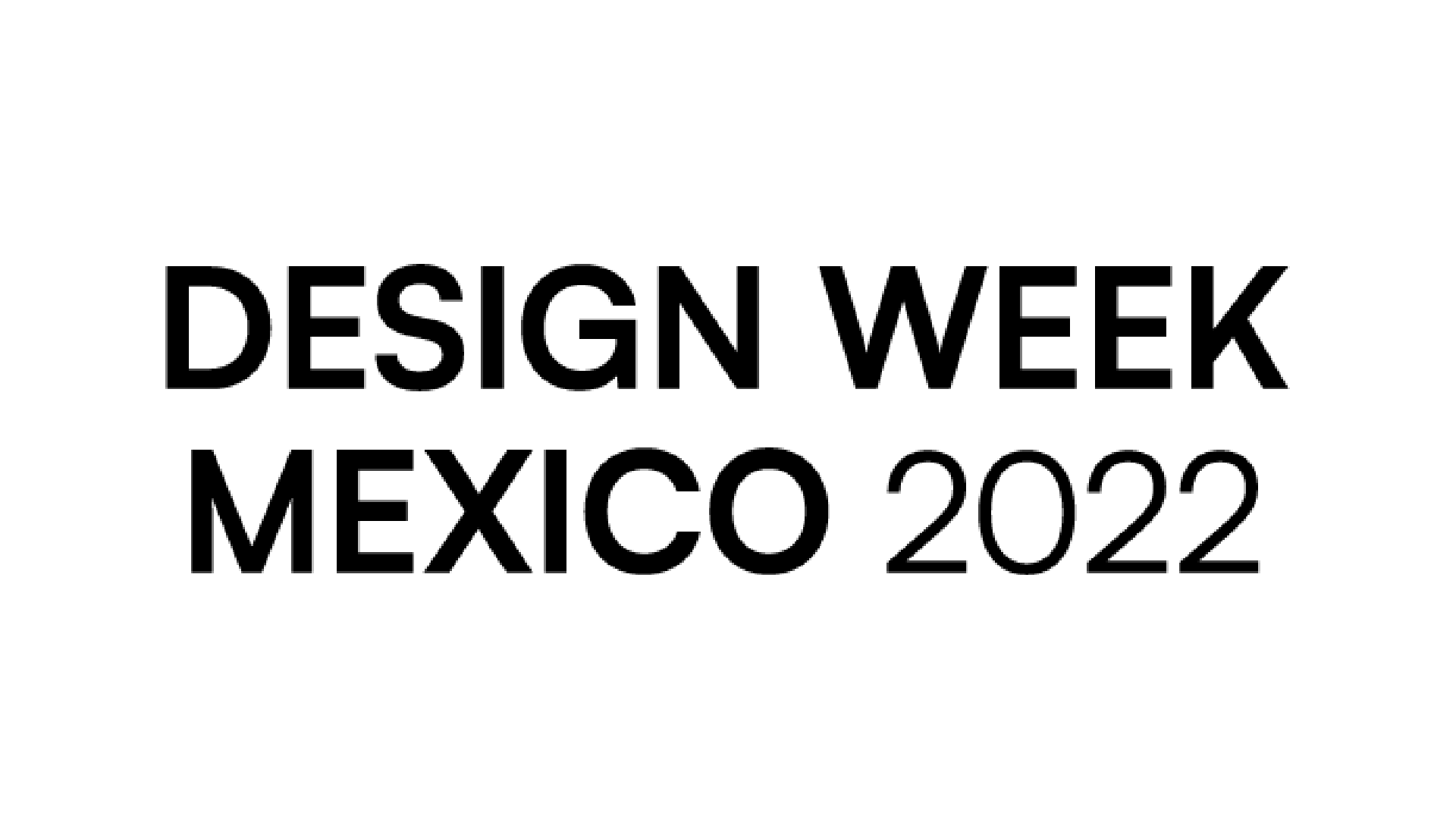
EGGSHELL Column
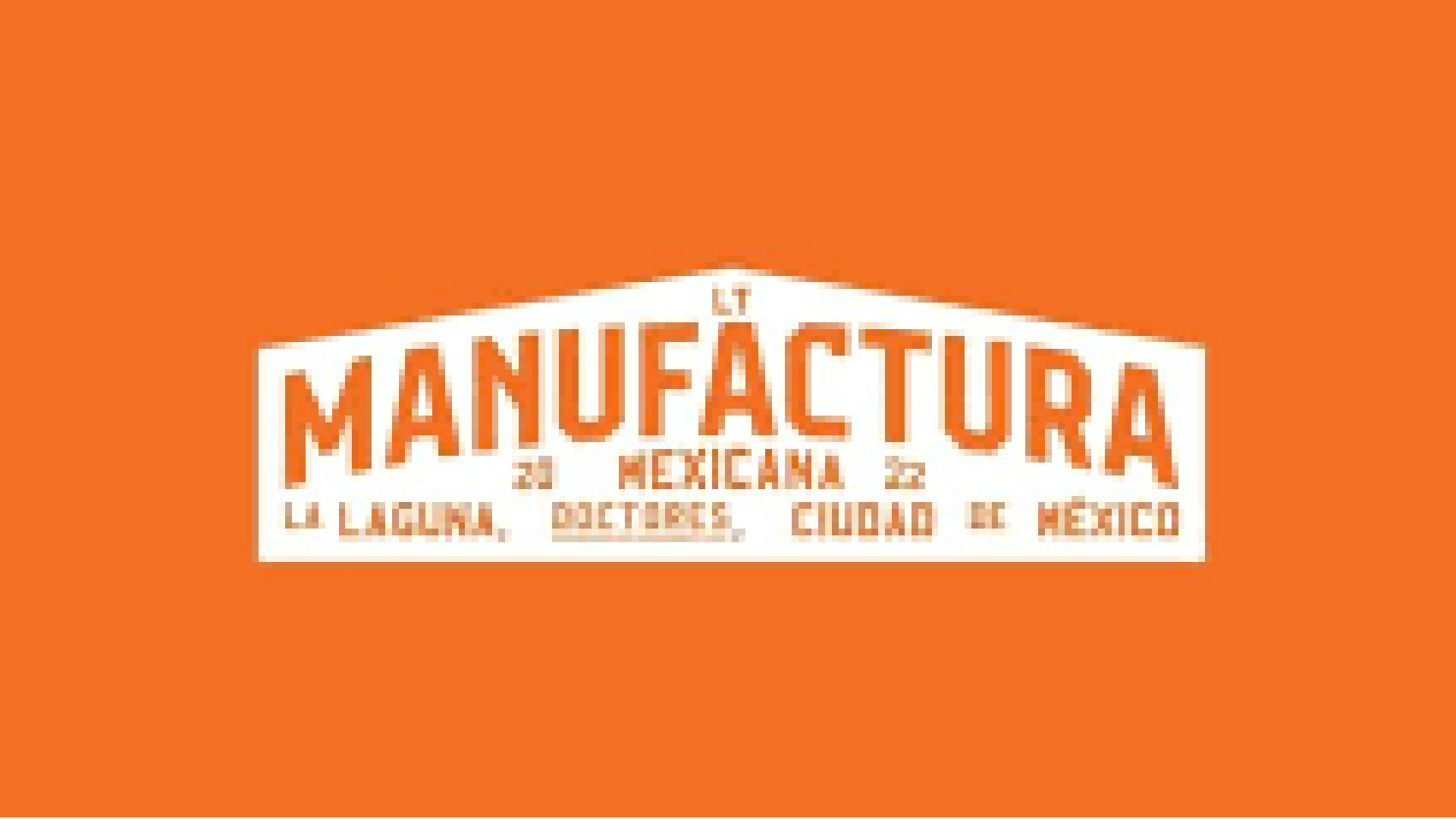
Eggshell Column is also part of the EGGSHELL Project, the ongoing development of an eggshell-based bio-composite.
In this case, the 3 legs of the column together with the stiffness of the material help maintain the support of the spiraling structure.
The infill of the structure has been a direct response to the characteristics of the material and process. Providing support to the circular sections through their angle limits that adapt computationally to the scale.
Presented at: Zona Maco 2023
Credits & Publications
Fabrication, Process development, design: MANUFACTURA + Montserrat Ayala
Project Team: Manufactura – Dinorah Schulte (co-founder, project director), Edurne Morales (co-founder, computational design) y Eduardo Barba (co-founder)Cal Viva – Montserrat Ayala (material development)
Guest Designer: Maria Pia Assaf
Collaborators: Santiago Rangel, Aleida Rahel Merkel y Natalia Juan
Material donation: Rosetta, Rosetta Panadería, LARDO, Rancho Rio Blanco y BOU
Photos: Arturo Arrieta, Enrique Aguilar, Dinorah Martínez Schulte
Publications: CoolHunter Mx, Design Boom,

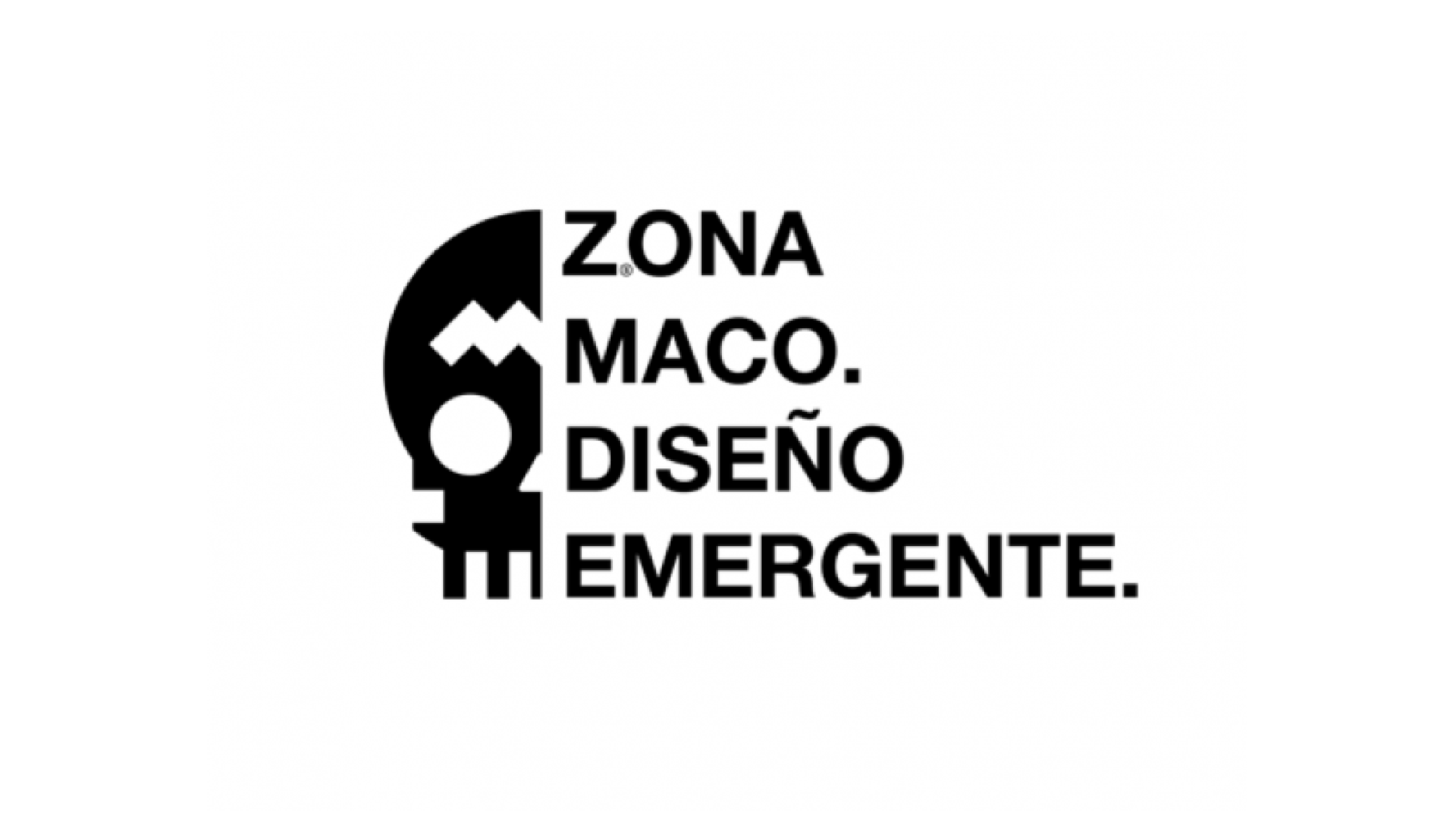
WOOD Project
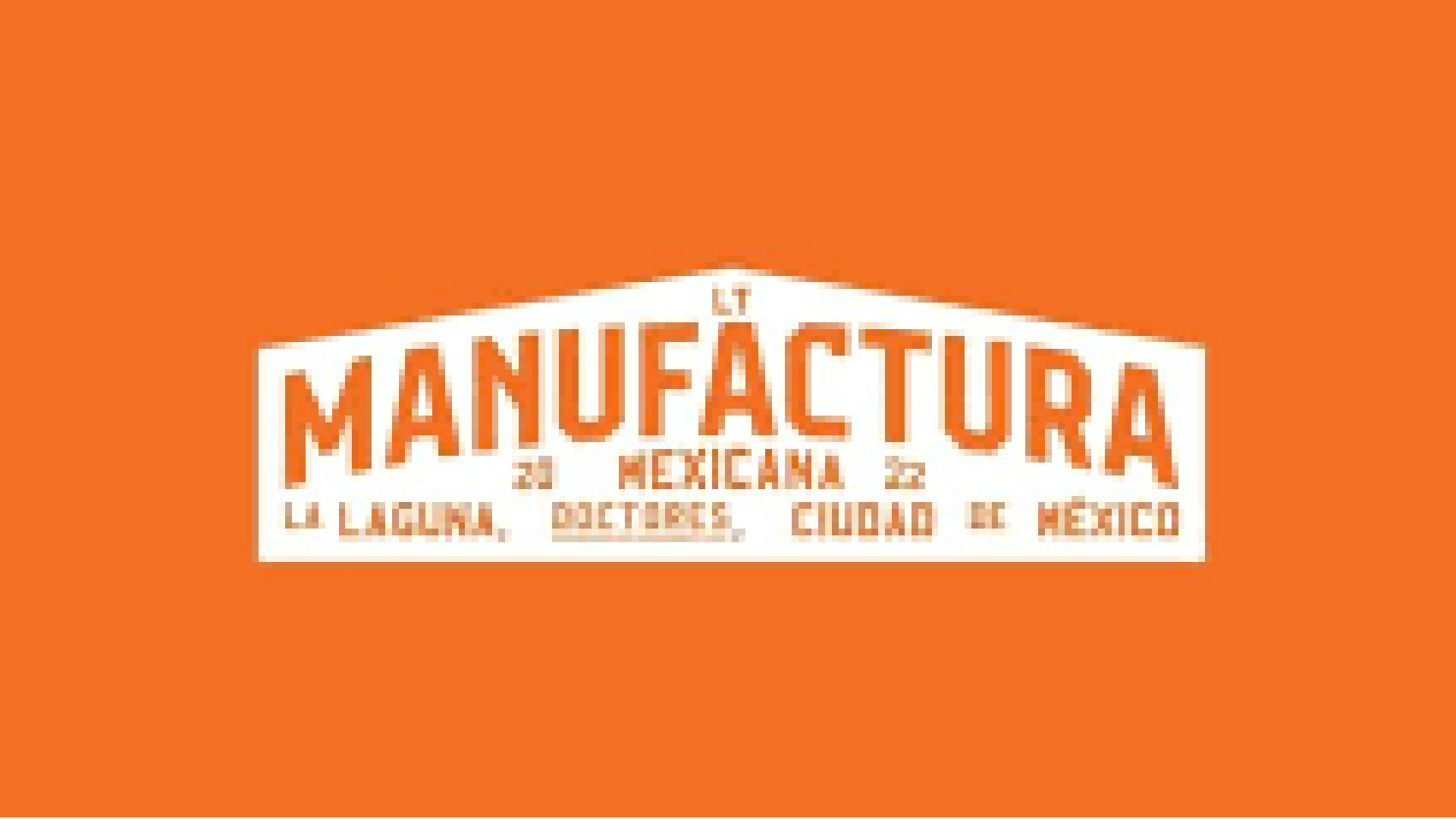
This project/research in collaboration with La Metropolitana, a furniture manufacturing and design workshop that combines traditional wood manufacturing with cutting-edge technologies.
They currently produce 4-6 bags of sawdust from multiple species in their daily activities, material that is rarely taken advantage of.
This material takes advantage of this fact to repurpose this high-quality material sustainably, using bio-binders as the matrix.
Manufactured for: LUUNA Showrooms
Production: 2022
Credits & Publications
Fabrication, Process development, design:
MANUFACTURA + La Metropolitana
Client: LUUNA
Project Team:
Manufactura: Dinorah Schulte (co-founder, project co-director), Edurne Morales (co-founder, computational design, design), Eduardo Barba (co-founder)
La Metropolitana: Rodrigo Escobedo (co-founder / project co-director), Fabricio Vazquez (collaborator), Brando Marín (collaborator)
Material Development: Montserrat Ayala in collaboration with La Metropolitana
Manufactura Collaborators: Santiago Rangel, Jared Zarate
Material Donations: La Metropolitana
Photography: Enrique Aguilar, Sebastian De Casa, Dinorah Martínez Schulte
Publications: Parametric Architecture, Rhino3Dzine, 3DPrinting.com, Material District
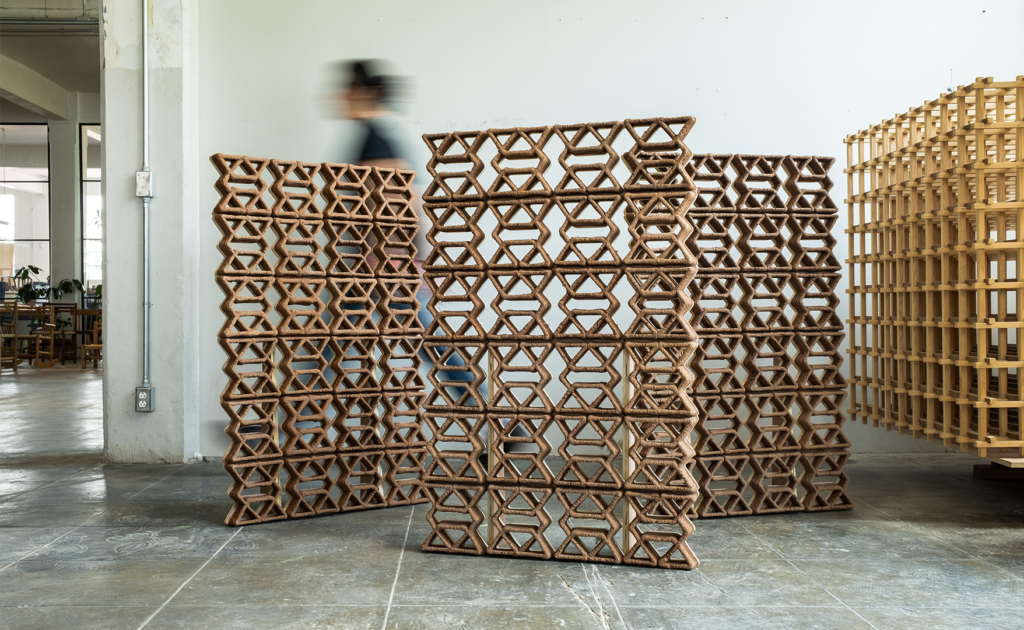
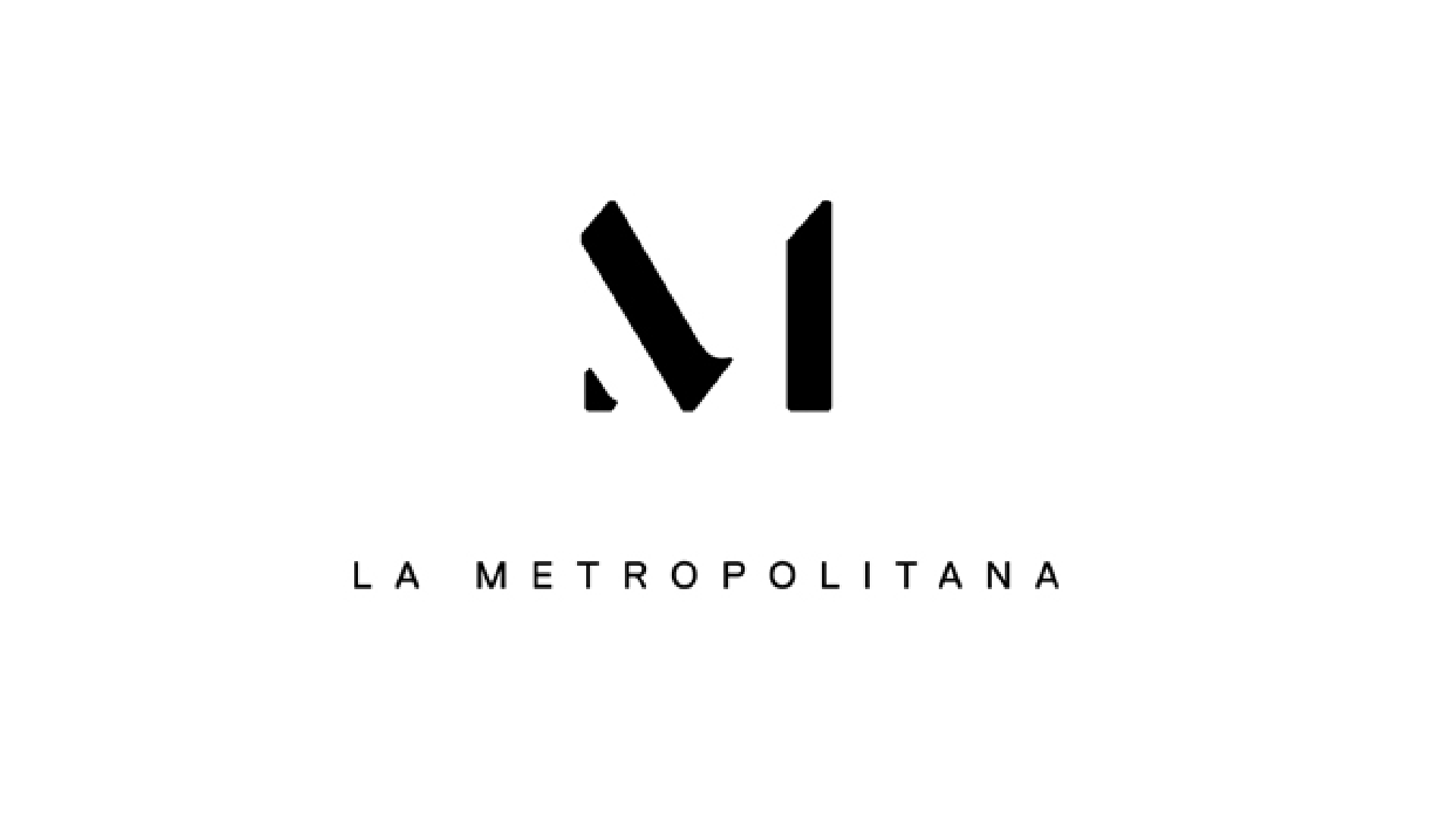
Sueños con Tierra/Concreto
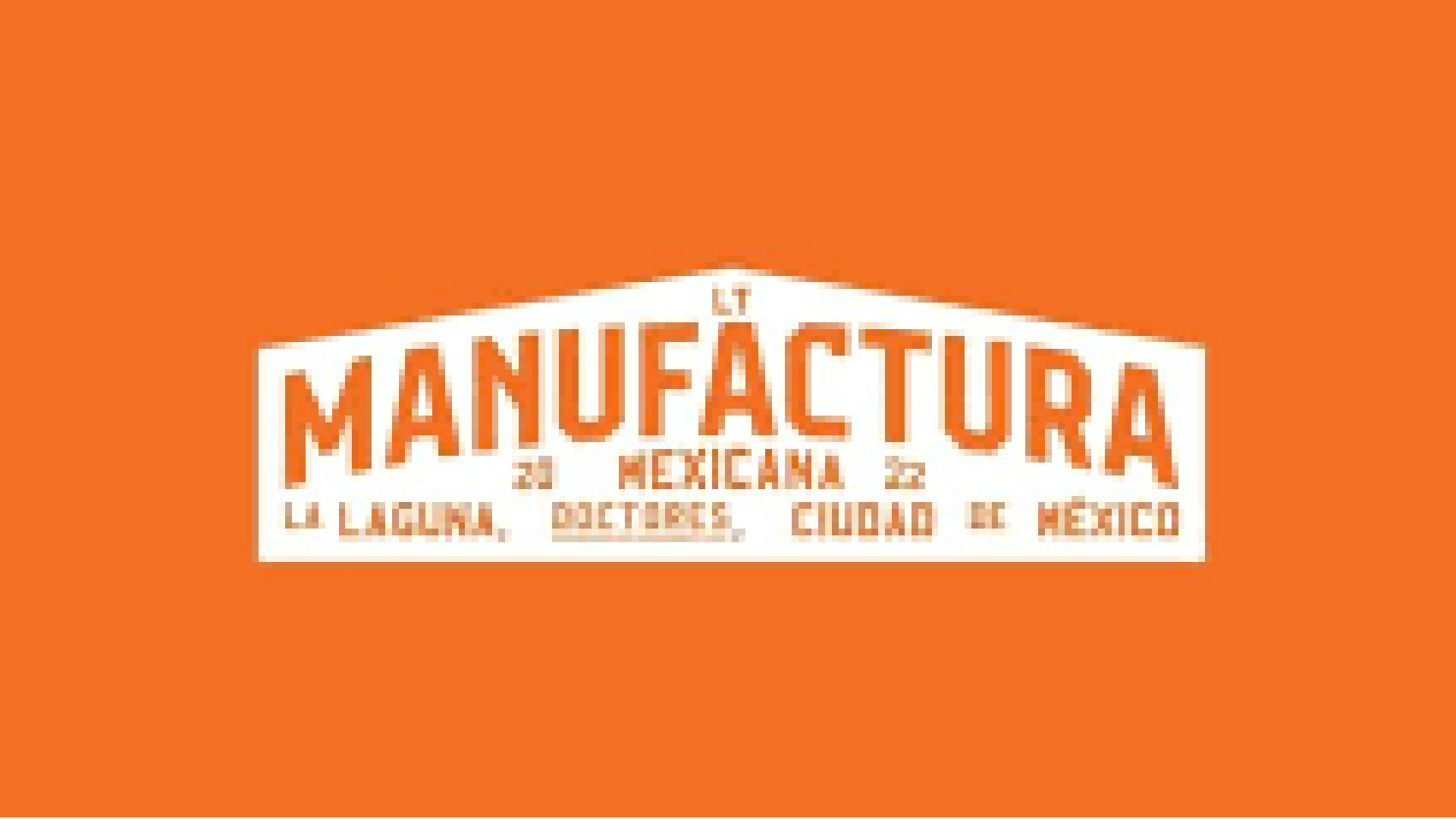
Sueños con Concreto explores the future of affordable housing in Mexico through low-impact construction methods.
The horizontal cover, based on a joist and vault system. The prefabricated concrete joists have been optimized with computational design methods developed at MIT, which minimize up to 50% of material use and associated environmental impact.
The 3D-printed ceramic vaults are placed between the joists as a lost formwork, and then the upper concrete slab is poured, manufactured by MANUFACTURA and ANFORA Studio. The use of tepetate, a local soil with a high clay content, allows the manufacture of compressed and sun-dried blocks that make up the walls of the pavilion.
Design and development: MIT
Presented at: Mextrópoli 2022
Credits & Publications
Architecture: Grupo Mota-Engil, MIT Leventhal Center of Advanced Urbanism
Community Partners: New Story, Échale
Collaborators: Digital Structures (MIT), Manufactura, Anfora Studio, Formas de Fibra de Vidrio, Future Urban Collectives
Photos: Marisa Morán, Arturo Arrieta, Dinorah Martínez Schulte, Walter Shintani, Rafi Segal
Publications: ArchDaily, ACADIA paper
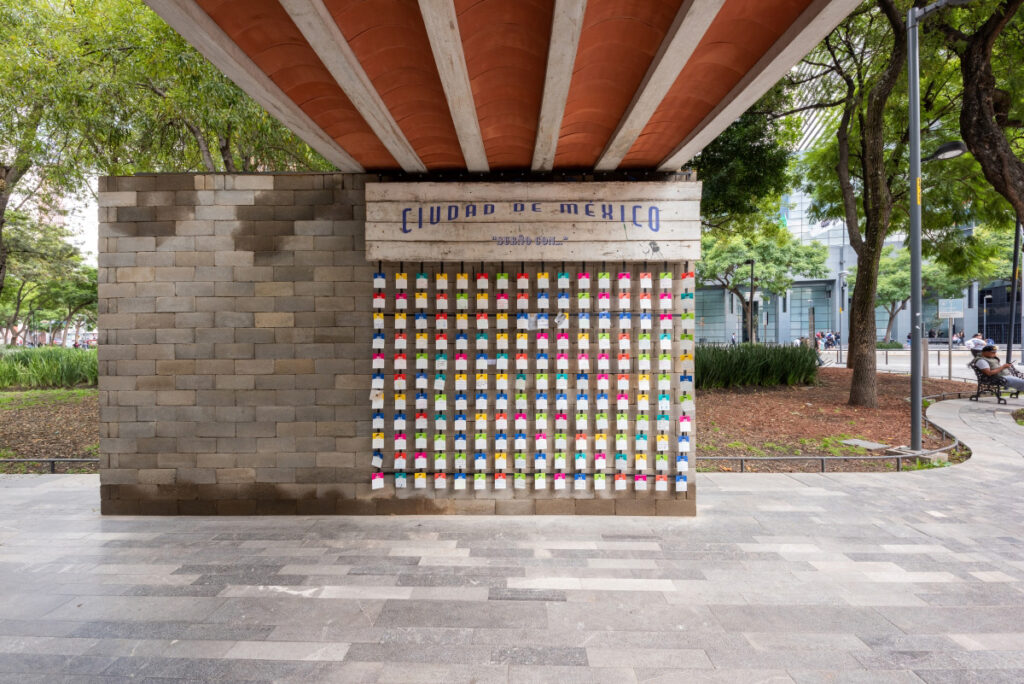
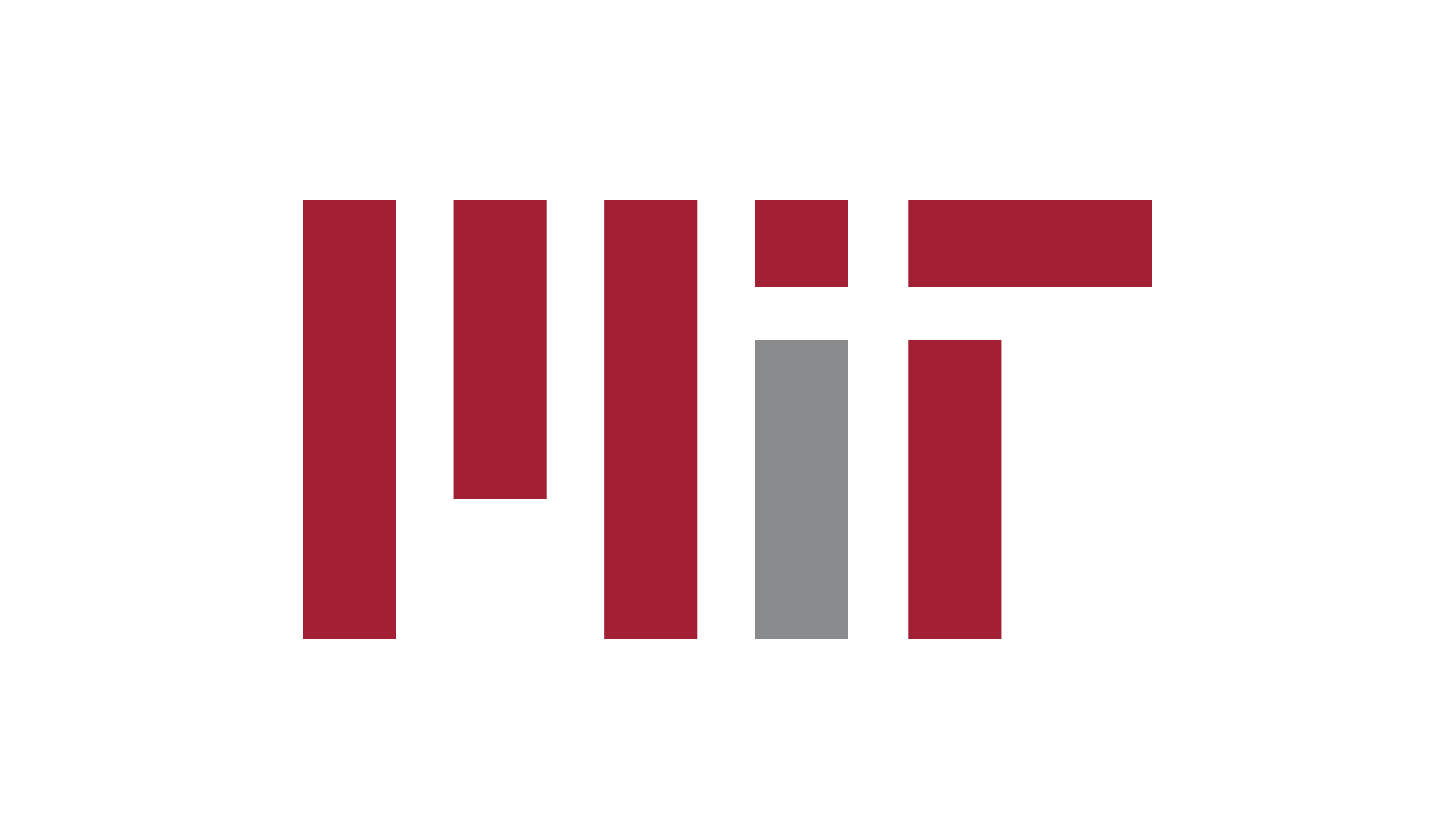
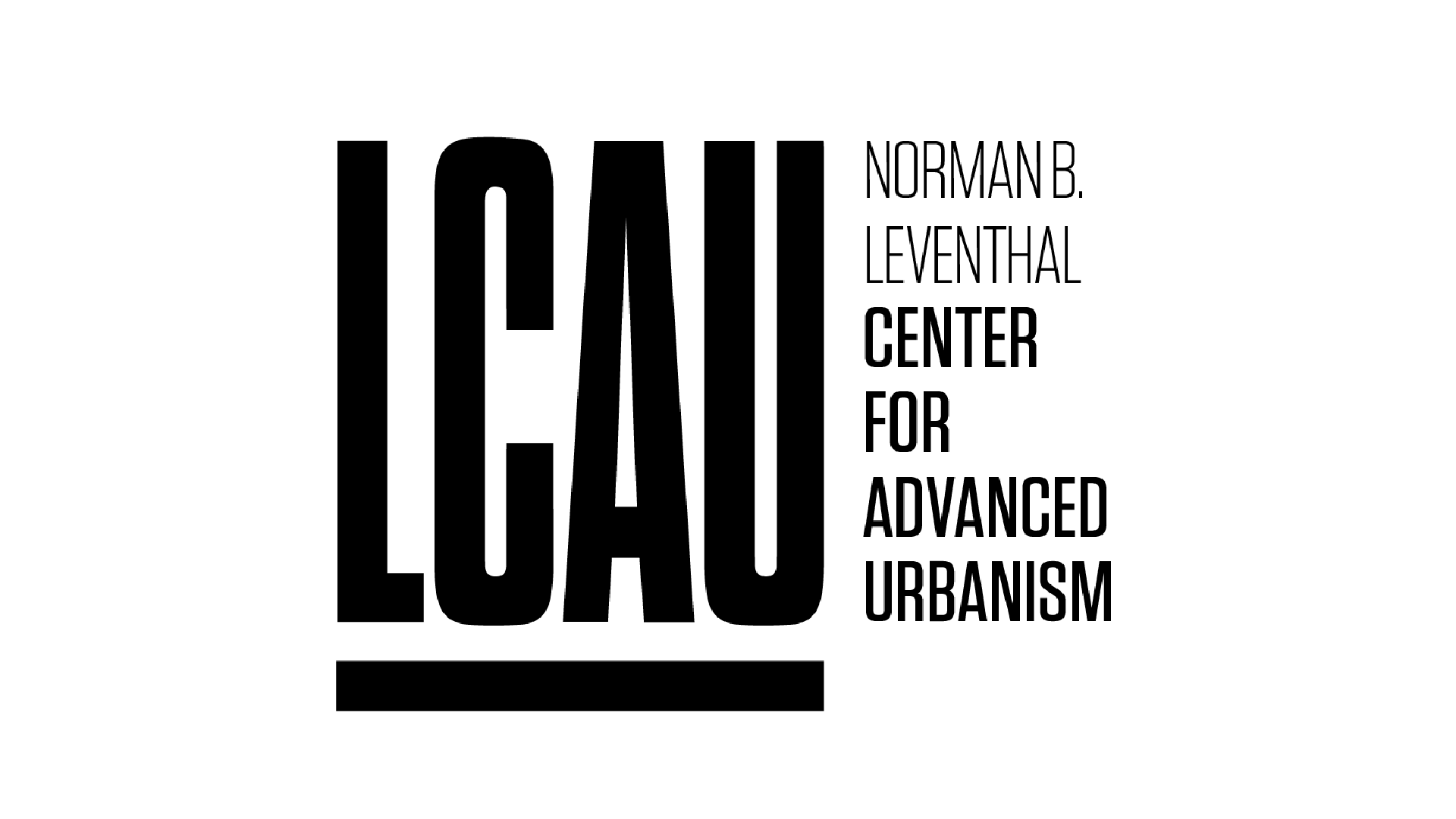
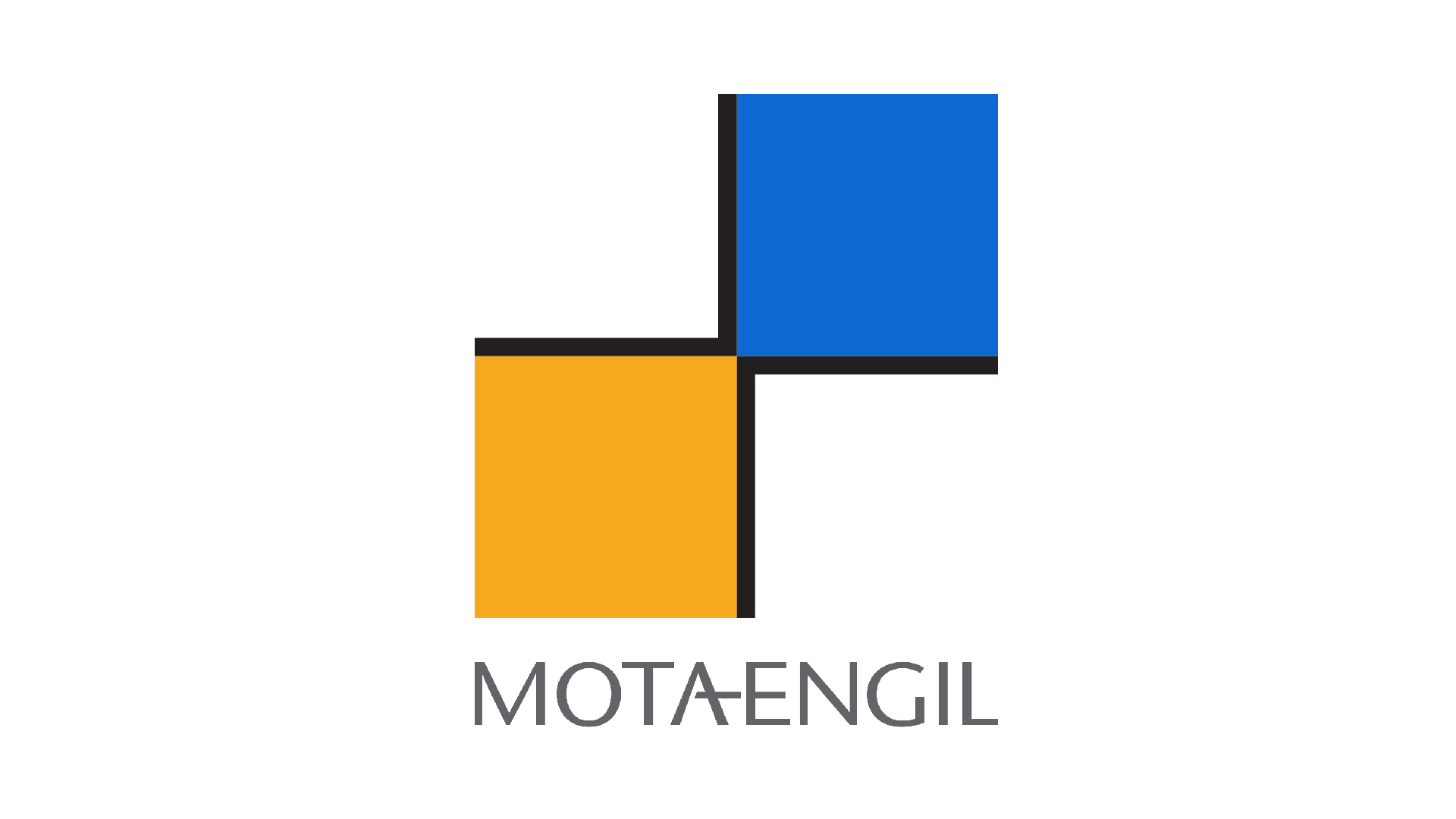
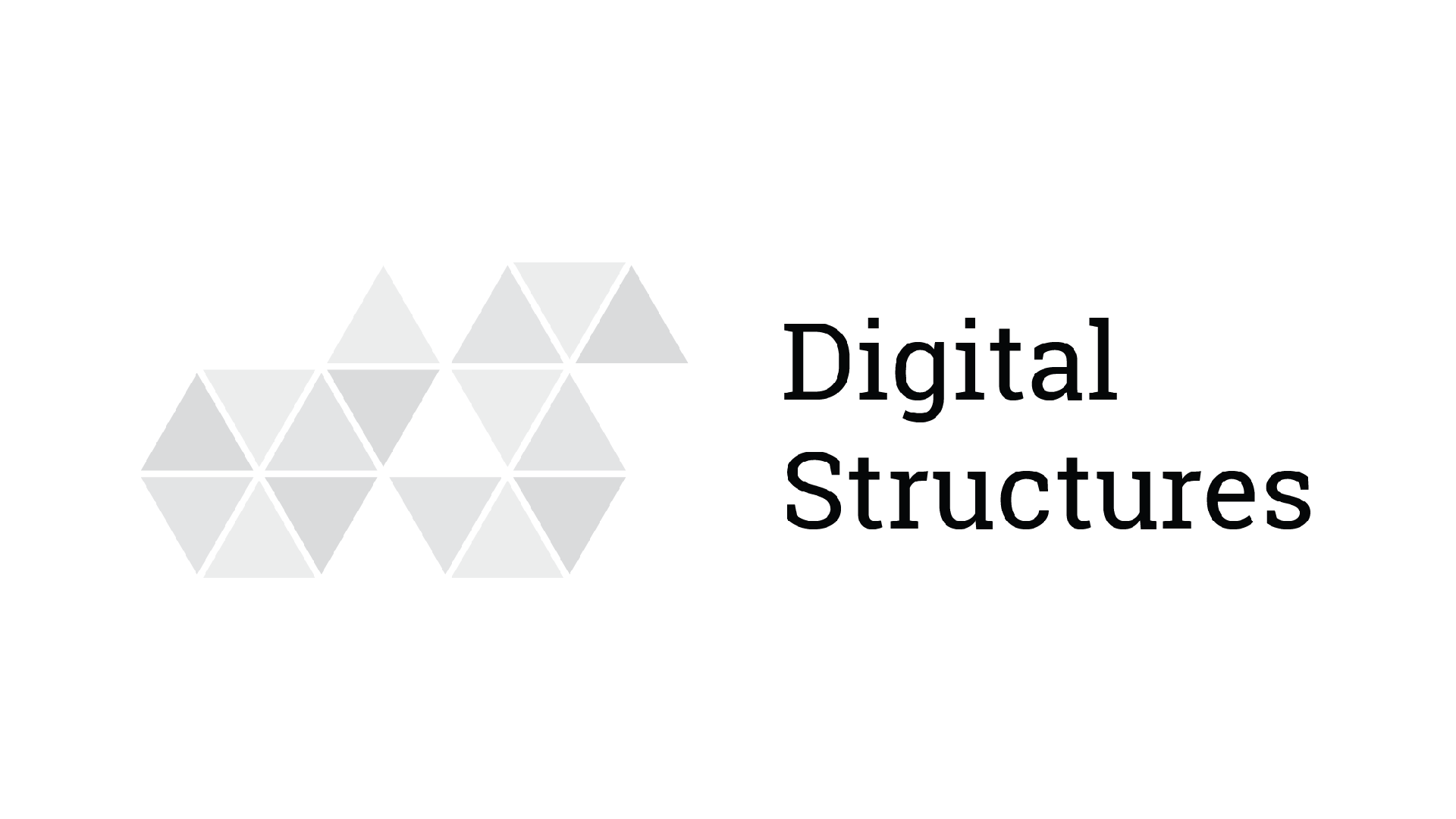
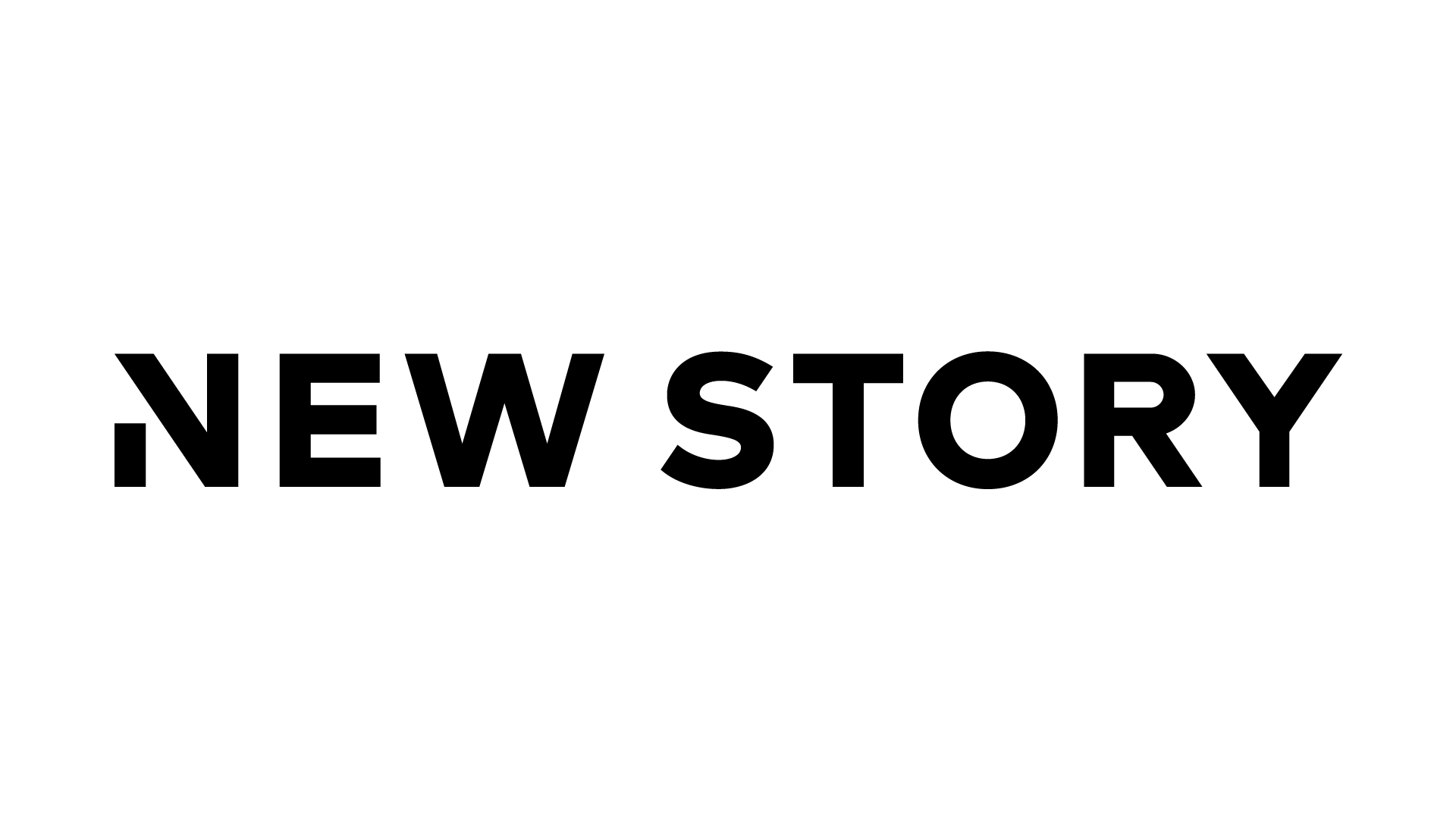
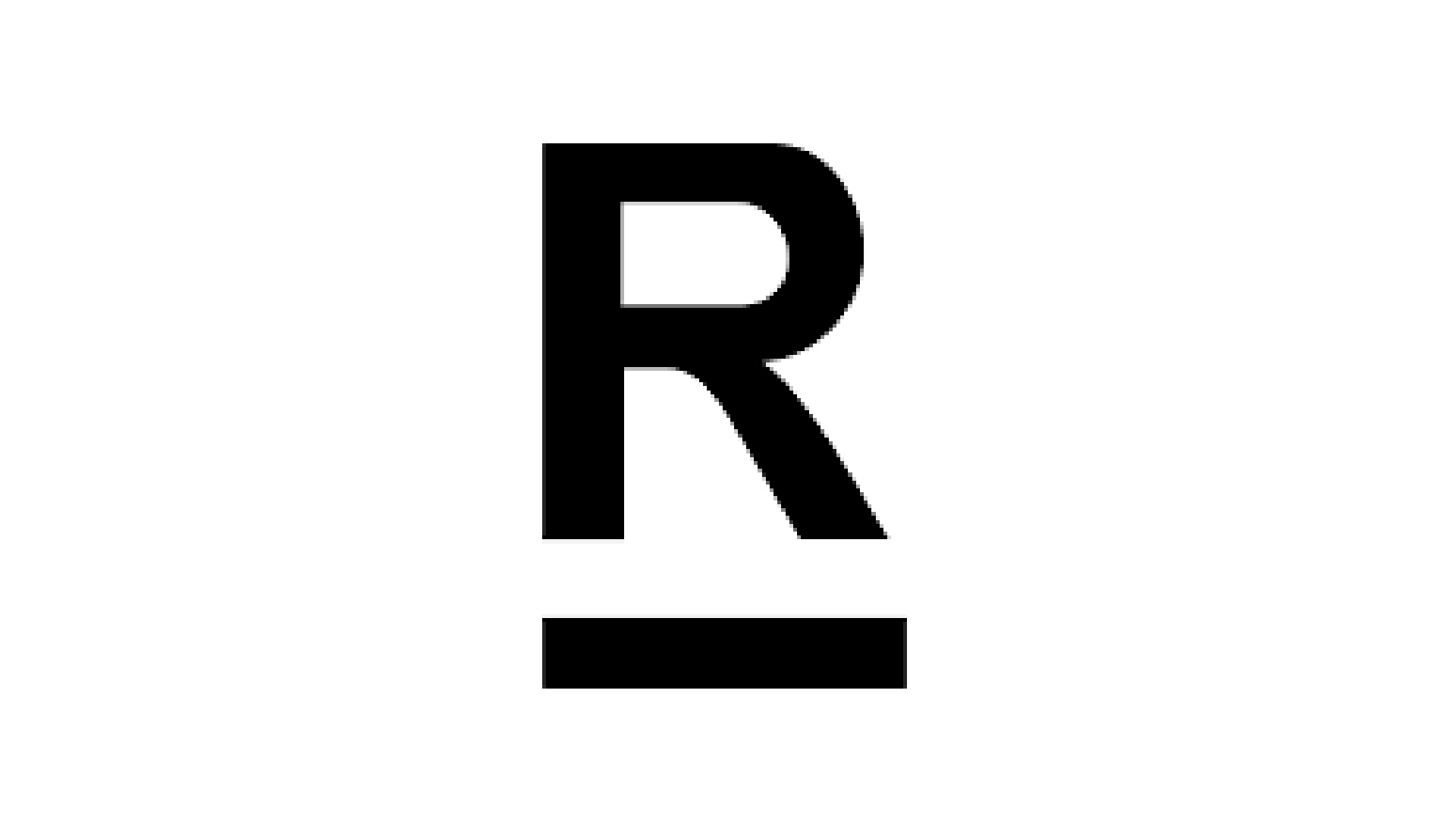

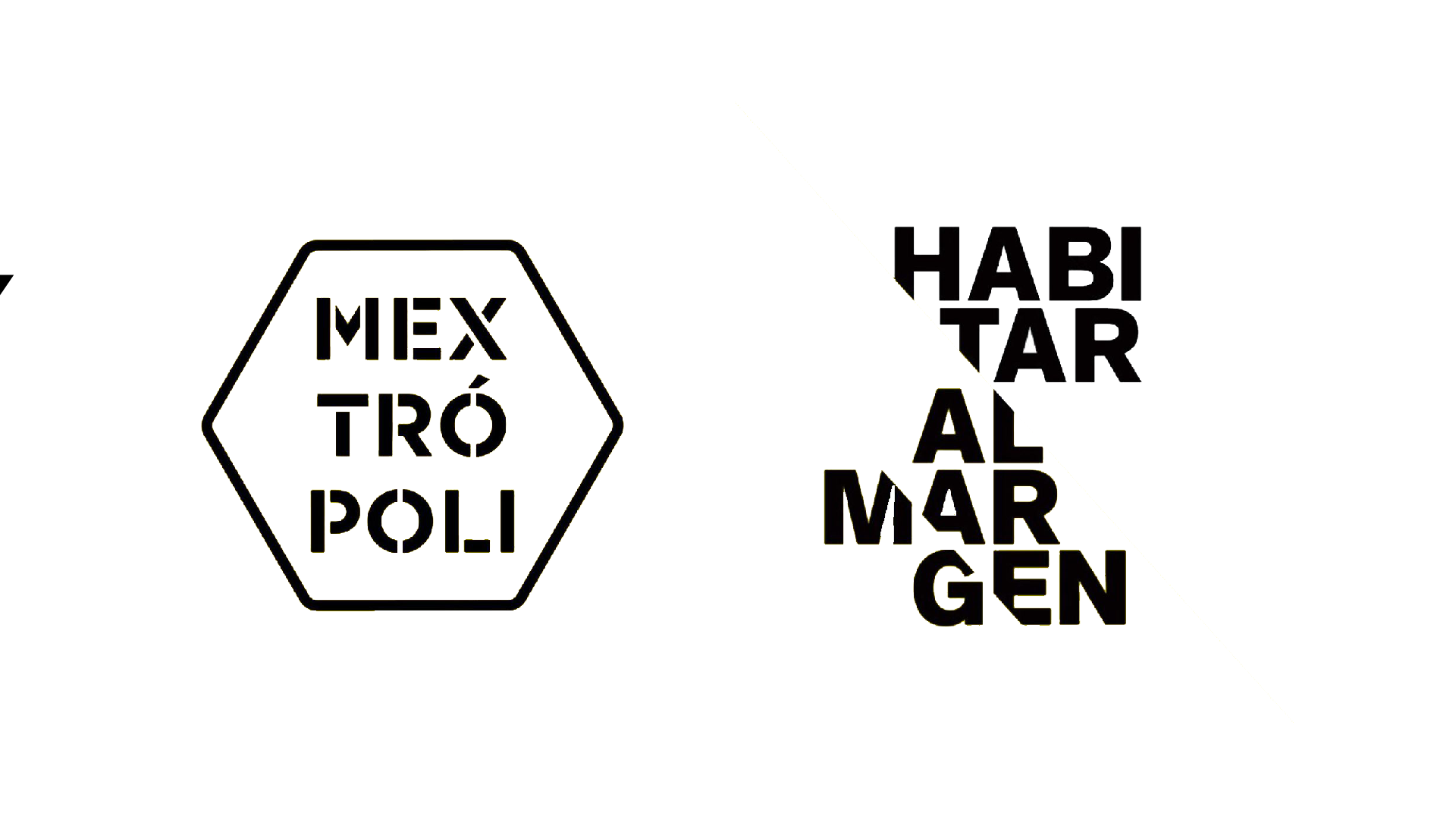
TALAVERA Project
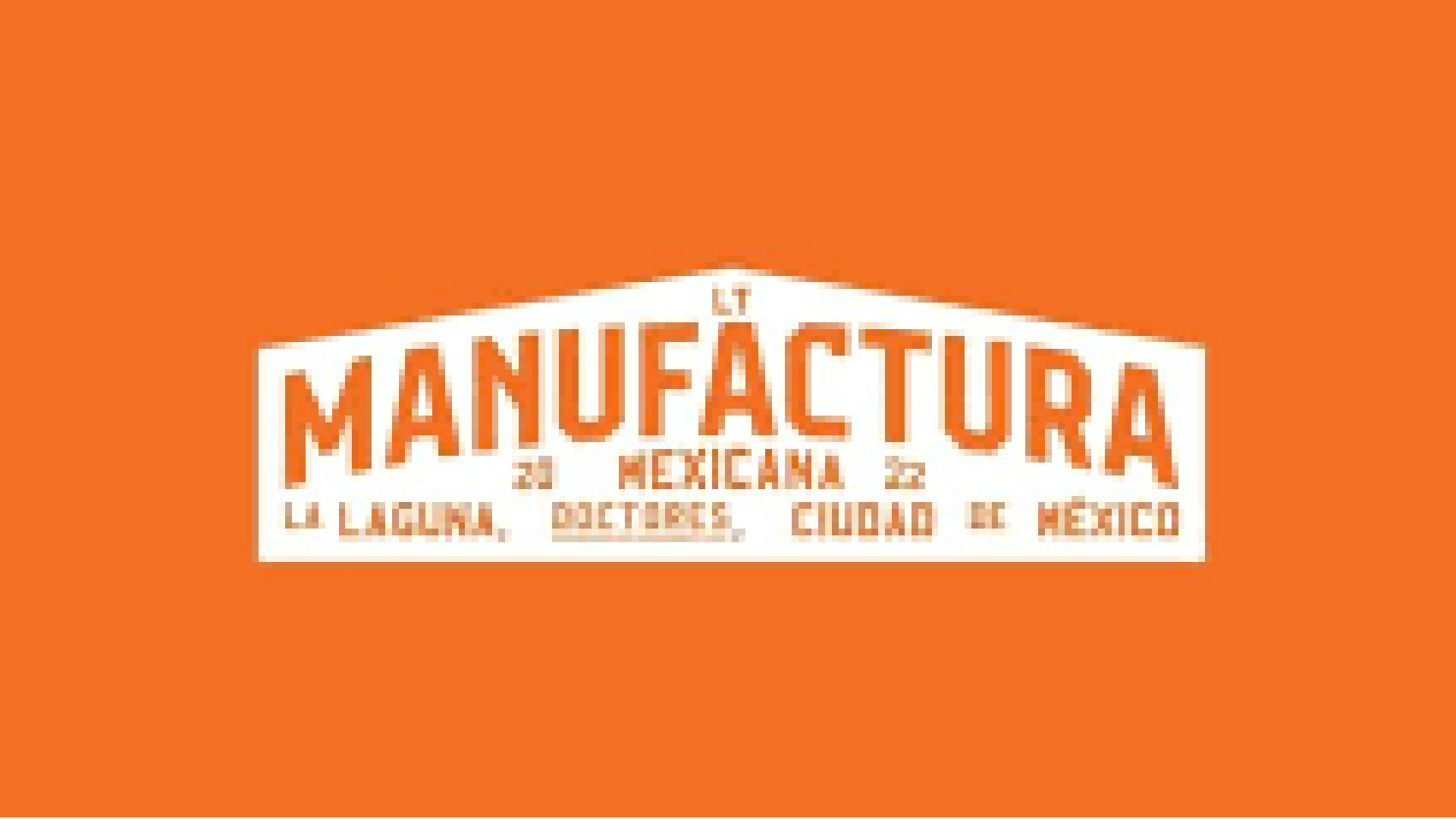
This project aims to create a dialogue between new technological methods and tradition. Talavera is a traditional Mexican and Spanish method listed as Intangible Cultural Heritage of Humanity by UNESCO.
This method requires specific clay sourcing and processing, making it hard to innovate.
Considering this the process for this specific project consisted of 3D printing the piece that would shape the mold based on the restrictions, to then pour, shape, and treat with the specific method required for Talavera.
Exhibited at: Patio Efímero Edición 4
Credits & Publications
Fabrication, Process development, design:
Manufactura + Uriarte Talavera
Manufactura: Dinorah Schulte (invited artist, co-founder), Edurne Morales (co-founder, computational design, design)
Collaborators: Jared Zarate
Uriarte Talavera: Mariana Muñoz (Directora General), Arturo Rojas (Dirección de Producción), Katia Ramirez (Dirección de Producción)
Artisans: Cesar Oropeza, Arturo Rojas, Miguel Vazquez, Hector Dominguez (Barros), Artemio Romero, Ángel López (Hornos), Claudia Pérez, Jessica González (Calidad), Beatriz Chavez, Massiel Xique, Claudia Rocha (Jahuete), Alberto Garcia, Carmen Cardona, Patricia de la Rosa, Santa Micaela, Norma Juarez (Vidriado), Enrique Vazquez, Sergio Ayona, Guadalupe Ruelas,
Neli Pérez (Pintura), Ericka Alarcón (Estarcido).
Investigación, producción y donación de material: Uriarte Talavera
Photos: Dinorah Martínez Schulte, Arturo Arrieta
Publications: Rhino3dzine, Parametric Architecture, DesignBoom
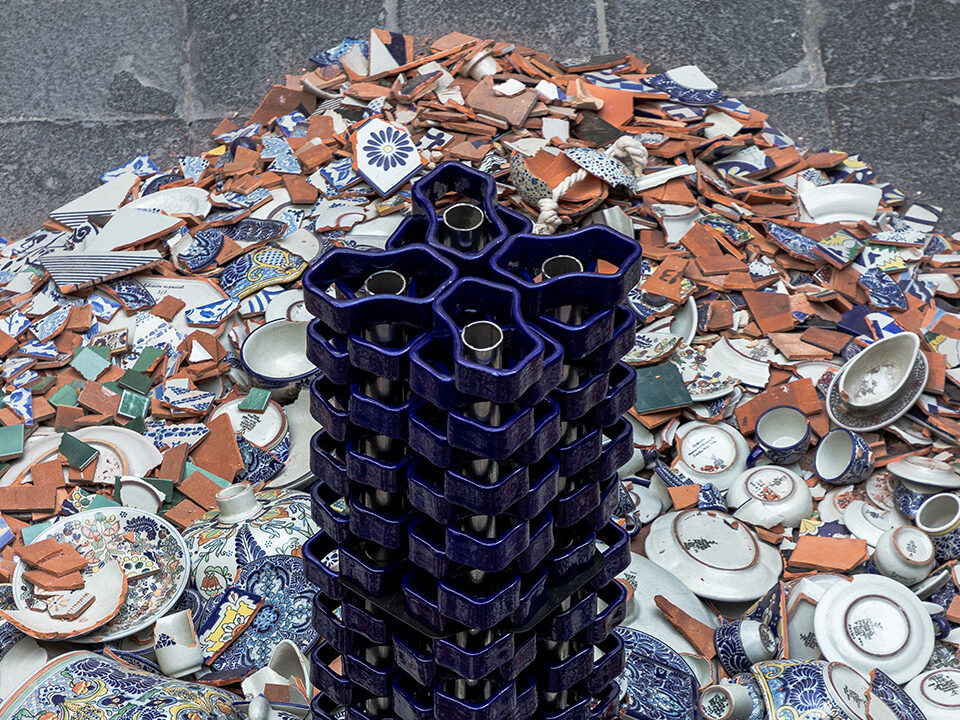
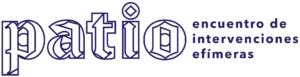
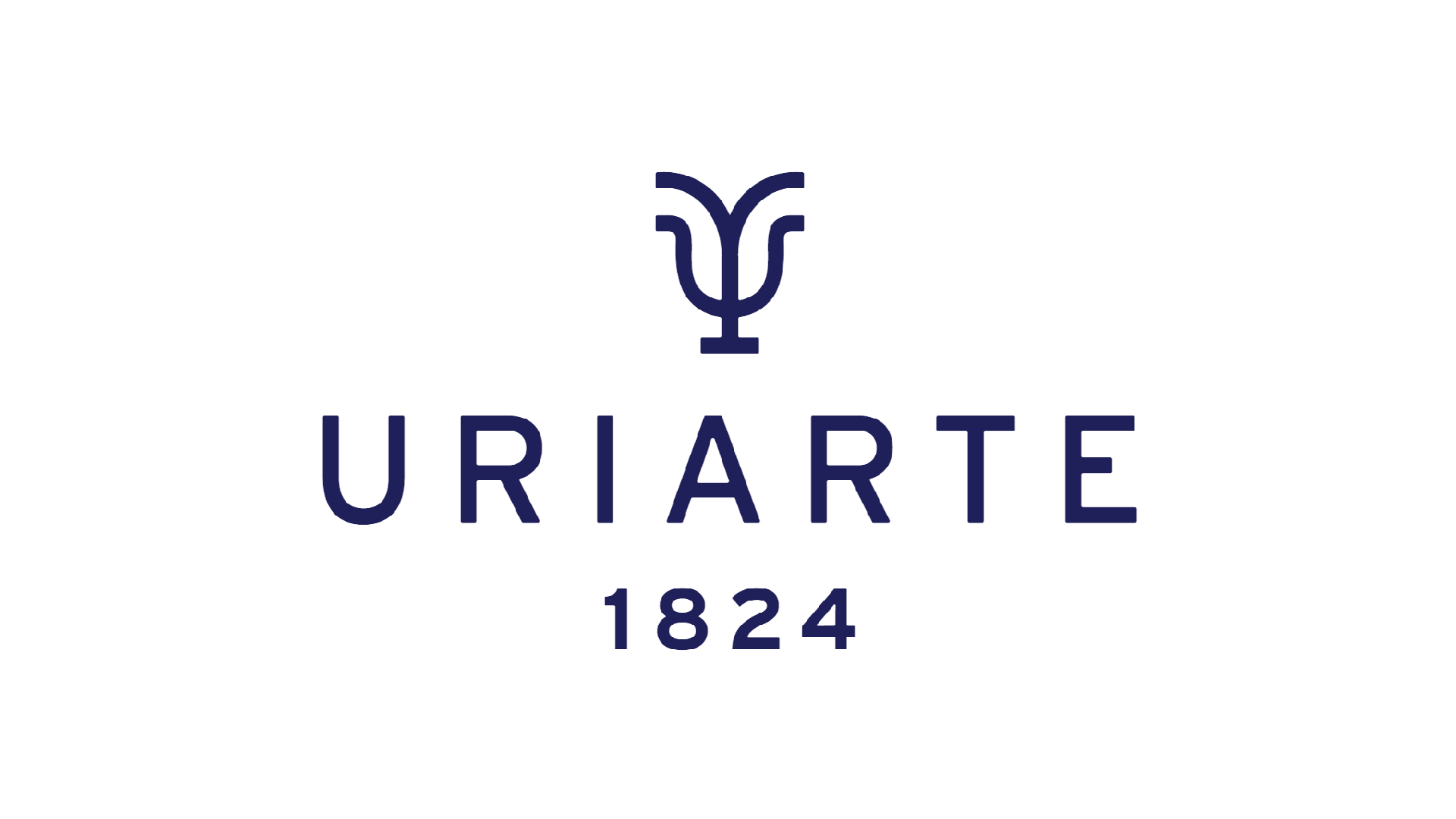
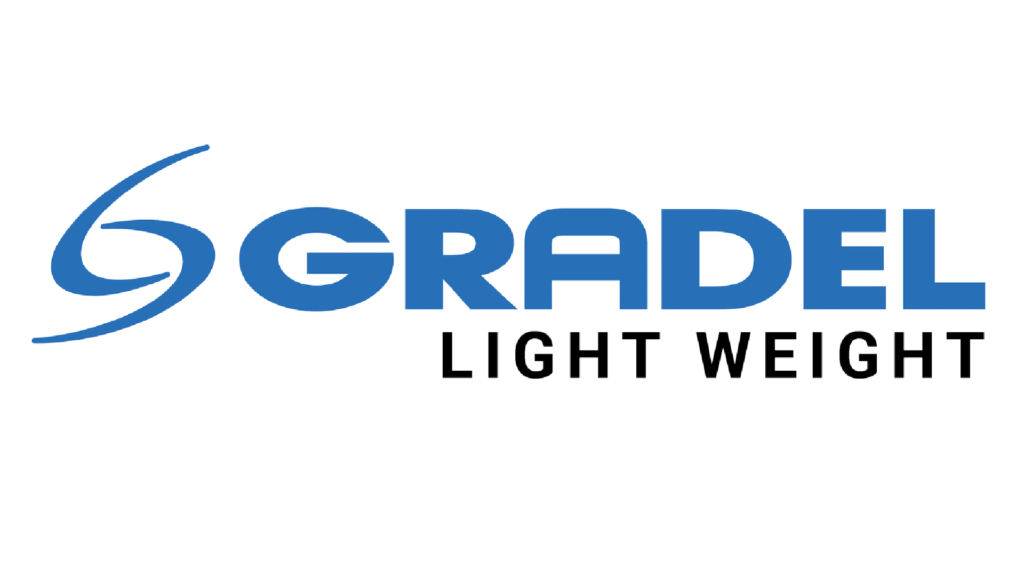
GRADEL
GRAM Space application’s development
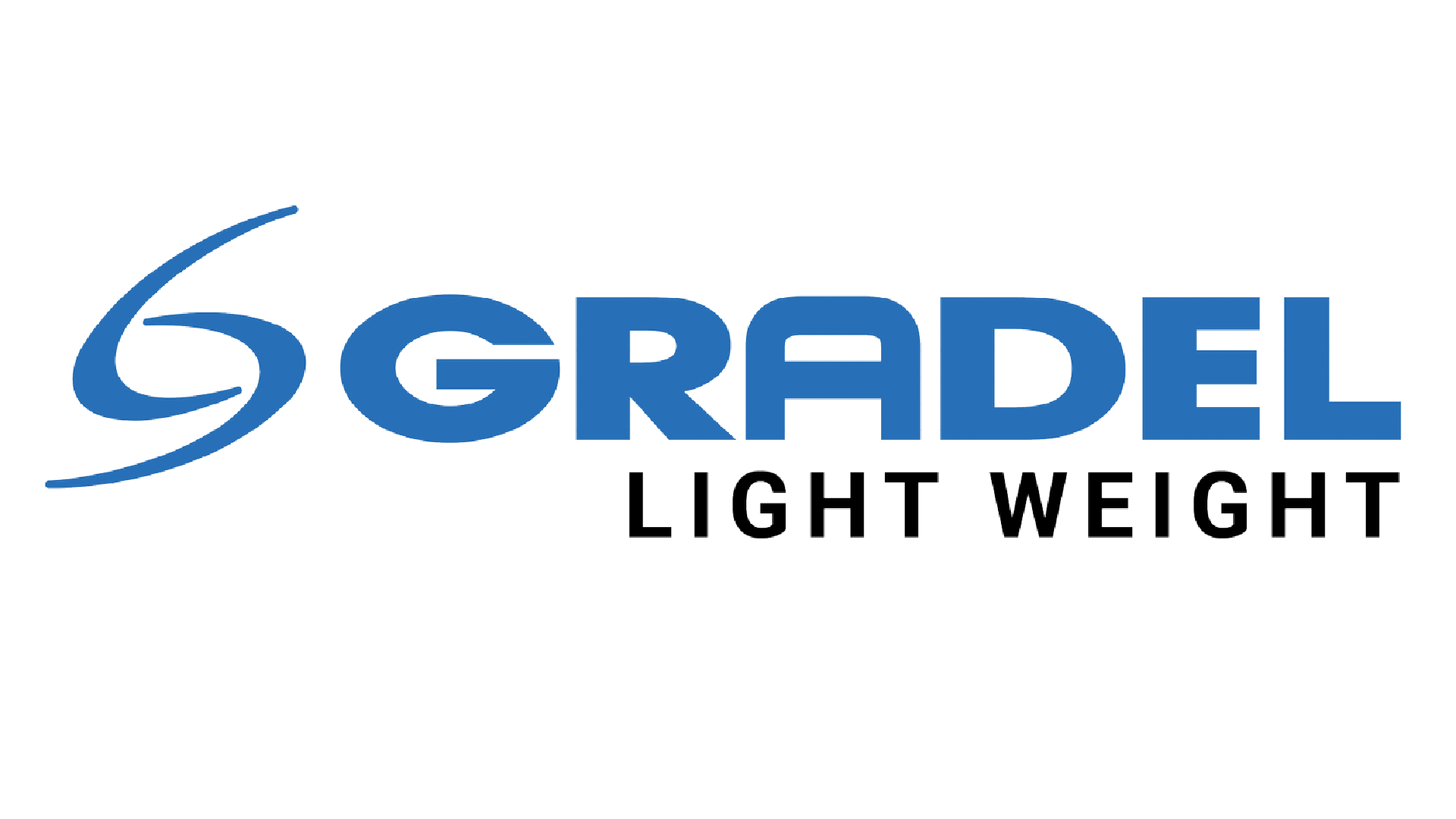
This joint project with the European Space Agency, LIST (Luxembourg Institute of Science and Technology), and multiple industry partners aims to develop the GRAM (Gradel Additive Manufacturing) technology for its use in space.
This multi-layered research combines structural and mechanical design development, carbon composite for this specific application and in-house computational methods for its robotic application.
Ongoing development, currently TR5
Presented at ESA in 2024
Credits & Publications
Manufacturing, process development, design: Gradel LW + Luxembourg Institute of Science and Technology
Team: Claude Mack (CEO), David Macieira (project leader), Pierre Schumann, Jair Cordeiro, Rodrigo Hernandez, David Pizzagalli (production), Nicolas Jeannot, Colin Barad, Steve Krecke (engineering), Mira Al Akkawi, Ahmed Al Moumen, Laetitia Blaise (material engineering), Edurne Morales, Mengxi He, Bahar Al Bahar (robotics)
Collaborators: ESA, Airbus, OHB, Thales,
Photos: Gradel LW (Rodrigo Hernandez, Edurne Morales)

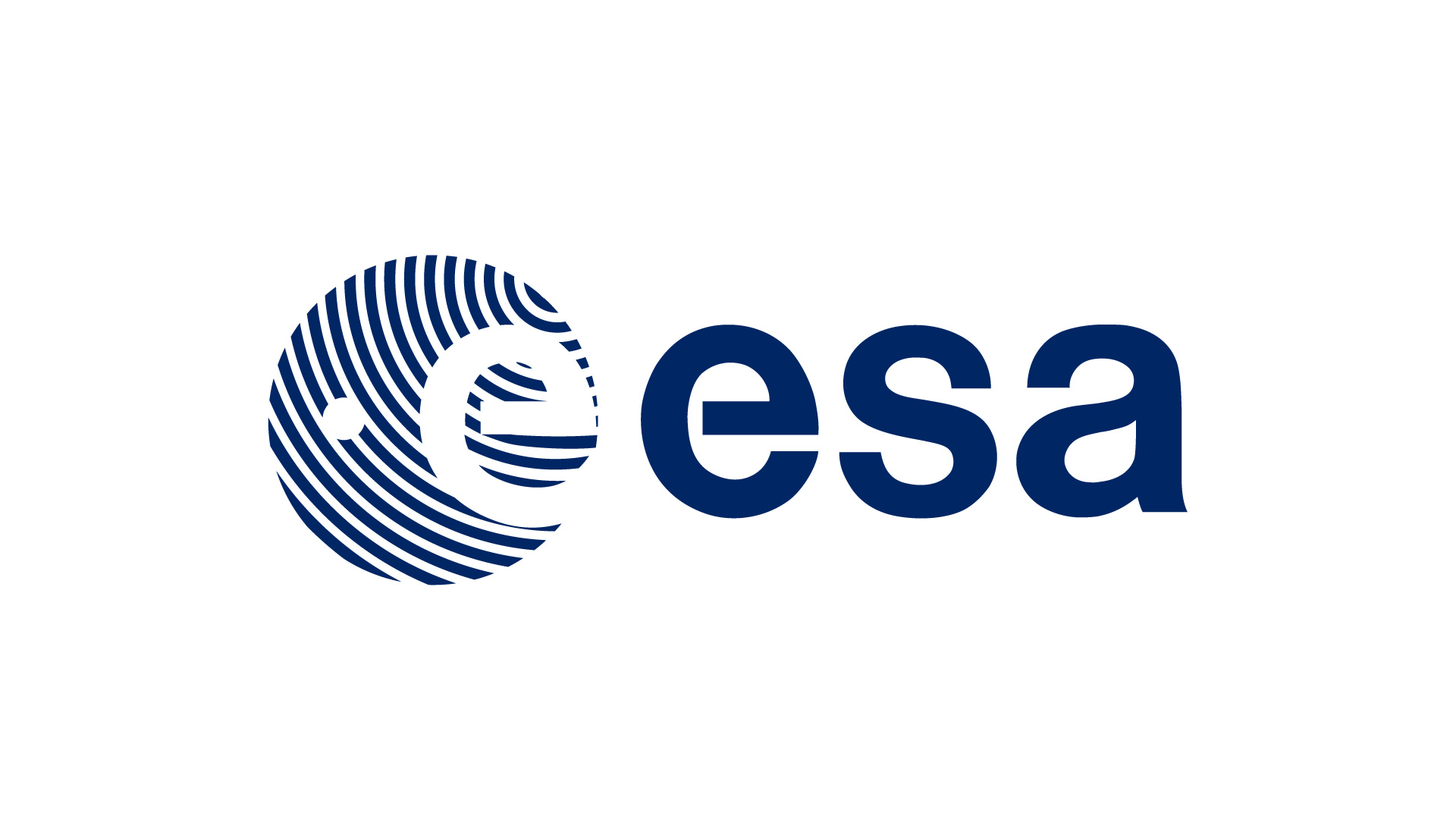
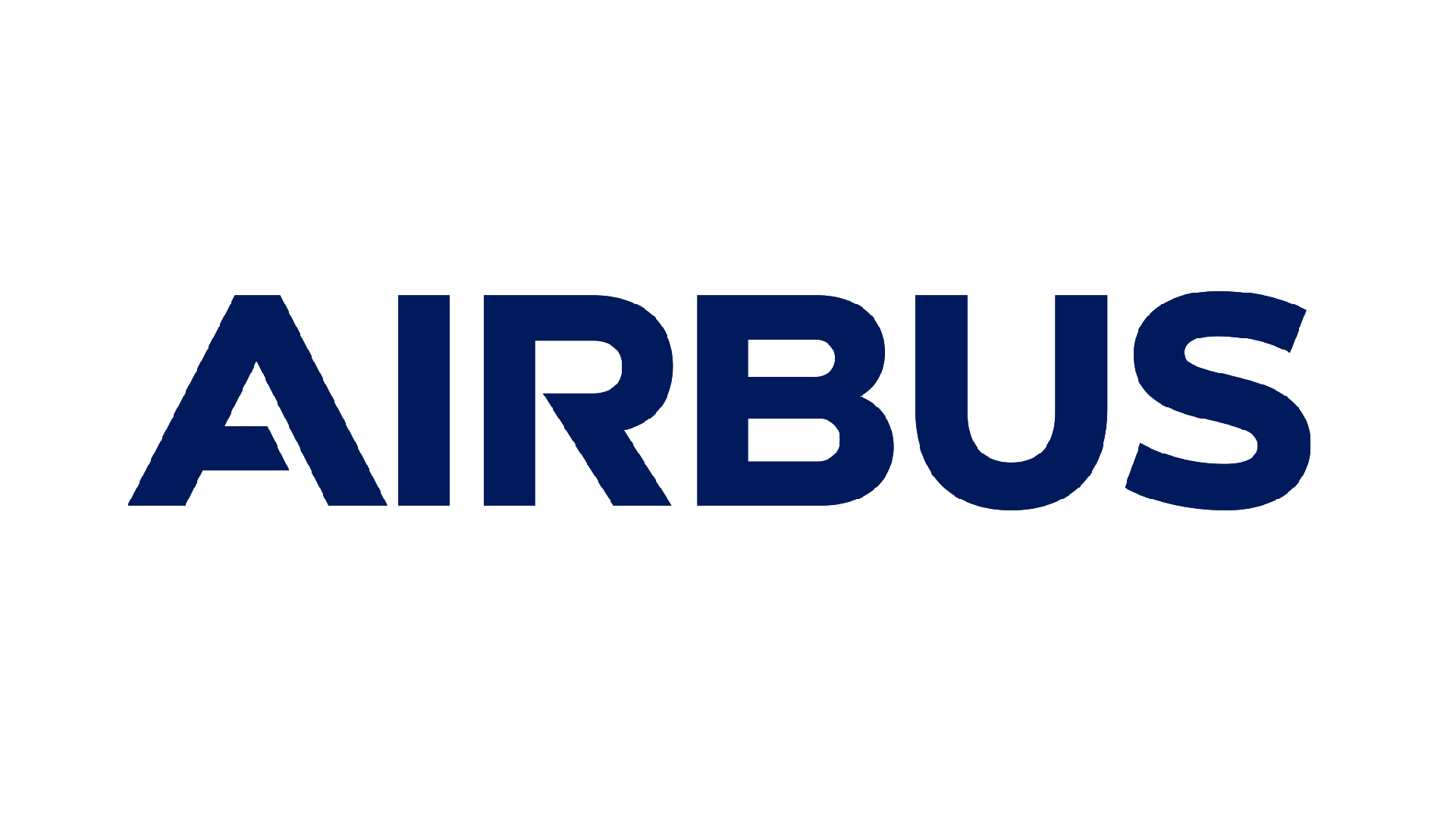
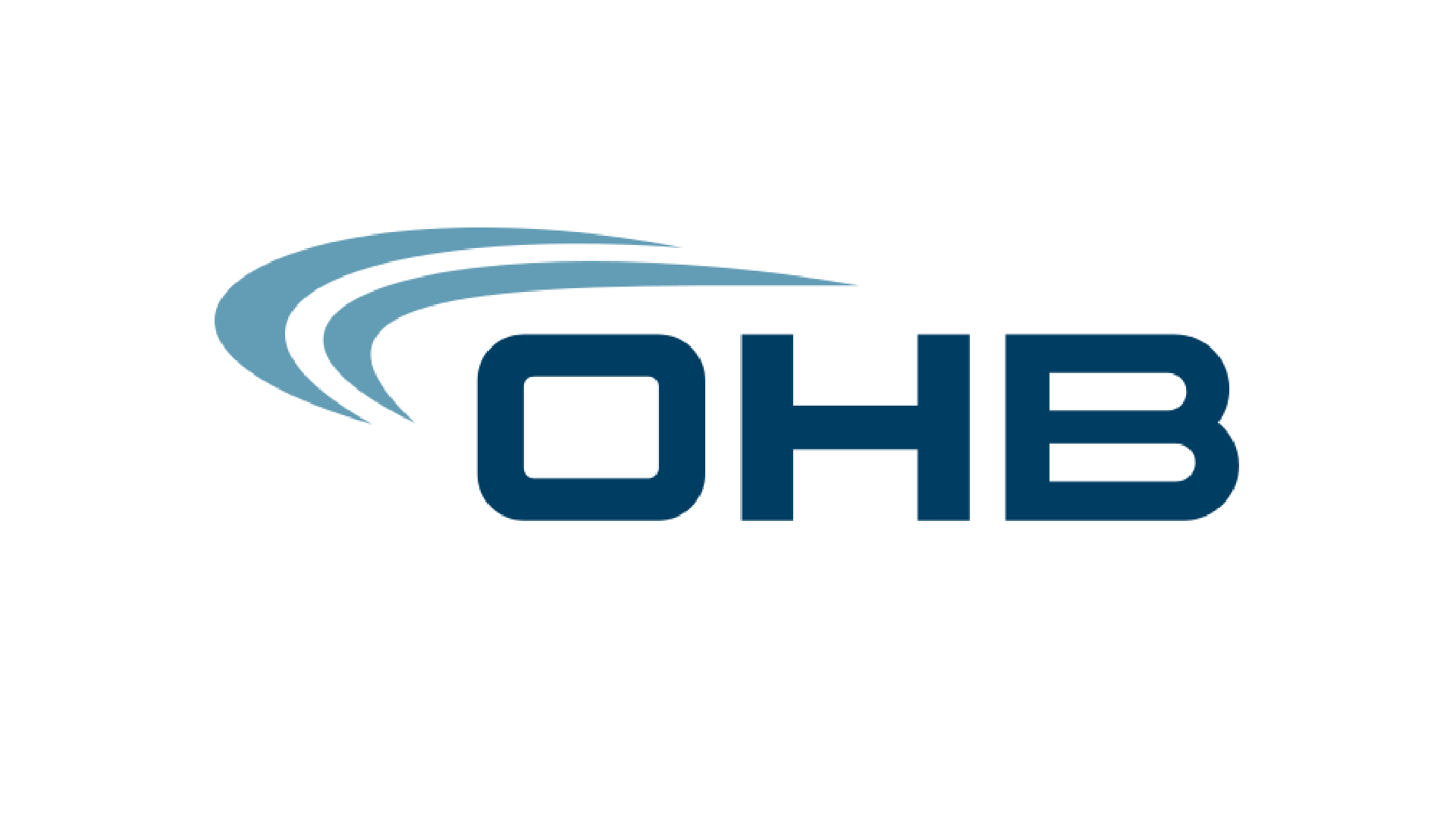
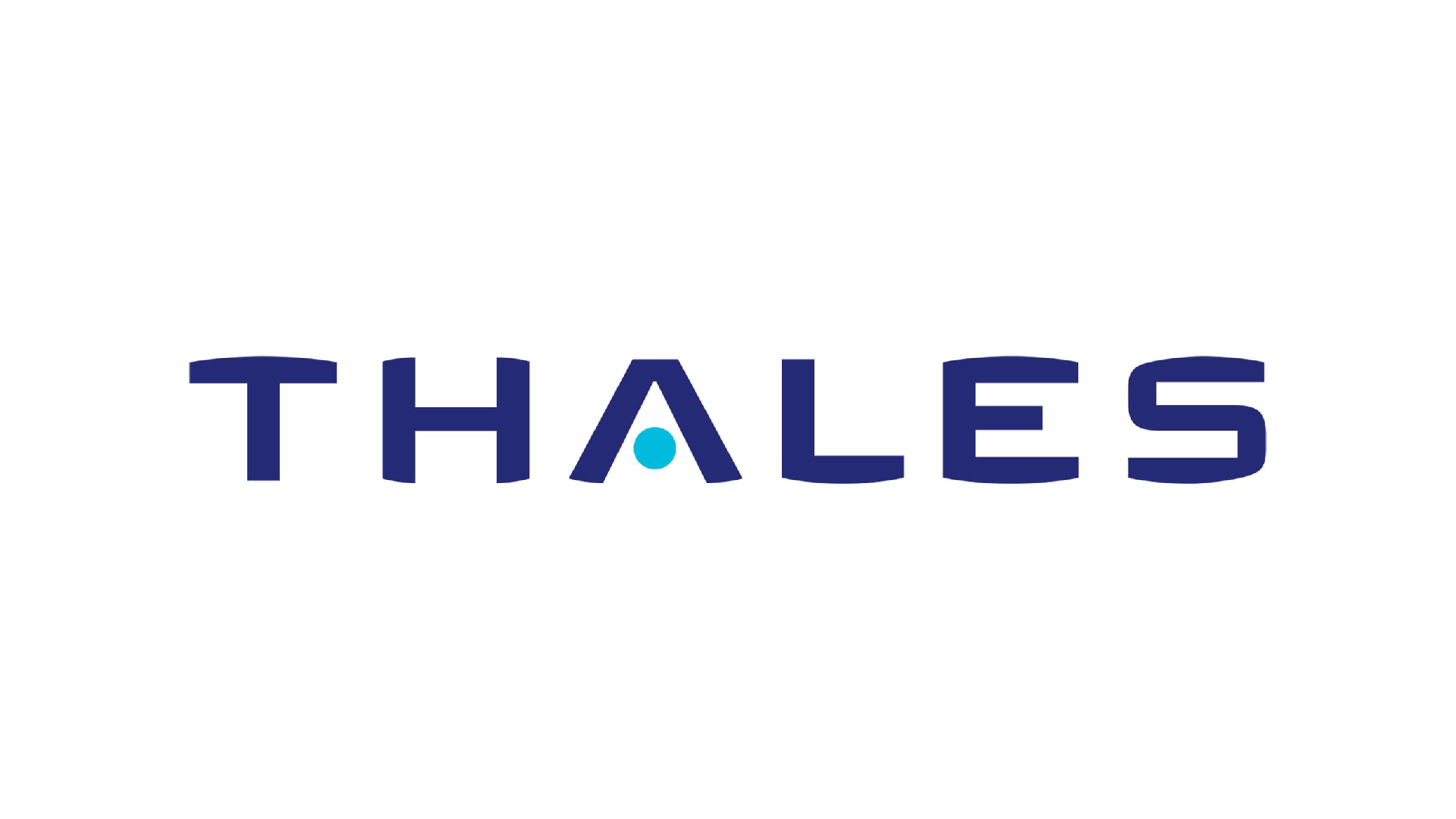
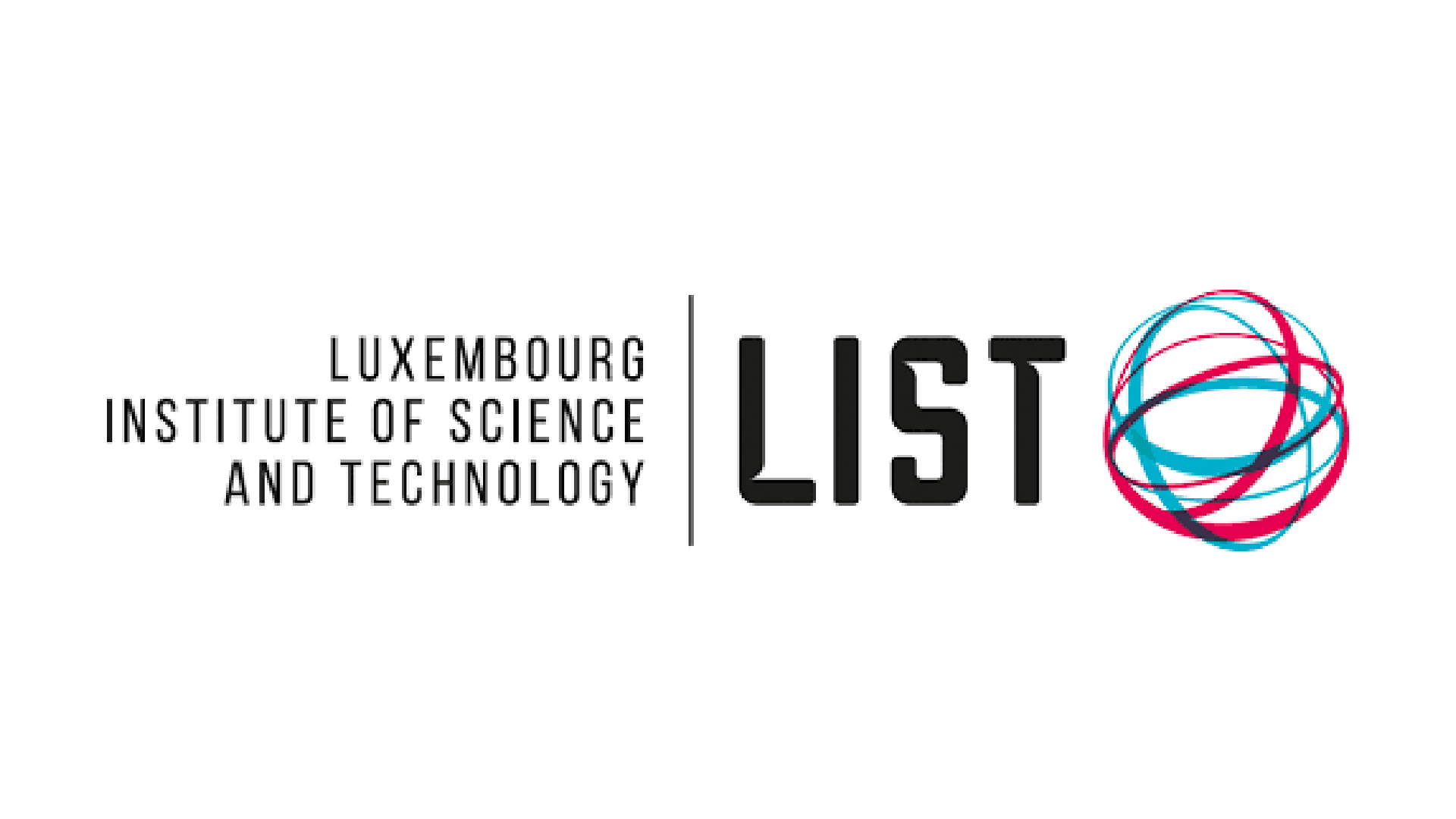
BMW M Visionary Material Seat
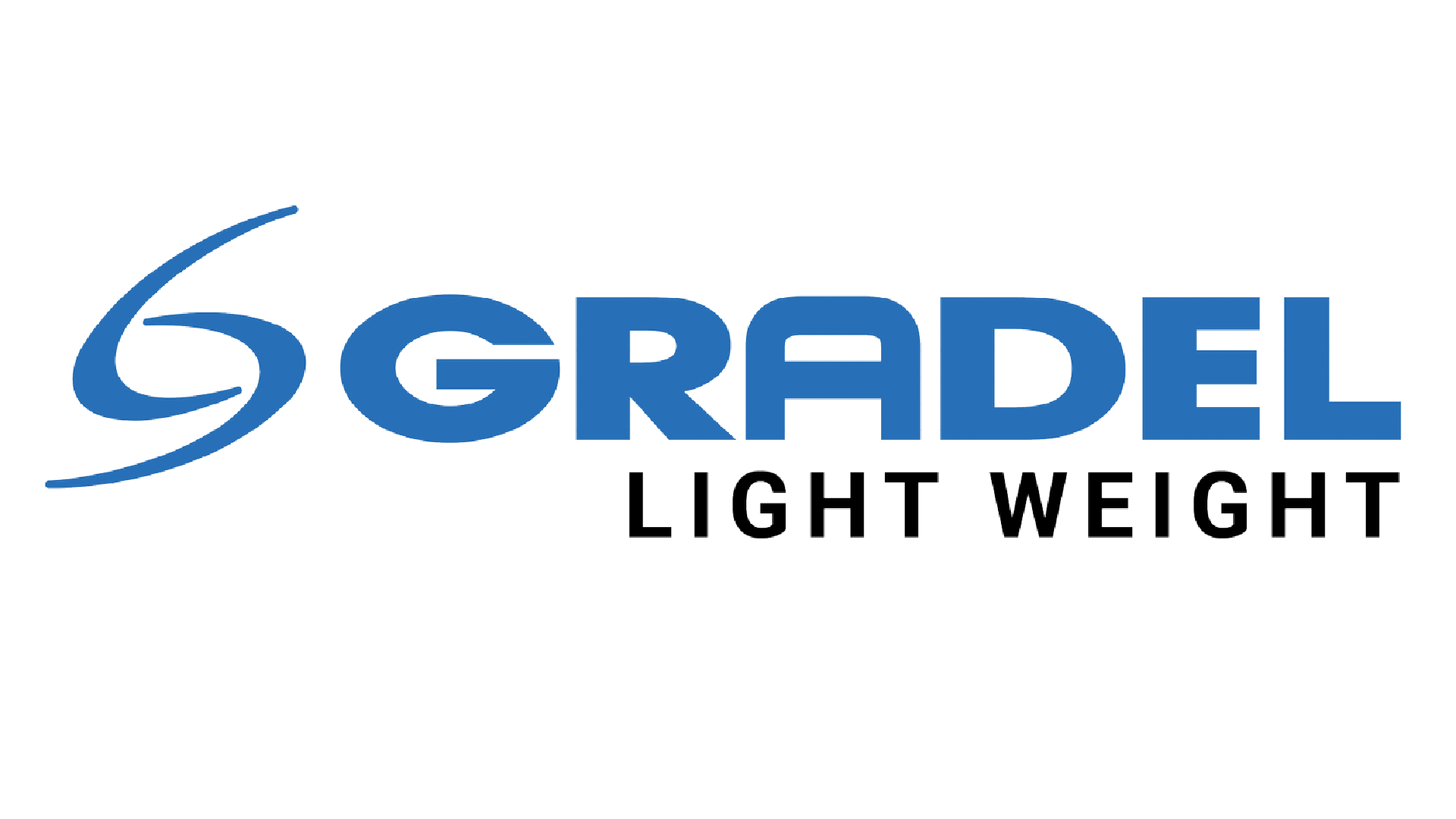
The creation of the BMW M Visionary Materials Seat is based on combining sustainability with cost-efficiency. To meet this requirement, BMW M obtained valuable support from leading companies in this field. BMW Designworks created the design, color and material concept, while Automotive Management Consulting GmbH, Gradel Light Weight Sàrl, Lasso Ingenieurgesellschaft mbH and Bcomp Ltd – a Top 100 Global Cleantech Company – contributed their collective know-how.
Some of the elements that characterize this seat are: a lightweight construction, design for circularity, and BMW’s characteristic high quality and practicality.
Development and production: 2023-2024
Credits & Publications
Manufacturing: GRADEL LW
Client: BMW
Gradel Team: Claude Mack (CEO), David Macieira (project leader), Pierre Schumann, Jair Cordeiro, Rodrigo Hernandez, David Pizzagalli (production), Nicolas Jeannot, Colin Barad, Steve Krecke (engineering), Mira Al Akkawi, Ahmed Al Moumen, Laetitia Blaise (material engineering), Edurne Morales, Mengxi He, Bahar Al Bahar (robotics)
Design and development: BMW, Automotive Management Consulting GmbH, Gradel Light Weight Sàrl, Lasso Ingenieurgesellschaft mbH and Bcomp Ltd
Diagrams and photos: BMW, Gradel LW (Edurne Morales)
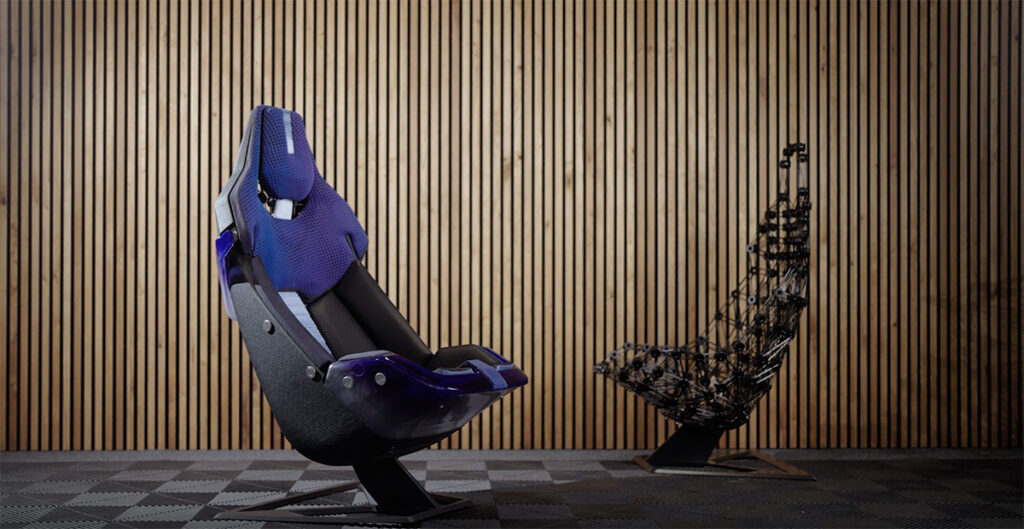
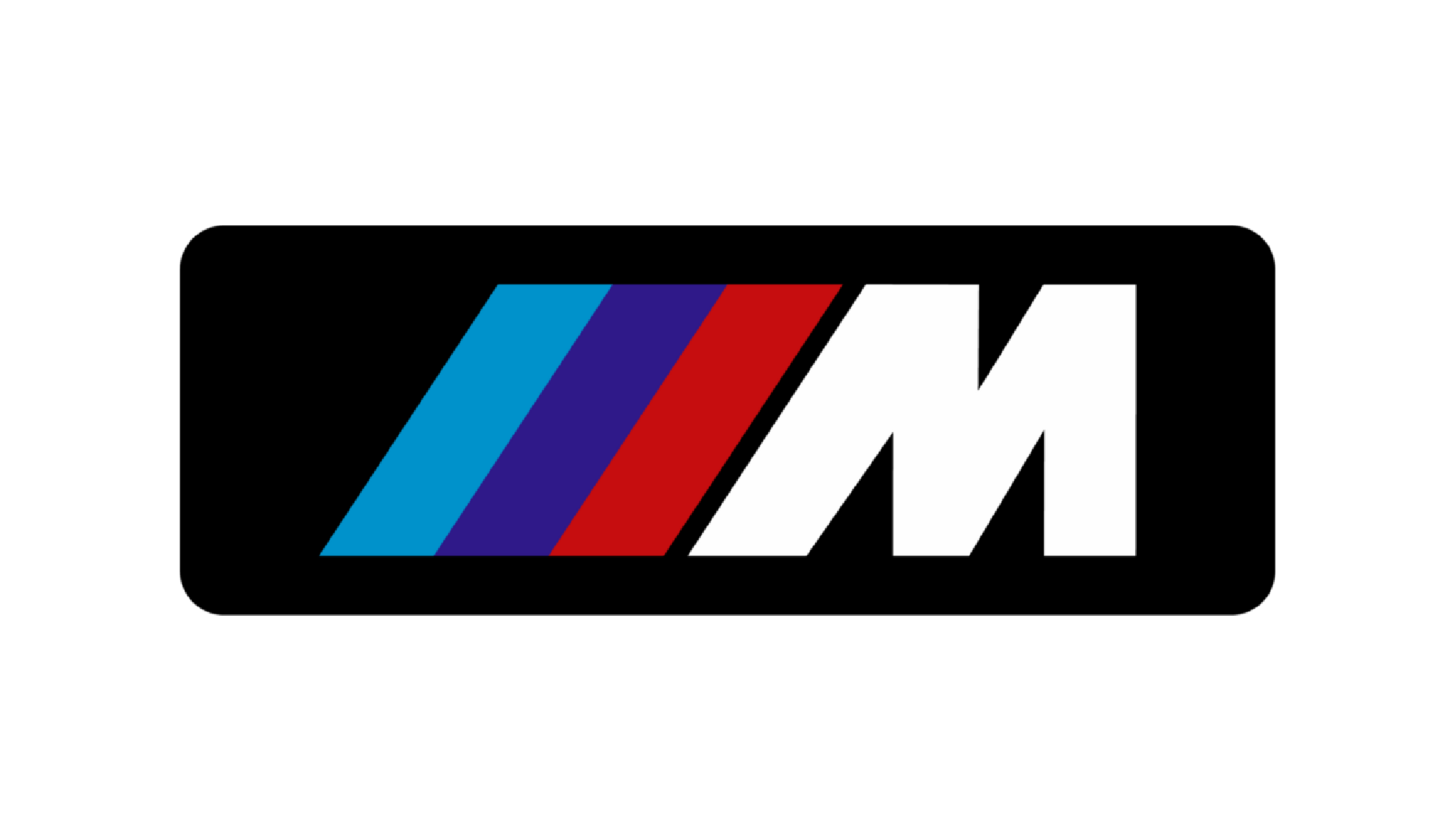
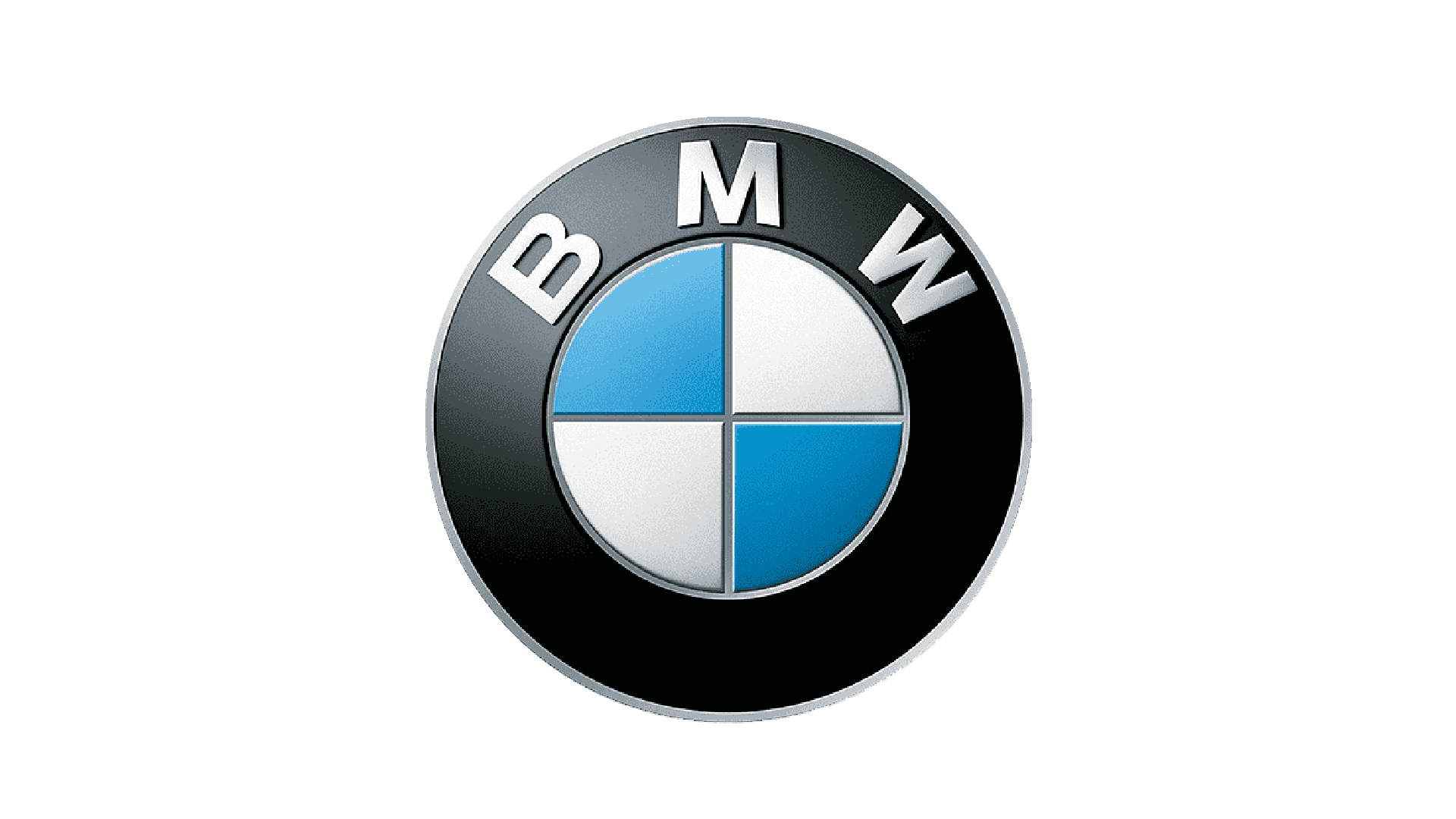
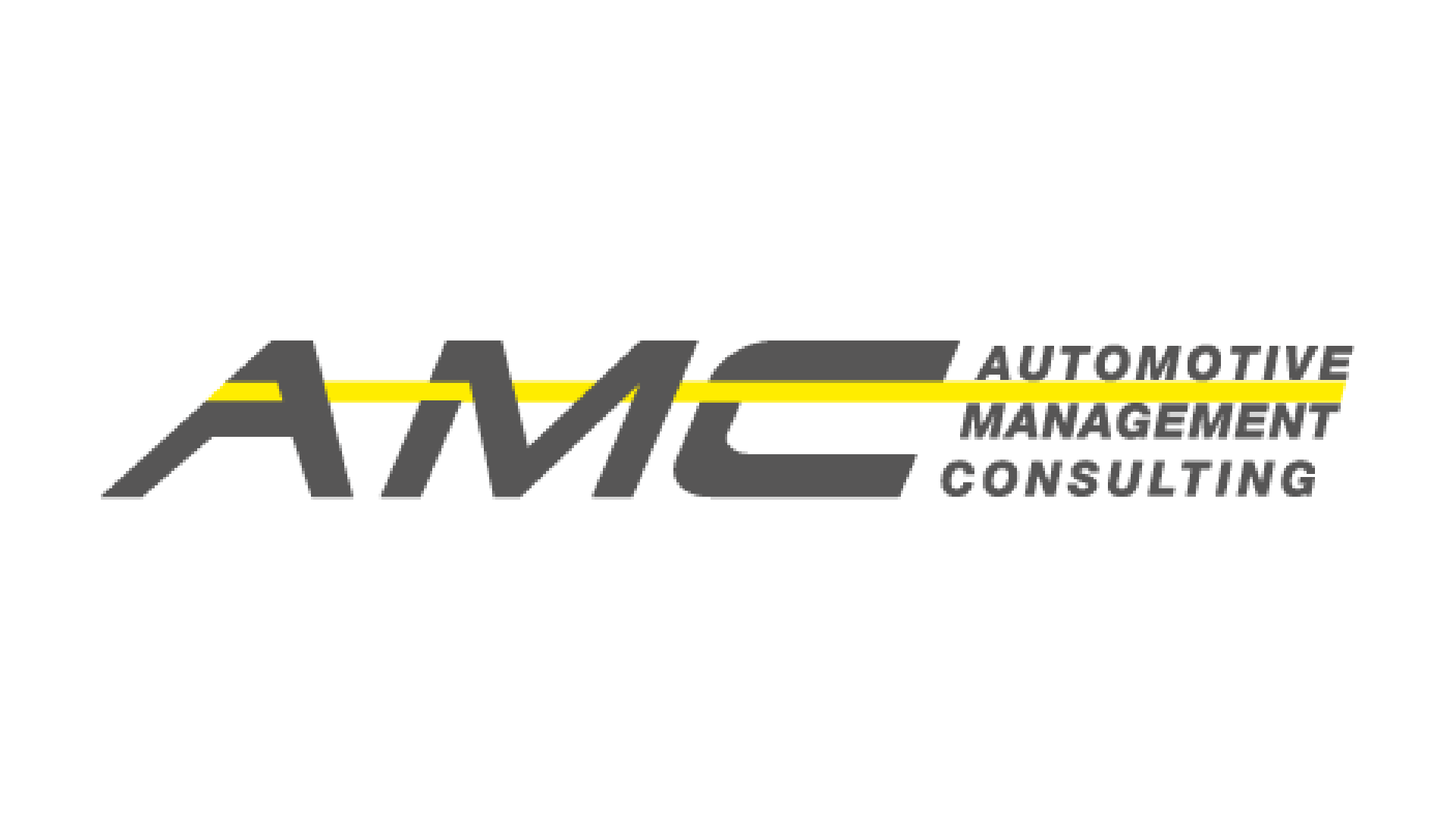
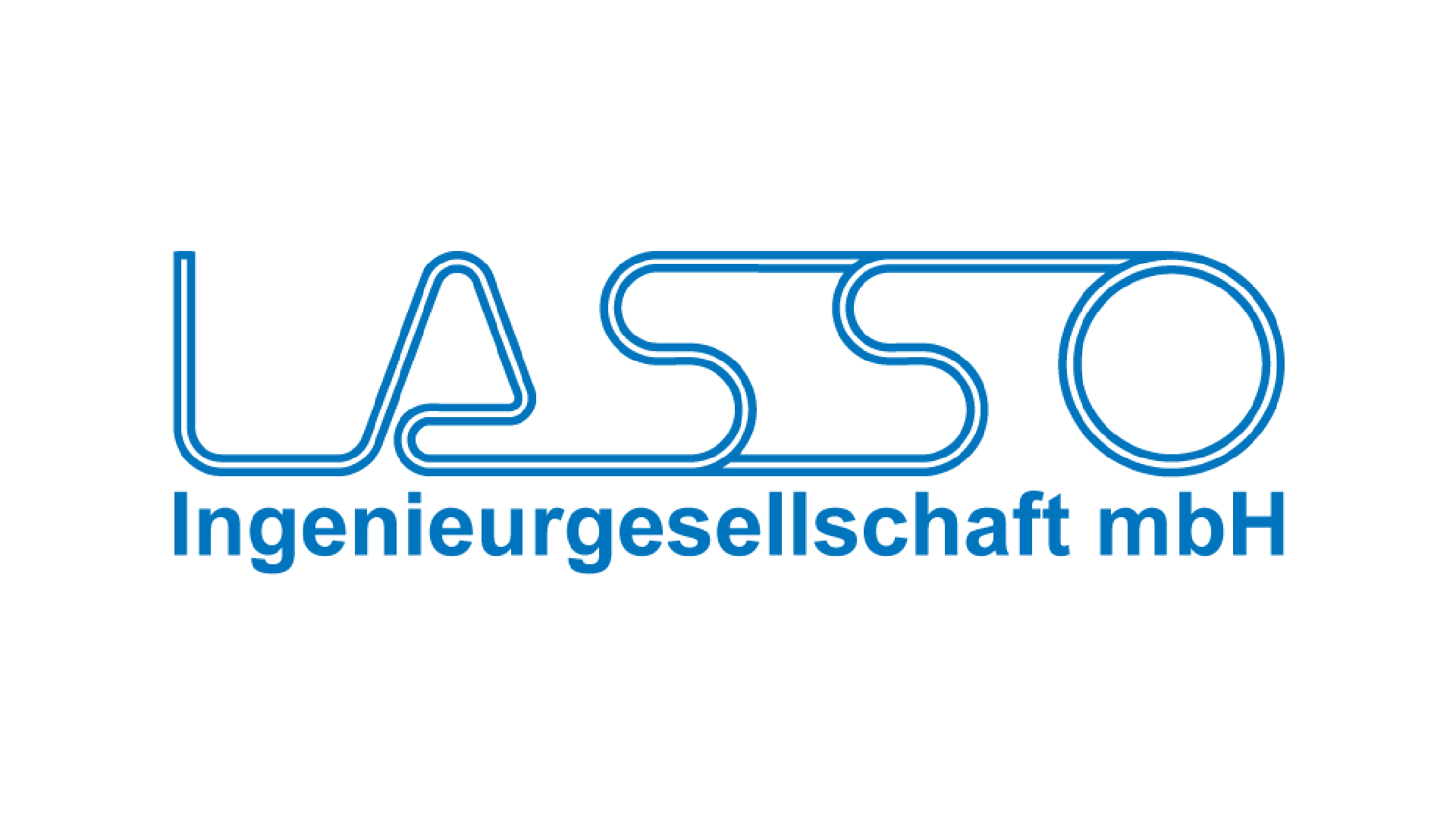
Floating Platform
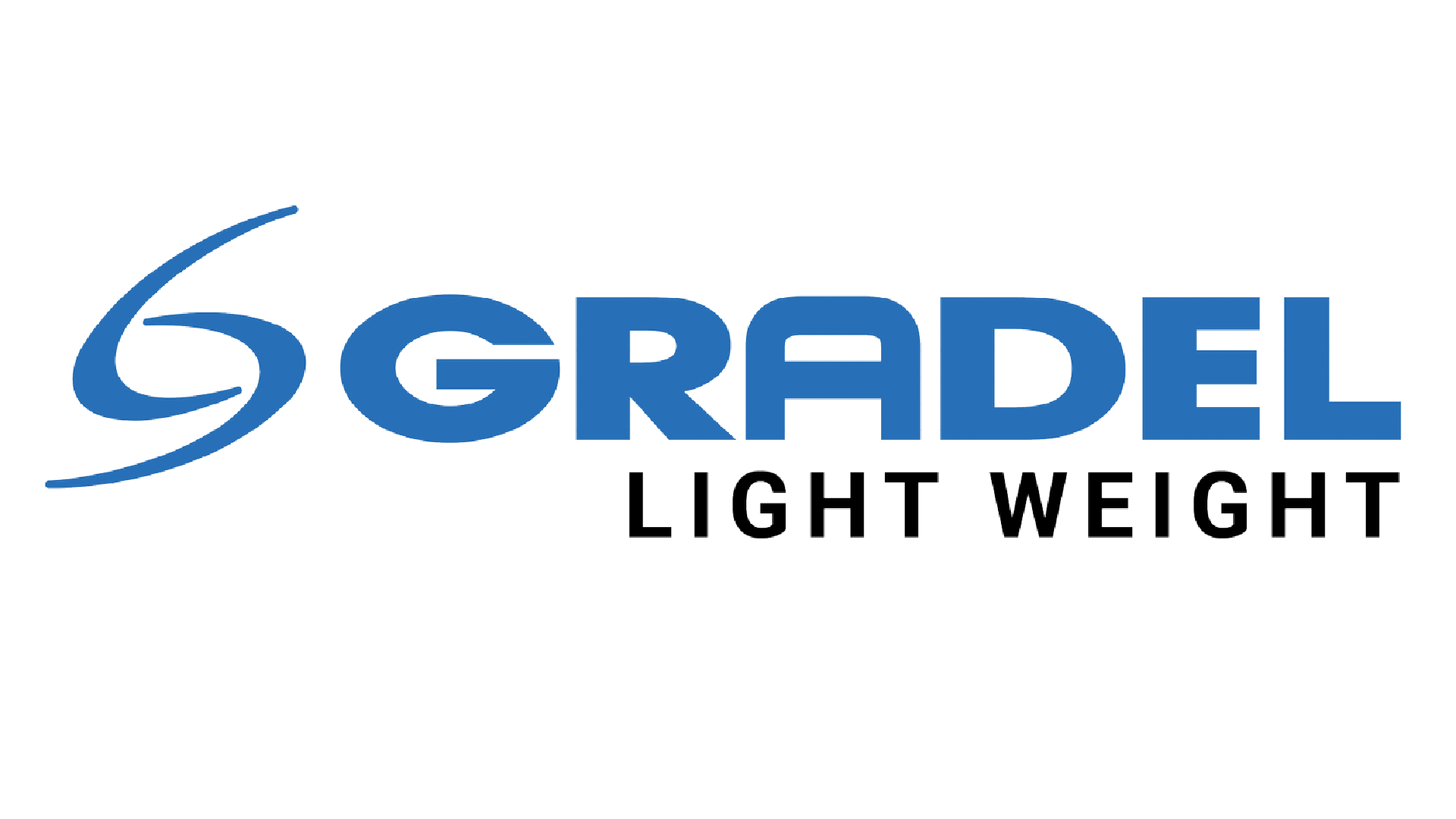
The Floating Platform is an example of a pure wound system consisting of 74 pins and a carbon fiber skeleton. This complex structure has many different sensors, battery packs, thrusters and fuel cells. This custom build was specifically requested from the customer to meet a sever weight reduction, reaching a final weight of 300 g per disc.
As normal sandwich plate construction was too heavy due to the inserts and pins. Gradel explored making a sandwich structure that utilized integrated hybrid joints to connect the various parts and also serves as the substructure of the platform. This in turn allows the researchers to change configurations in several ways while reducing the weight of the final structure.
The programming for the application of the structure is currently being developed though its simulation at the Zero Gravity Lab of the University of Luxembourg.
initiative of the: Space Robotics (SpaceR) Research Group
Credits & Publications
Design and manufacturing: Gradel LW
Client: University of Luxembourg
Gradel Team: Claude Mack (CEO), David Macieira (project leader), Pierre Schumann, Jair Cordeiro, Rodrigo Hernandez (production), Nicolas Jeannot (engineering), Mira Al Akkawi (material engineering), Edurne Morales, Bahar Al Bahar (robotics)
Diagrams and photos: Gradel LW (Edurne Morales)
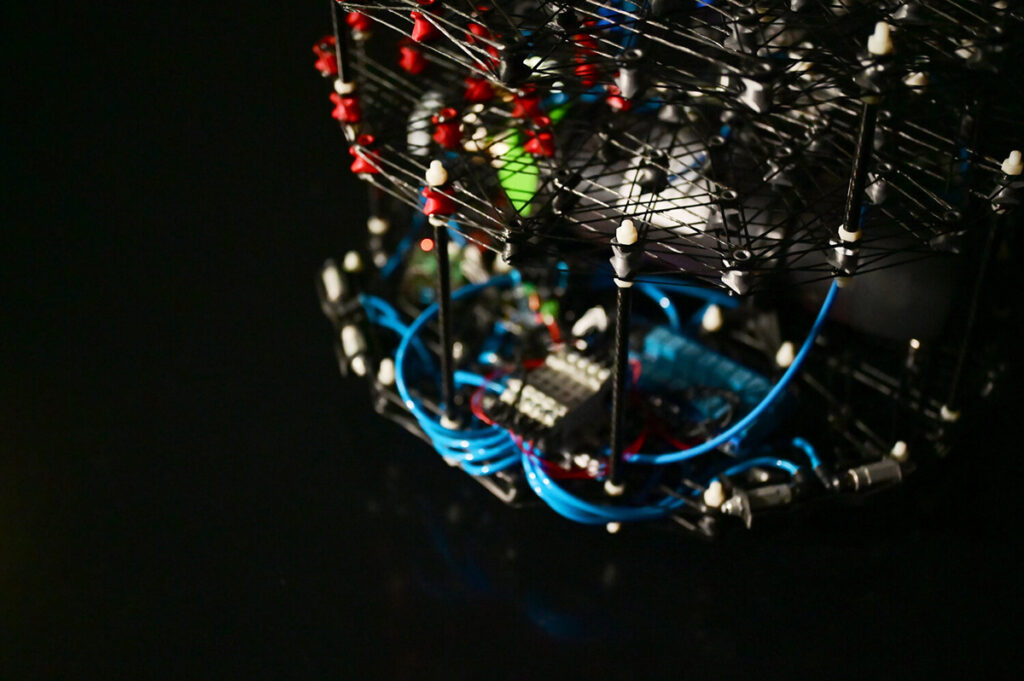
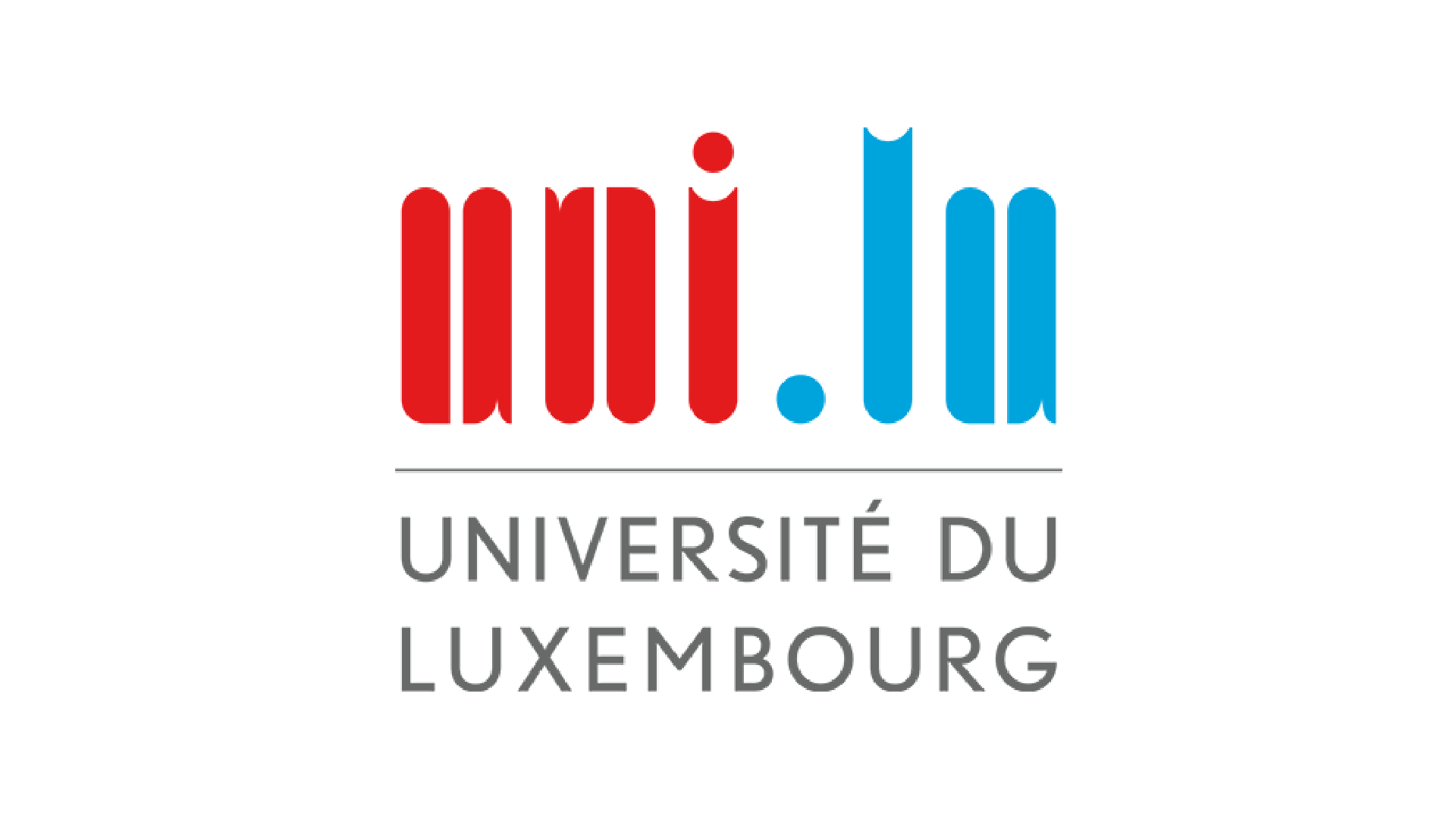
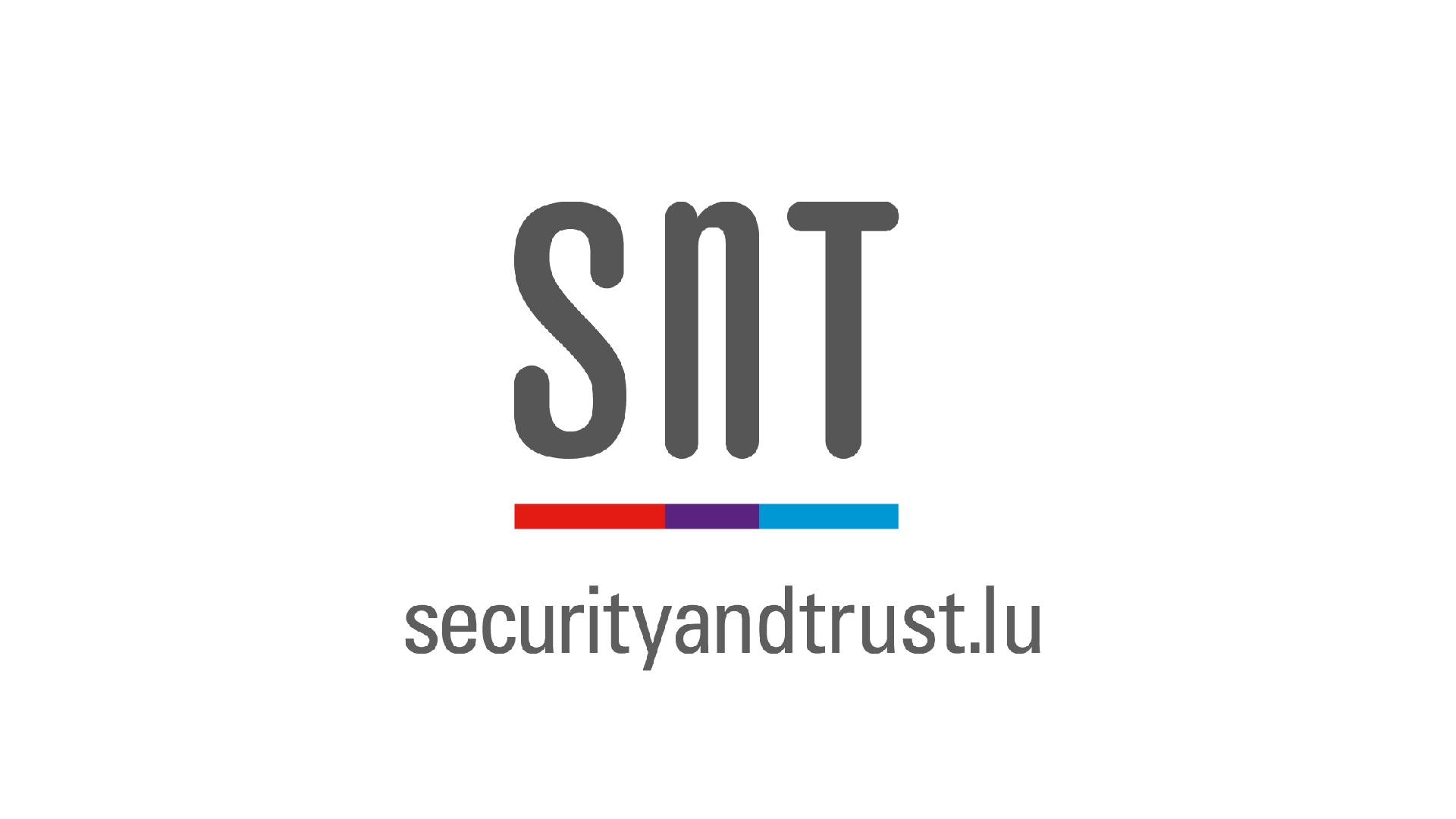
NextGEN 2.0 Seat
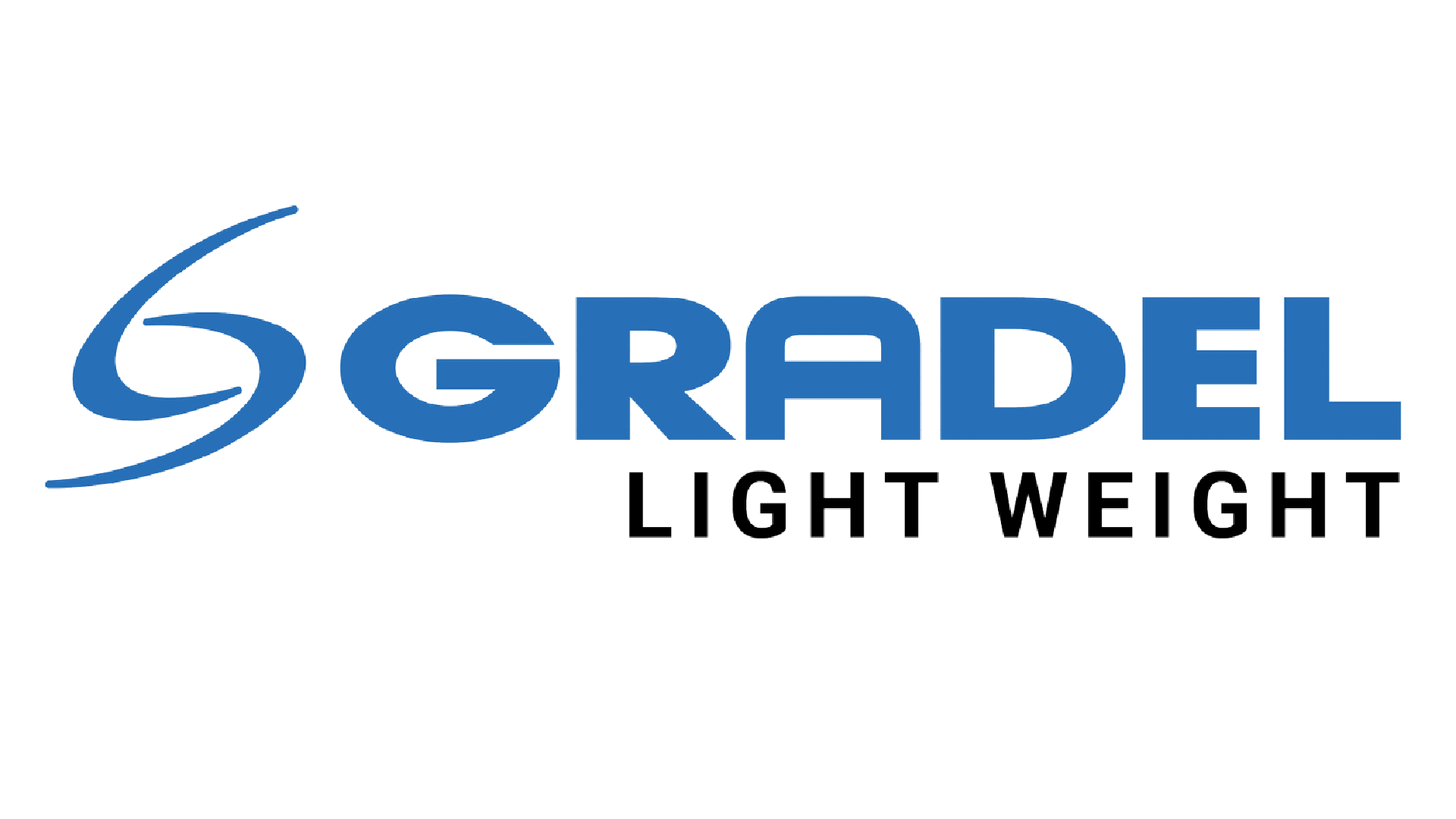
NextGEN 2.0 showcases a new way of producing automotive parts. GRAM is applied on this seat with the purpose of making it strong, light, fast to reproduce, and replicable. Qualities wanted in automotive parts and inherently sustainable due to its efficiency in production, material reduction, and basalt fiber structure.
This seat was FEA analyzed to extract the areas that required more support, reacting to the needs of the structure.
Presented at: Lightweight Symposium 2021 – Kasel Germany
Credits & Publications
Design and Manufacturing: GRADEL LW
Team: Claude Mack (CEO), David Macieira (project leader), Pierre Schumann, Jair Cordeiro, Rodrigo Hernandez (production), Nicolas Jeannot (engineering), Mira Al Akkawi (material engineering), Edurne Morales, Bahar Al Bahar (robotics)
photos: Gradel LW (Brad Elsbury, Edurne Morales)
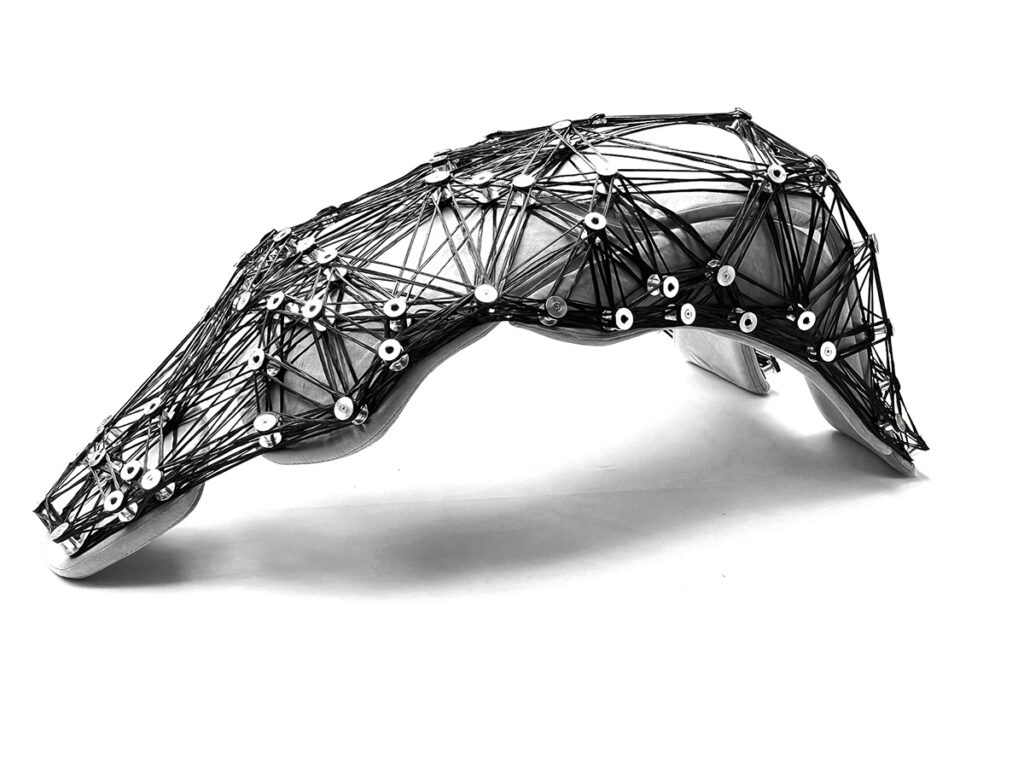
Luxembourg Phone Holder
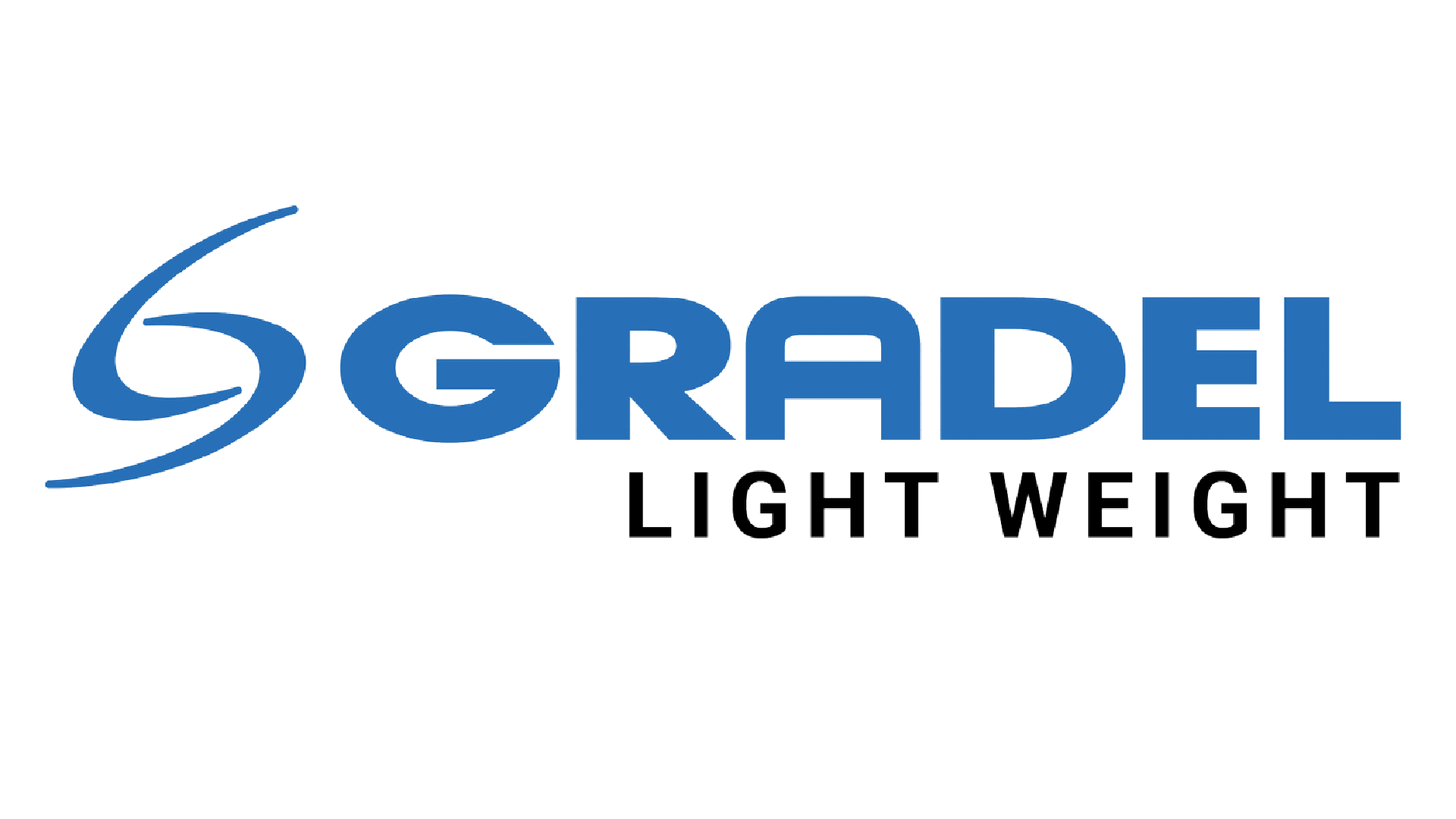
This phone holder shaped with the sillouhete of Luxembourg showcases the capability of the GRAM technologies, to create lightweight, strong and versatile products.
This phoneholder was mass produced and robotically built, and has the possibility of being applied with endless shapes and composite fibers.
Gift for GRADEL LW’s production hall opening event in 2023
Credits & Publications
Design and Manufacturing: GRADEL LW
Team: Claude Mack (CEO), David Macieira (project leader), Alexander Keiller (designer), Pierre Schumann, Jair Cordeiro, Rodrigo Hernandez, David Pizzagalli (production), Laetitia Blaise (material engineering), Edurne Morales, Bahar Al Bahar (robotics)
photos: Gradel LW (Rodrigo Hernández, Brad Elsbury)
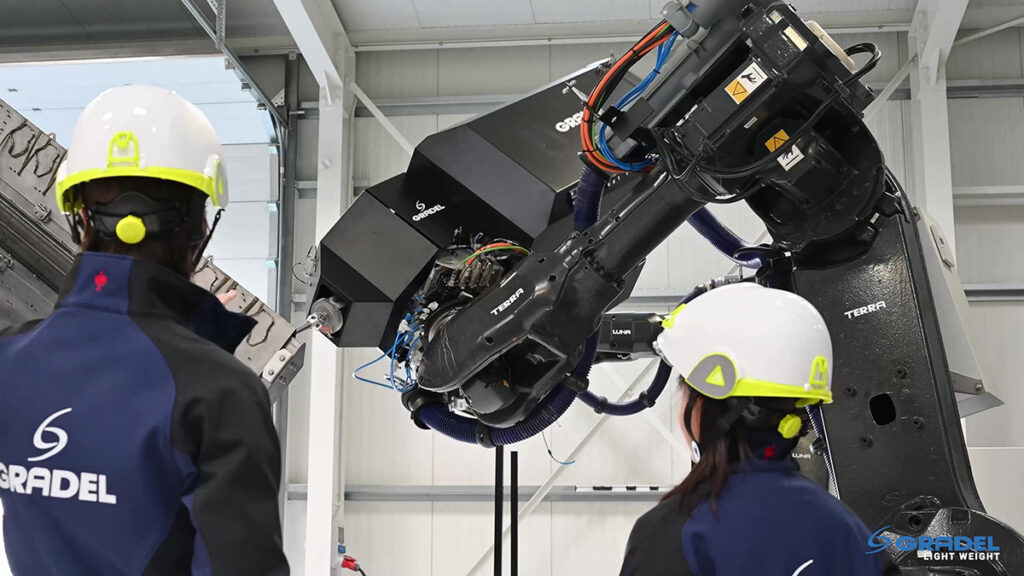
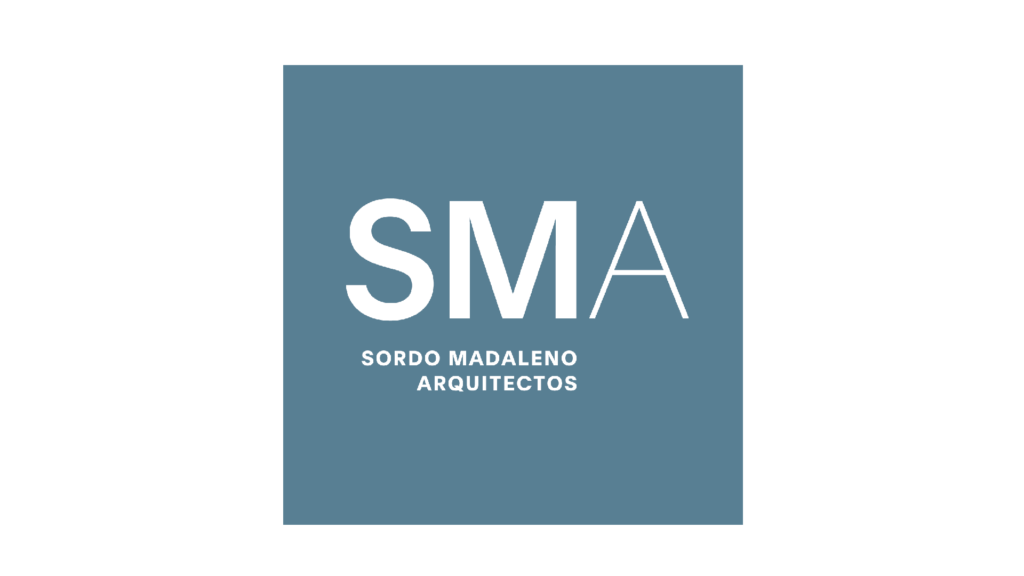
SMA
SHA Wellness Center
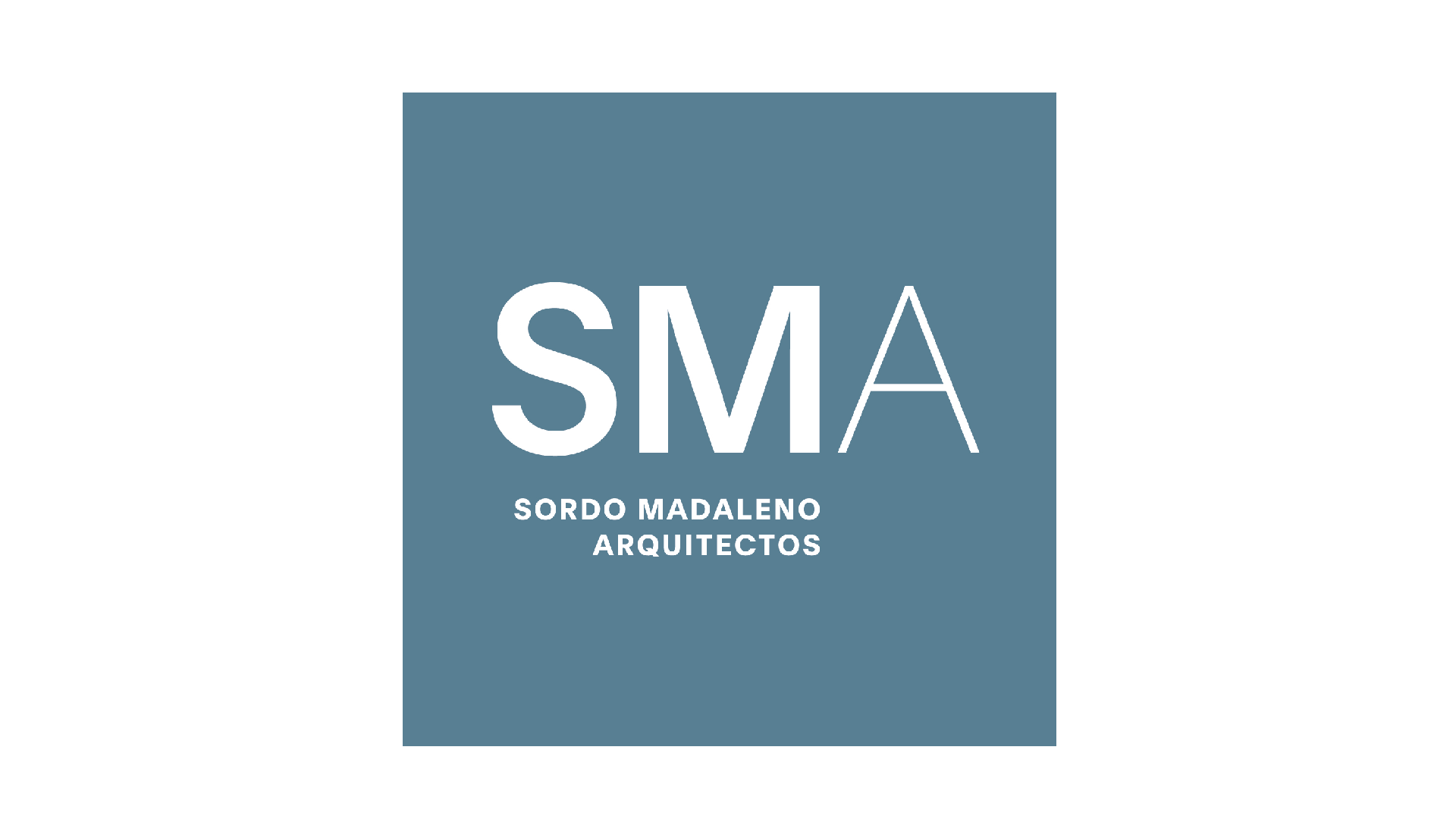
SHA, currently in Alicante, Spain, is a clinic that integrates natural therapies and Western medicine. To create an
effective supervised fusion that adapts to each patient’s nutritional condition, genetics, health, and well-being.
This proposal, currently being built, adapts to Mexican culture and tourism.
This proposal offers Sordo Madaleno Arquitectos’ distinctive material expression applied to the site organically. Within its final volume, it accommodates residences, spa and hotel linearly, taking advantage of its view of the Caribbean.
Ongoing construction
Location: Cancún, Quintana Roo, Mexico
Credits
Architectural design: SMA
Client: SHA Wellness Clinic
Partners: Javier Sordo Madaleno Brigas, Javier Sordo Madaleno de Haro
Team Leader: Fabiano Continanza
Project Manager: Alejandro Espejel
Design Team: Tamara Munoz, Octavio Moreno, Manuel Archundia, Miranda Oyangurén, Mariana Martínez, Edurne Morales, Sinuhé Acosta, Rommel González, Pablo Moncada.
Parametric Specialist: Ángel Quintana, César Saldívar
Consultants: Urbana, Maat Handasa, Luz+Forma
Renders and photos: Pablo Moncada, Tamara Munoz, Sordo Madaleno Arquitectos
Publications: CLADnews, GNGrup, Forbes Mexico
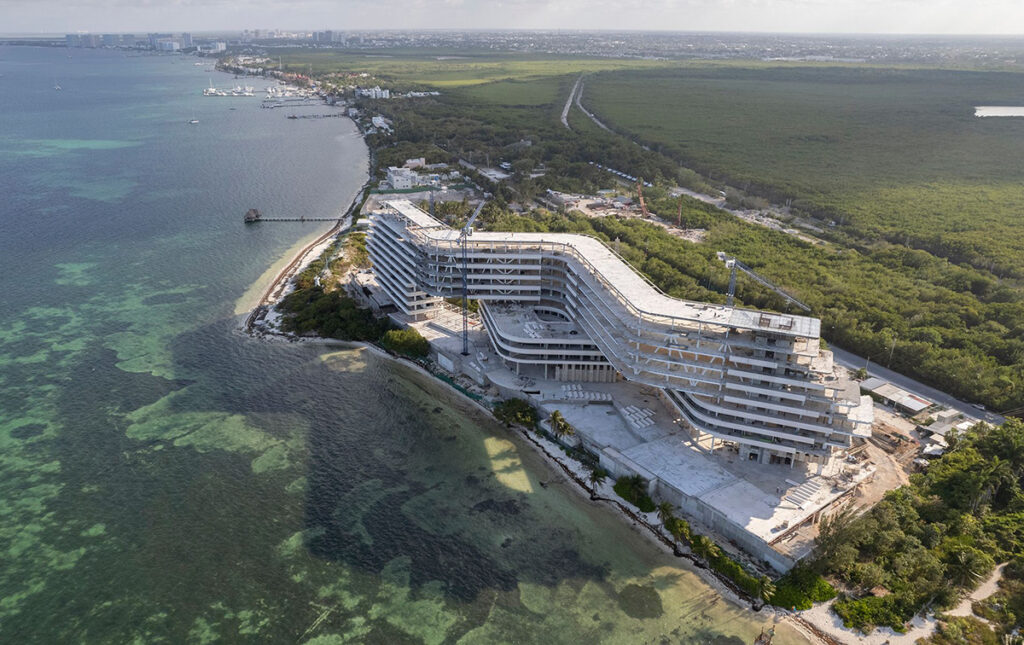
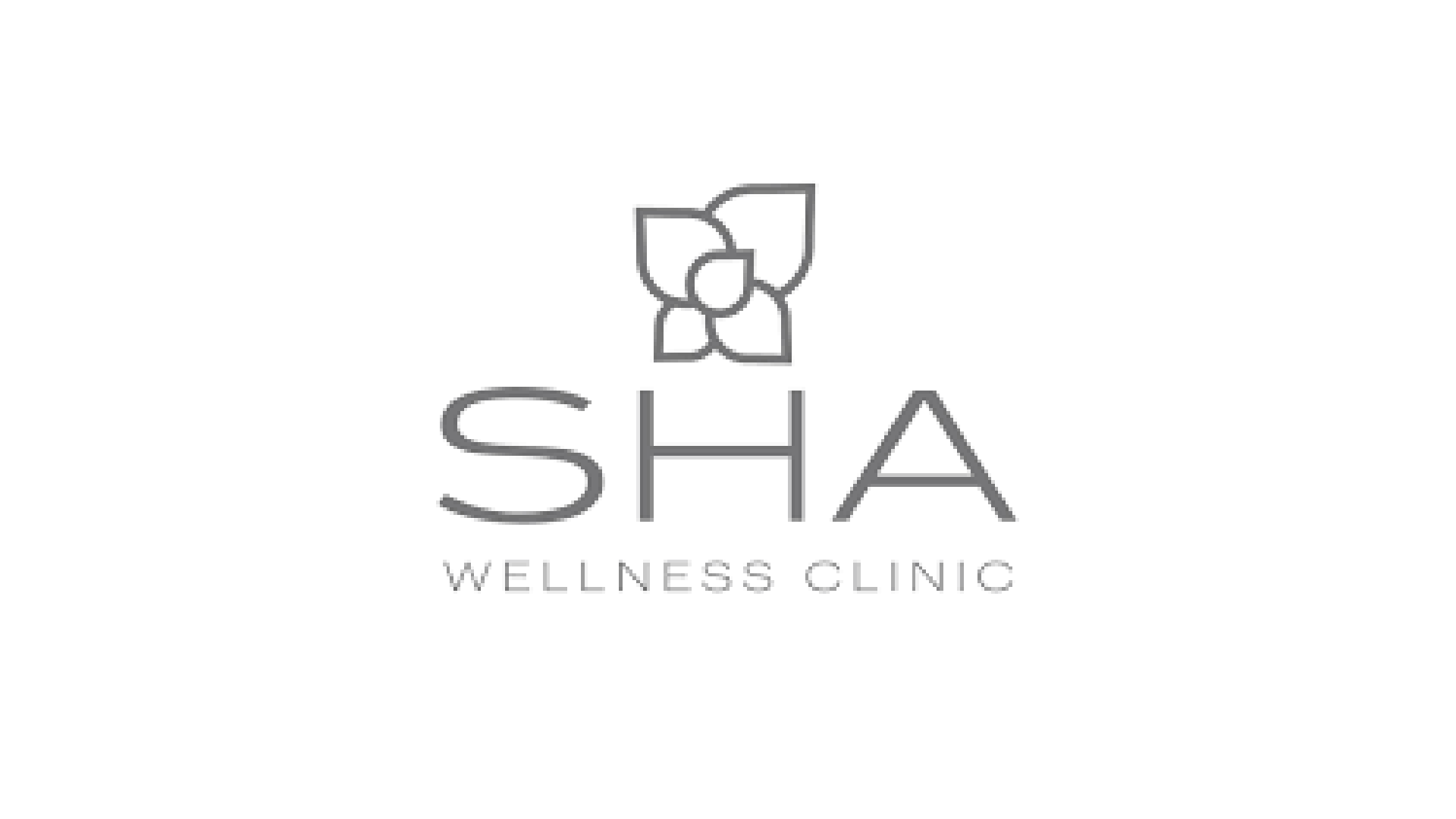
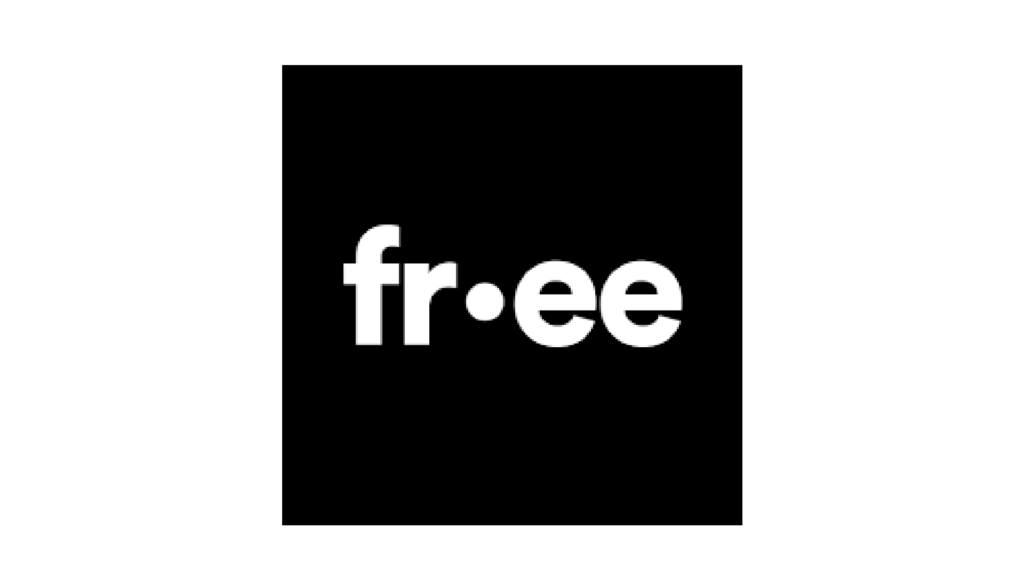
FR-EE
Mexico City’s New International Airport
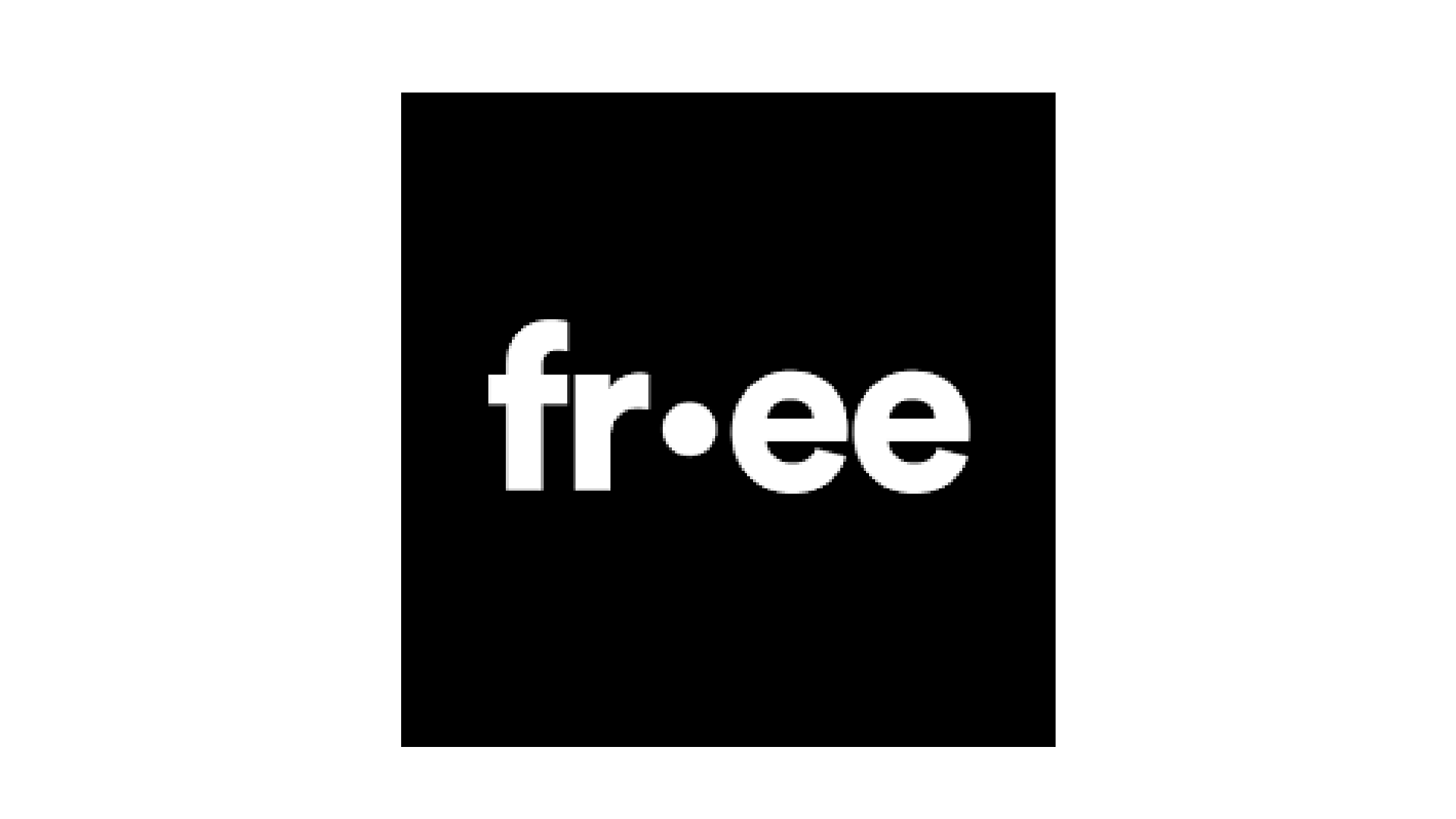
A collaboration between Foster + Partners, FR-EE, and NACO won the international competition to design Mexico City’s new international airport.
Conceived as one of the largest airports to revolutionize the airport experience by ensuring short walking distances, few level changes, easy navigation, and optimized mobility with the use of internal trains and underground tunnels.
Its design merges the Mexican symbolism and architectural monumental scale with contemporary design and structural elements. Some of which include spans of more than 100 m, a lightweight glass and steel structure, a vaulted roof designed for the area’s challenging soil conditions, a unique pre-fabricated envelope system and a high performance envelope that meets high thermal and acoustic standards.
Location: Texcoco, Mexico (canceled)
Years: 2014-2020
Credits & Publications
Client: Grupo Aeroportuario de la Ciudad de México
Partnership: In collaboration with Foster and Partners and Netherlands
Airport Consultants
Project Credits: ARUP, NACO, Inpros, Aba Consultoría, AKF, Colinas del Buen, ConstruBIM, Saad Acústica, L+F Iluminación, Gleeds, Ingeniería Experimental, Inhabit, GDU, La Metropolitana, PIG, PARE, Pragma, THREE, Trimble, Geovizion, RWDI, Tornado
Renders and photos: FR-EE, F+P
Publications: Grupo Aeroportuario de la Ciudad de México, Archello, Dezeen
Awards: 2017 AEC Excellence in Infrastructure by Autodesk for the BIM Model
2021 Rethinking The Future Award, Category Concept Transportation
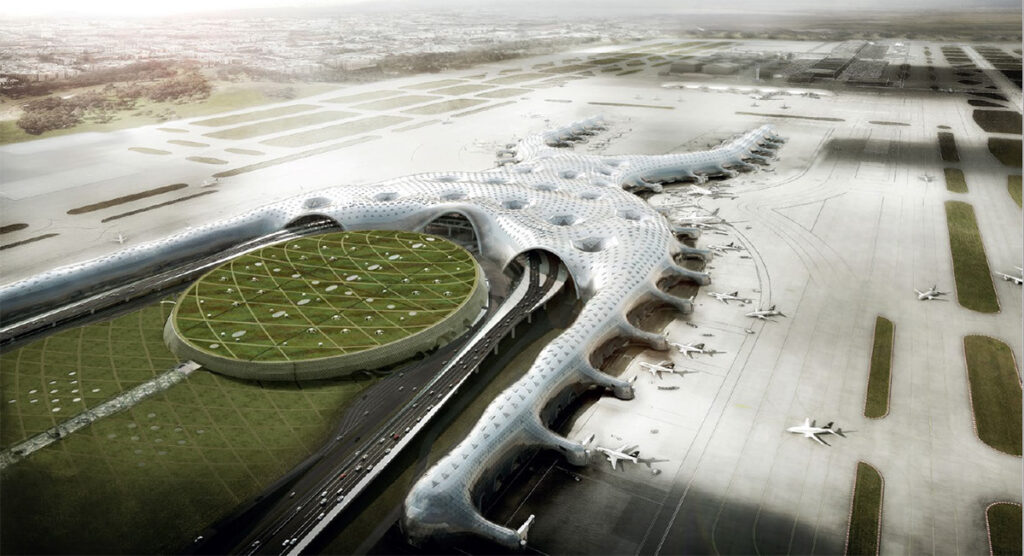

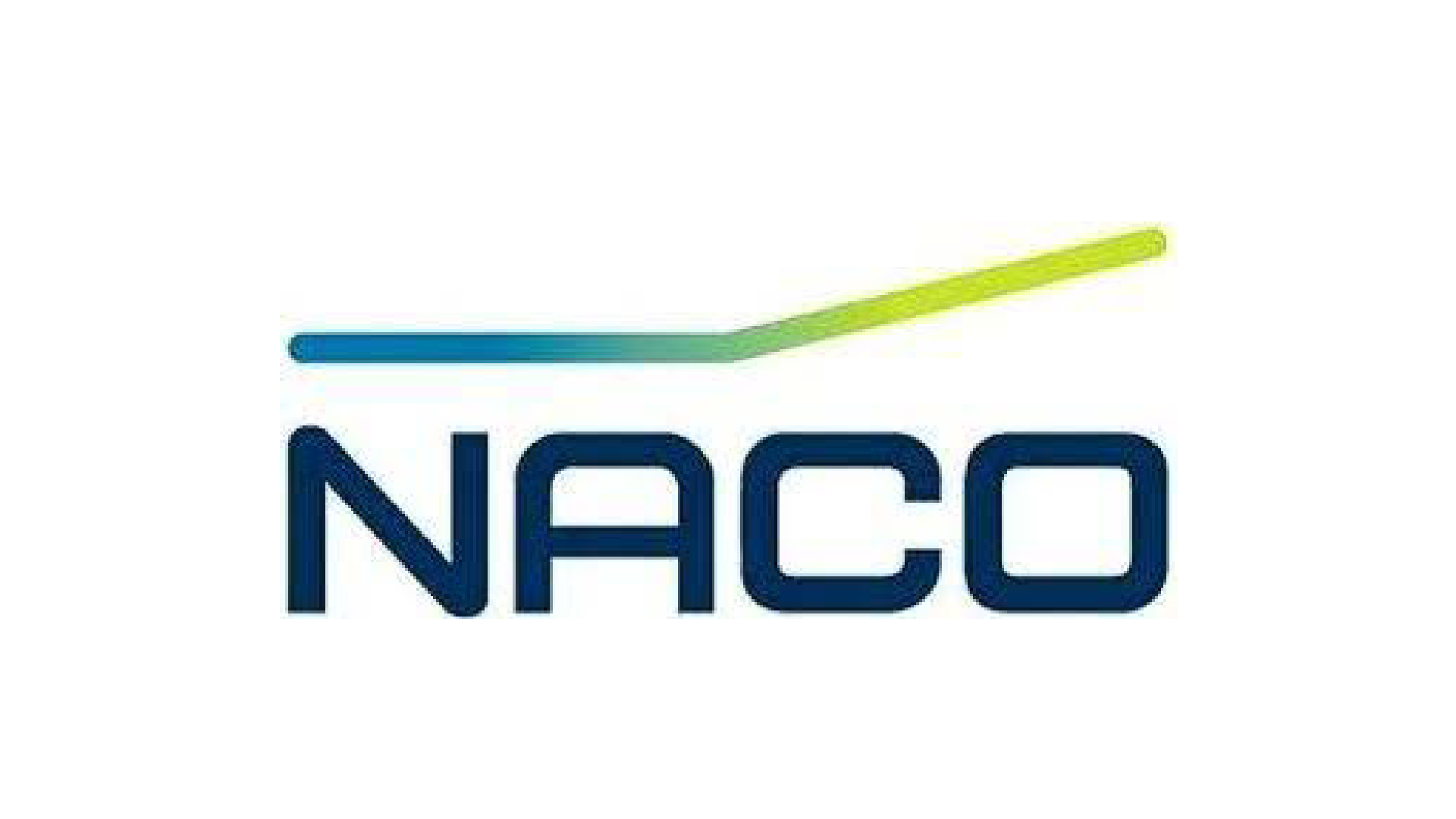
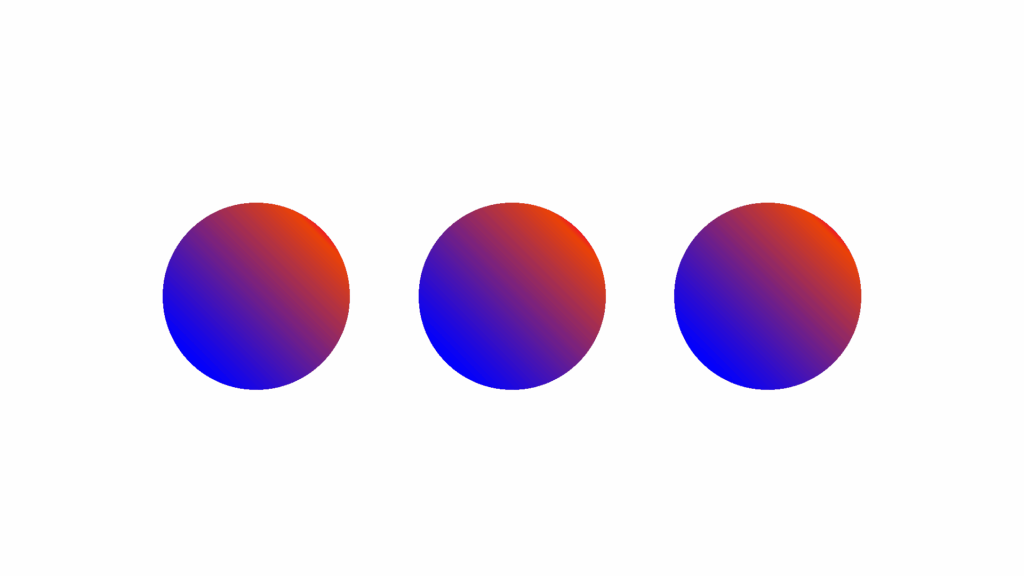
EDURNE MORALES
Iximaltic
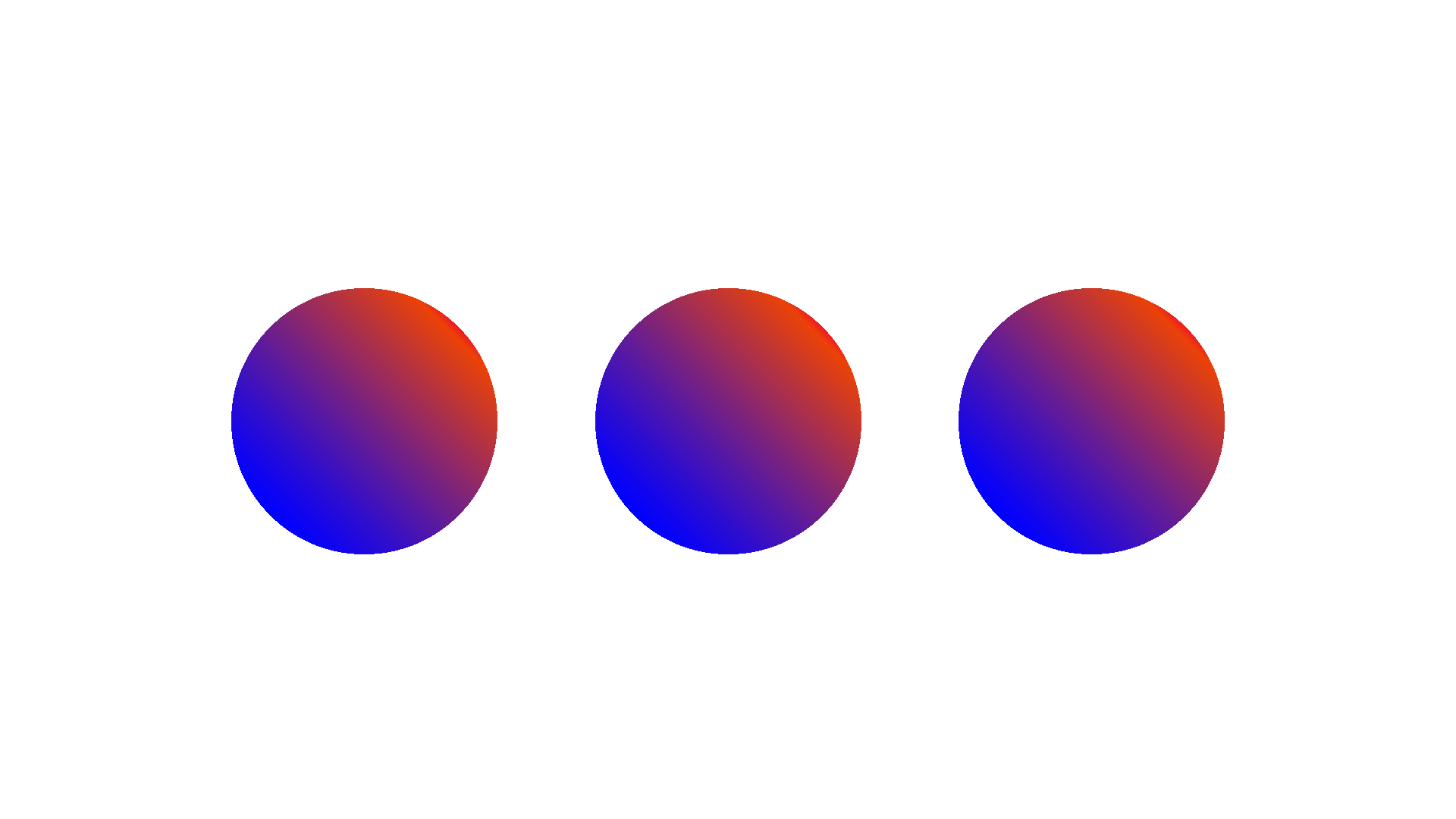
Iximaltic means cornfield in Tojab’al, a mayan language. This project aims to show a bit and promote the use of the native corn diversity in Mexico, reaching approximately 64 varieties with different colors, sizes and taste.
Currently the reliance on genetically modified corn introduced from the US, has an impact at multiple levels. Cross breeding and pollution causes local crops to fail. Additionally, the reliance on prices related to production capacity make it unattractive and hard to continue with the production of native species.
These pieces are based on multiple elements produced with locally sourced and naturally modified clay produced by coeur de terre. The pieces are woven together using adapted basketry techniques and corn husk of purple cacahuazintle and green Oaxacan green corn. Some pieces were also done using open firing.
presented at: BARRO, part of NYLAT (New York Latin American Triennale)
Credits & Publications
Exhibition: Barro, curated by Marinés Soria and Alejandra Rojas
Design and fabrication: Edurne Morales
Machines, clay and firing: coeur de terre by Brauchli Ziegelei AG
Corn husk sourcing: Marina Zúniga, Oscar González, Edurne Morales
Special thanks to: Bahar Al Bahar, Sadik Yigit and my family for eating corn for a month
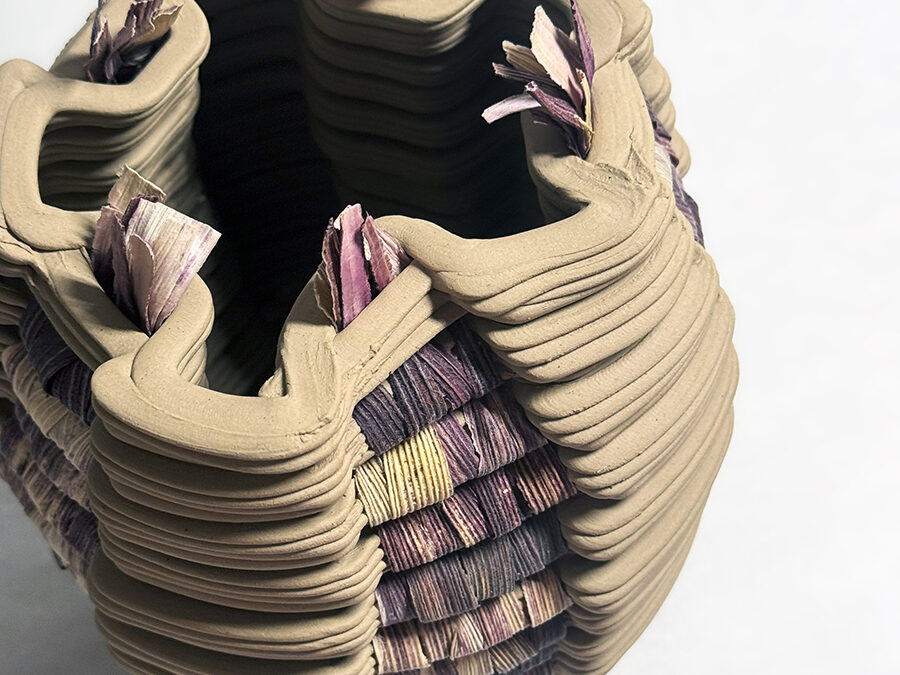
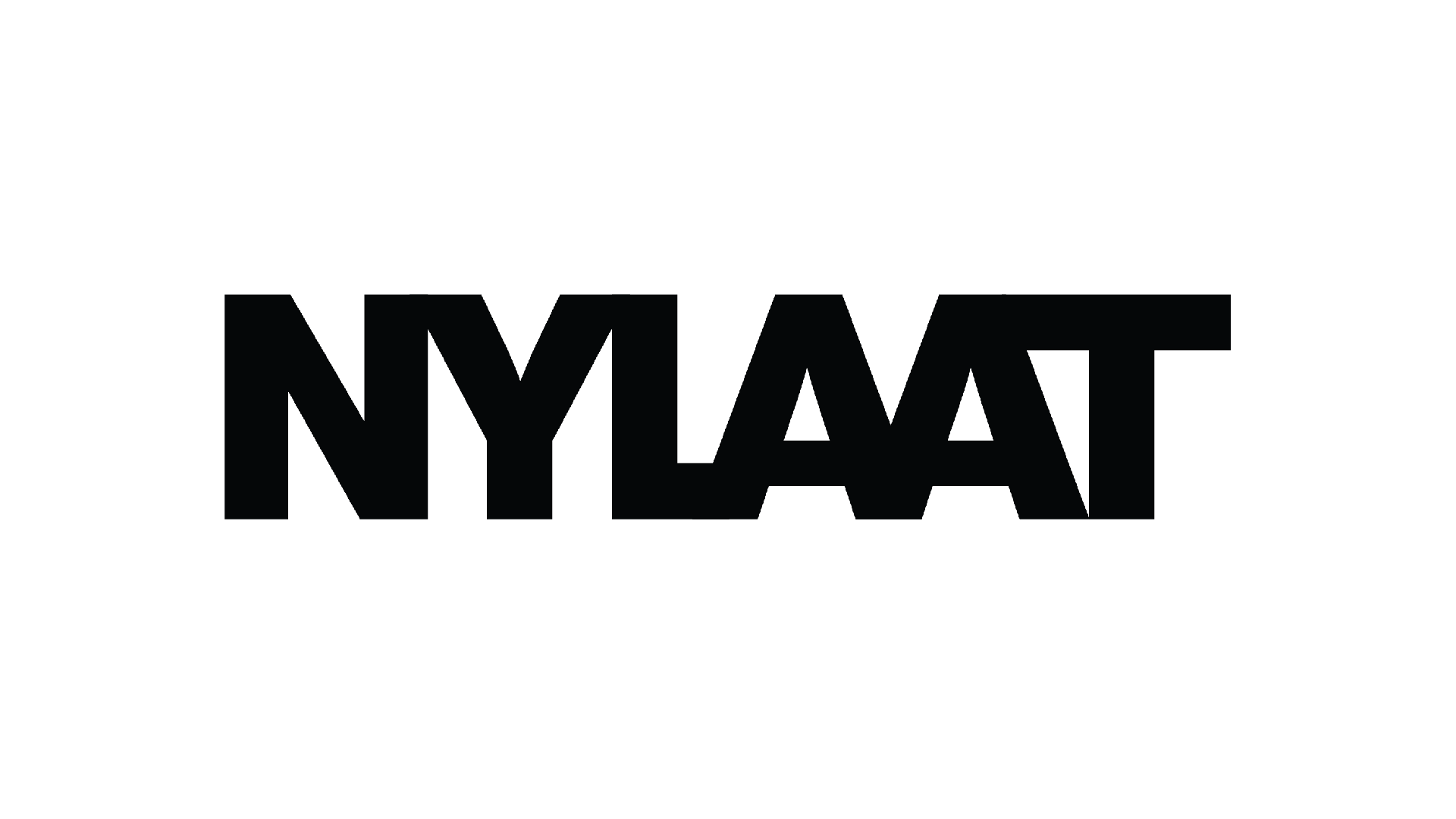

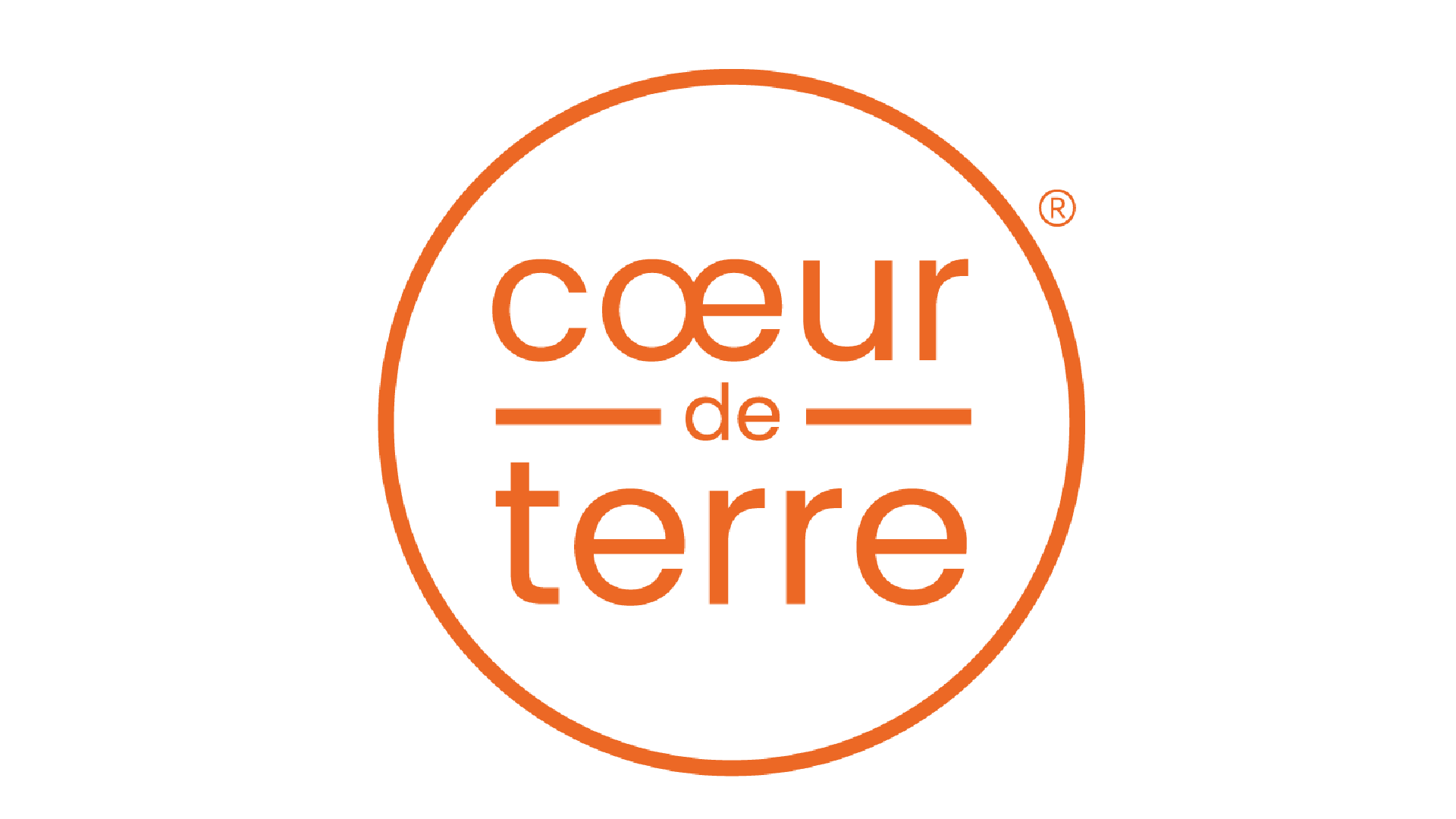
Iximaltic – Fire
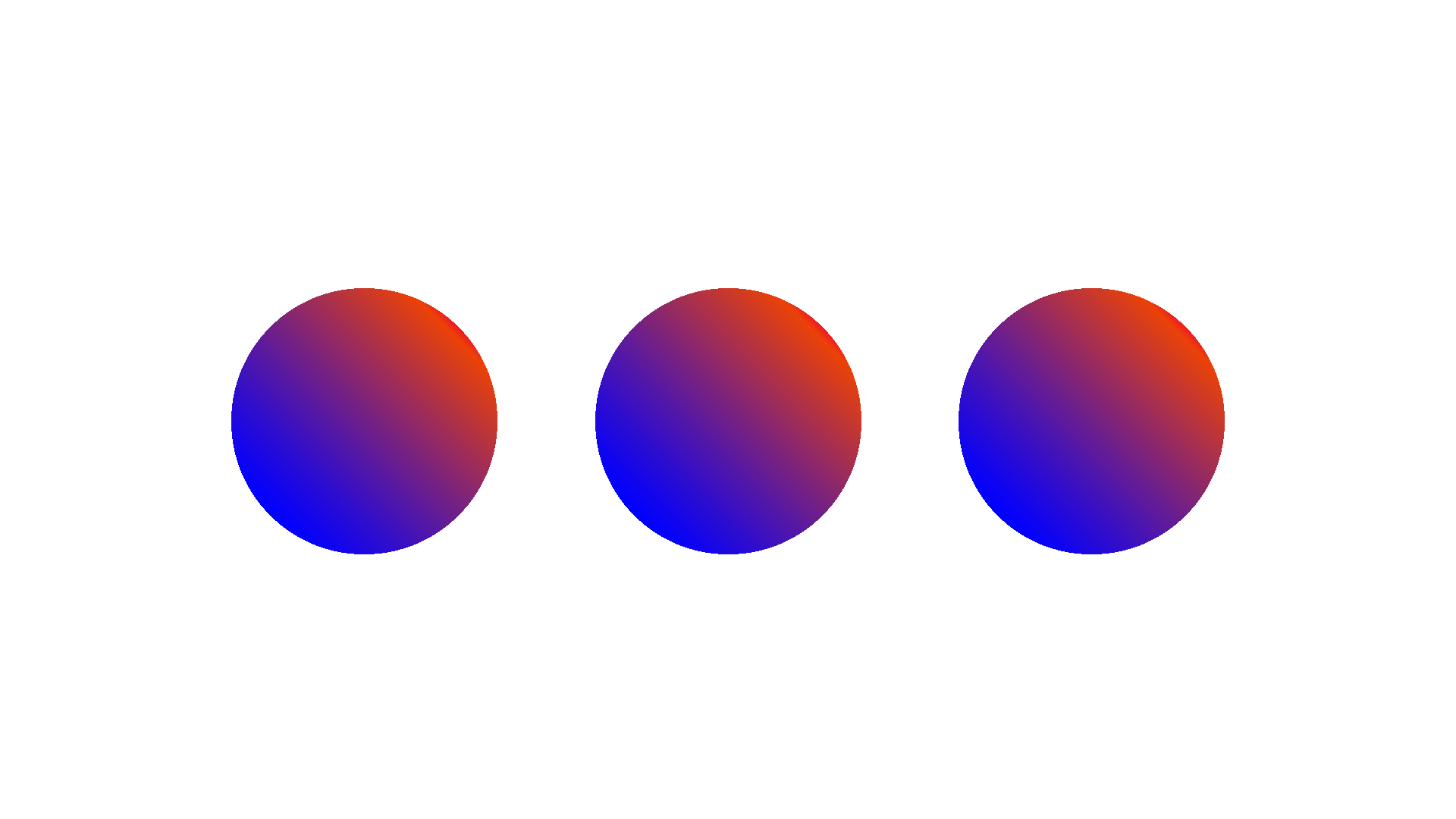
Iximaltic means cornfield in Tojab’al, a mayan language. This project aims to show a bit and promote the use of the native corn diversity in Mexico, reaching approximately 64 varieties with different colors, sizes and taste.
Currently the reliance on genetically modified corn introduced from the US, has an impact at multiple levels. Cross breeding and pollution causes local crops to fail. Additionally, the reliance on prices related to production capacity make it unattractive and hard to continue with the production of native species.
These pieces are based on multiple 3d printed elements, fired with an open firing and wound together using adapted basketry techniques.
presented at: BARRO, part of NYLAT (New York Latin American Triennale)
Credits & Publications
Exhibition: Barro, curated by Marinés Soria and Alejandra Rojas
Design and fabrication: Edurne Morales
Material: coeur de terre by Brauchli Ziegelei AG
Firing: Bahar Al Bahar, Sadik Yigit, Edurne Morales
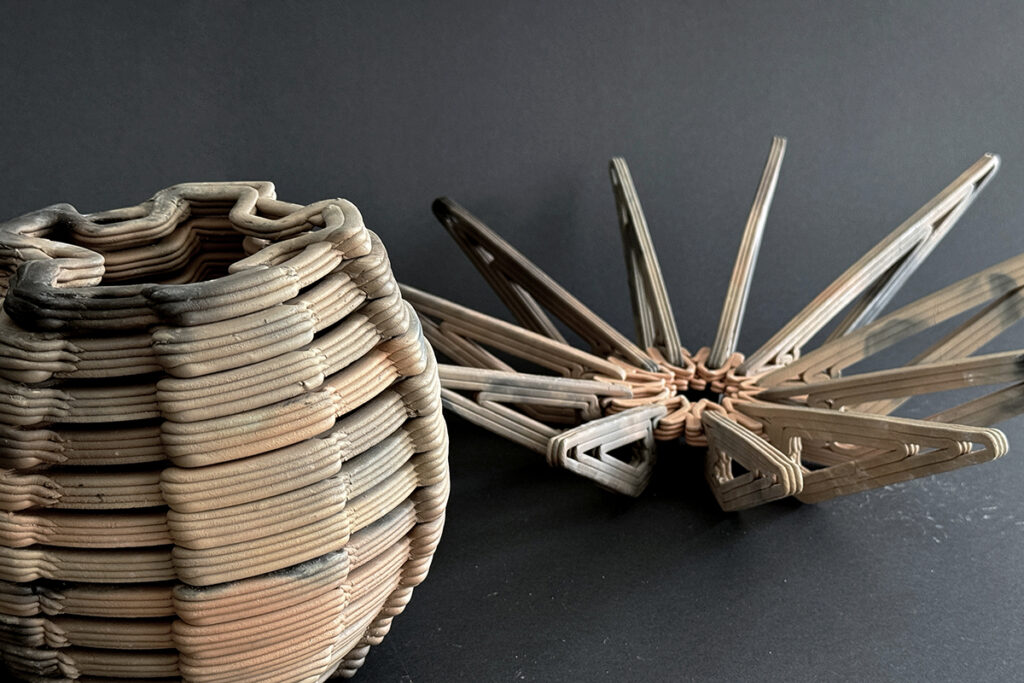
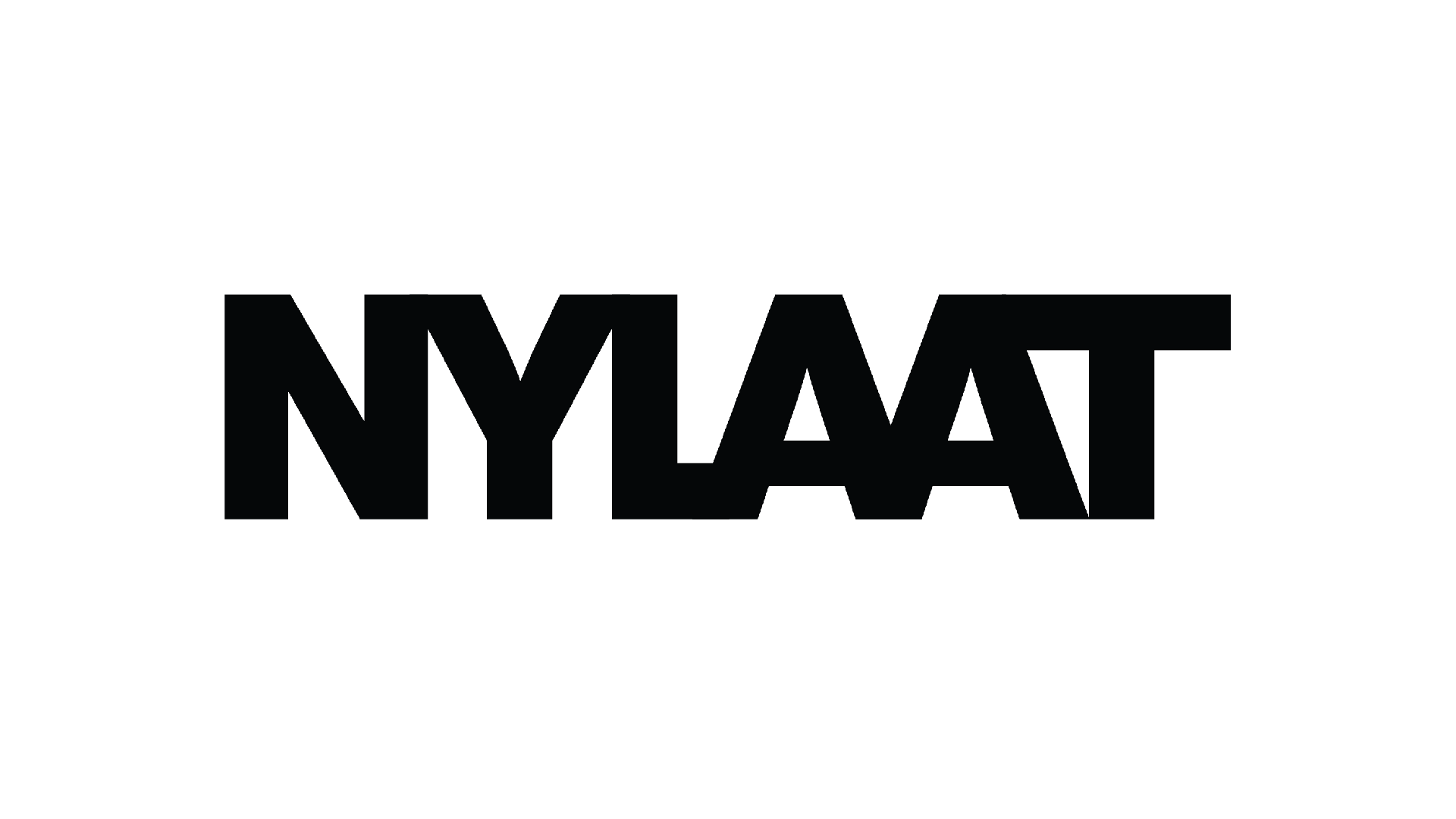

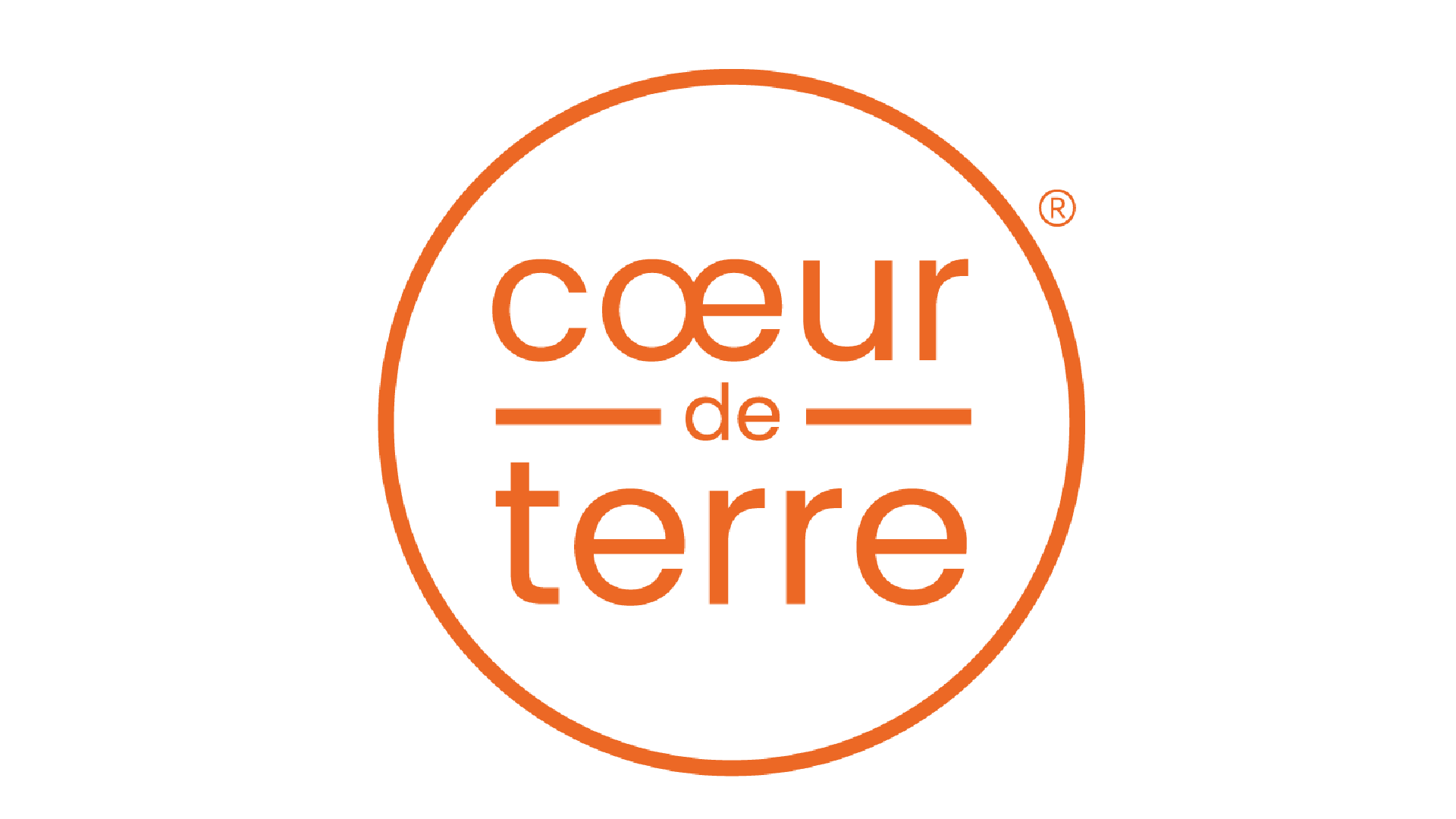
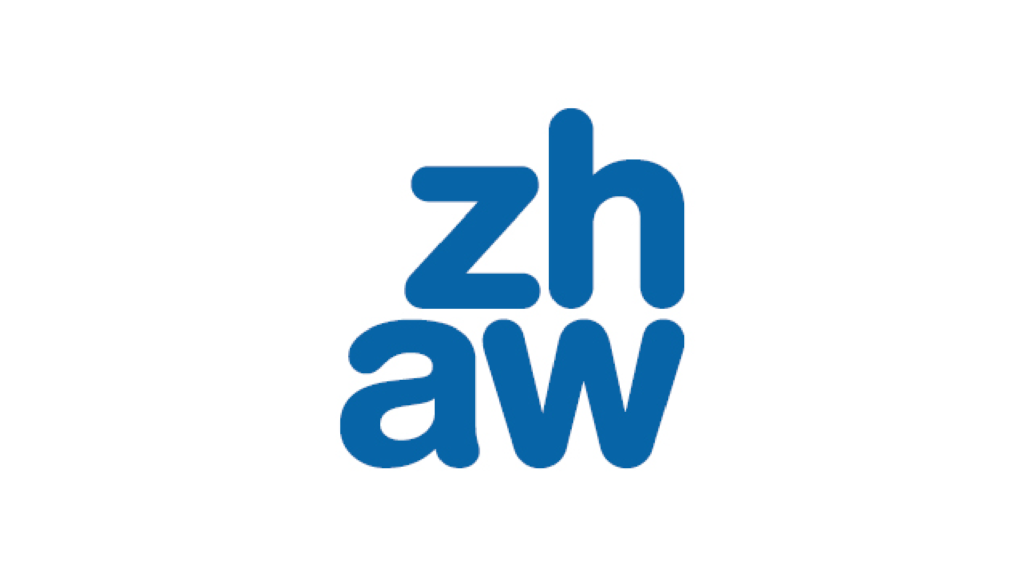
ZHAW
Earth Space
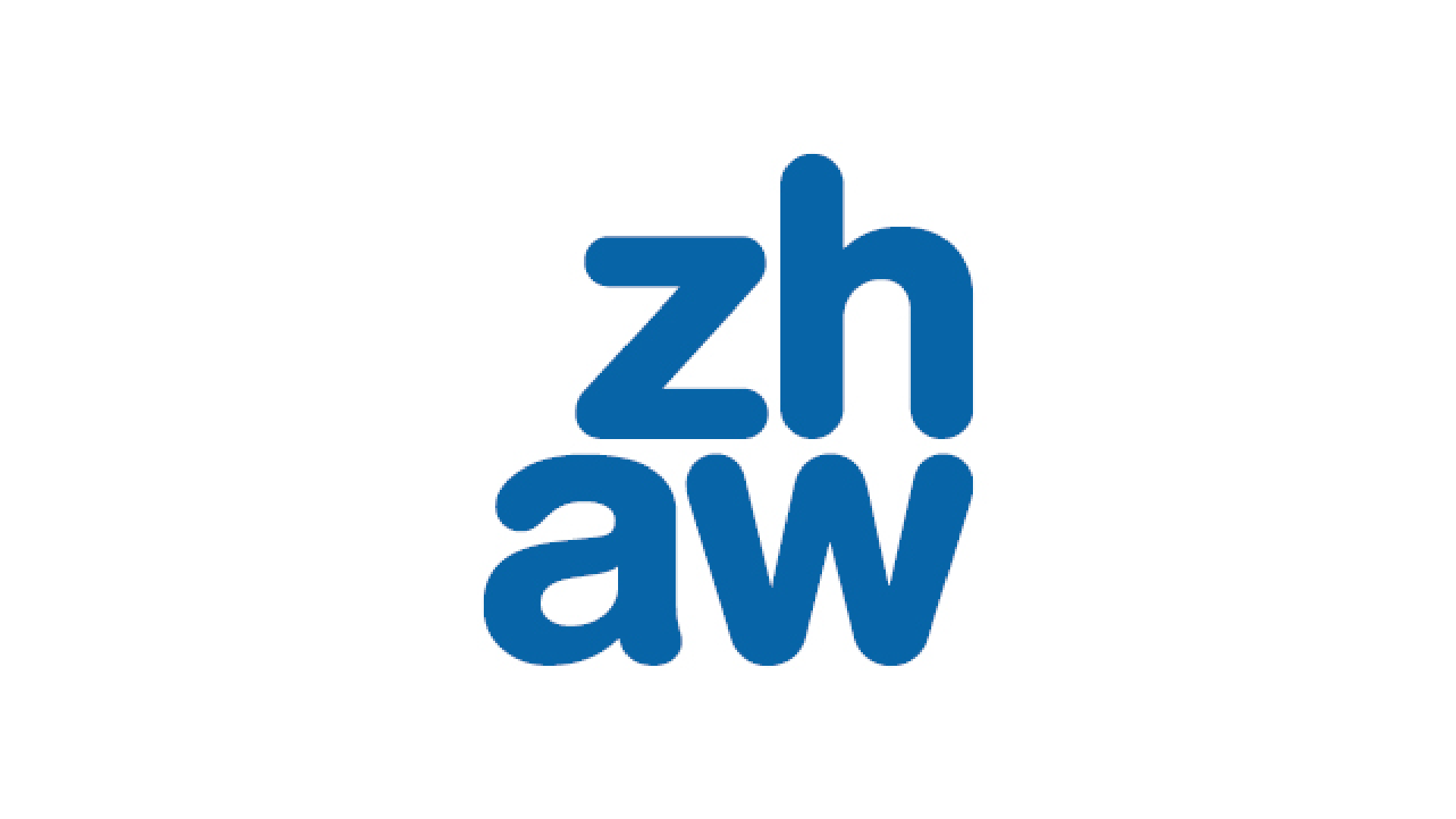
Winter School hosted by Università della Svizzera Italiana
ZHAW/USI winter research project on sustainable construction through digital fabrication. This project is an investigation towards 3D-printing articulated and reconfigurable clay walls.
Earth Space investigates the potential of industrialized 3D-printing of clay modules for articulated and reconfigurable structures. Through computational design and digital fabrication a small series, based on approximately 600 pieces of differentiated modules, is produced and used to design and build a functional, reconfigurable and spatially unique wall. This allows a meaningful reflection on novel sustainable constructive systems enabled through digital processes.
The modules are unfired, gaining strength with the geometry. The pattern on the outside walls is adapted to allow more design options and show more customizability alternatives.
Credits & Publications
ZHAW Institute for Building Technology and Process in collaboration with USI Accademia di architettura di Mendrisio, FMAA Fabrication- and Material-Aware Architecture
Collaborators: David Jenny (Workshop Lead ZHAW) , Prof. Dr. Ena Lloret-Fritschi (Workshop Lead USI), Edurne Morales (ZHAW), Sevgi Altun (USI), Yasaman Yavaribajestani (ZHAW), Sacha Cutajar (USI)
Students: Beatrice Damiani (USI); Hedwig Michelle Ringeisen-Castellanos (ZHAW); Irena Toplanaj (ZHAW); Jens Rudolf Kristiansen Ugelstad (USI); Julian Reissner (ZHAW); Kabishnah Rathirajan (ZHAW); Leon Schlatter (ZHAW); Luchuan Su (USI); Marina Bosch (ZHAW); Maximillianus Agitama (USI); Meltem Simsek (ZHAW); Sam Leon Leuenberger (USI); Severin Marti (ZHAW); Sofia Basso (USI); Wanchen Ning (USI)
Industry Partner and Sponsoring: cœurdeterre by Brauchli Ziegelei AG
Photos and videos: David Jenny, Alberto Canepa, Edurne Morales
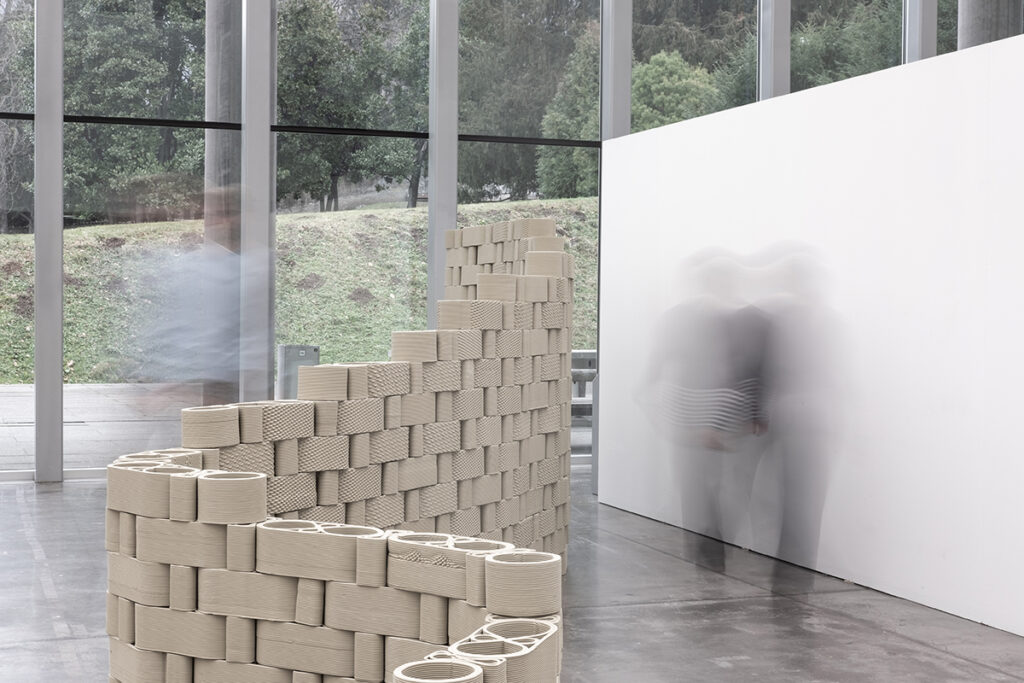
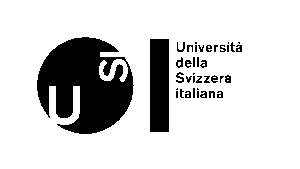
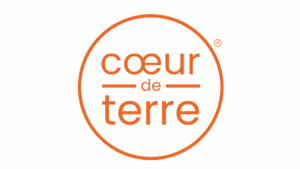
Collaborative Structure
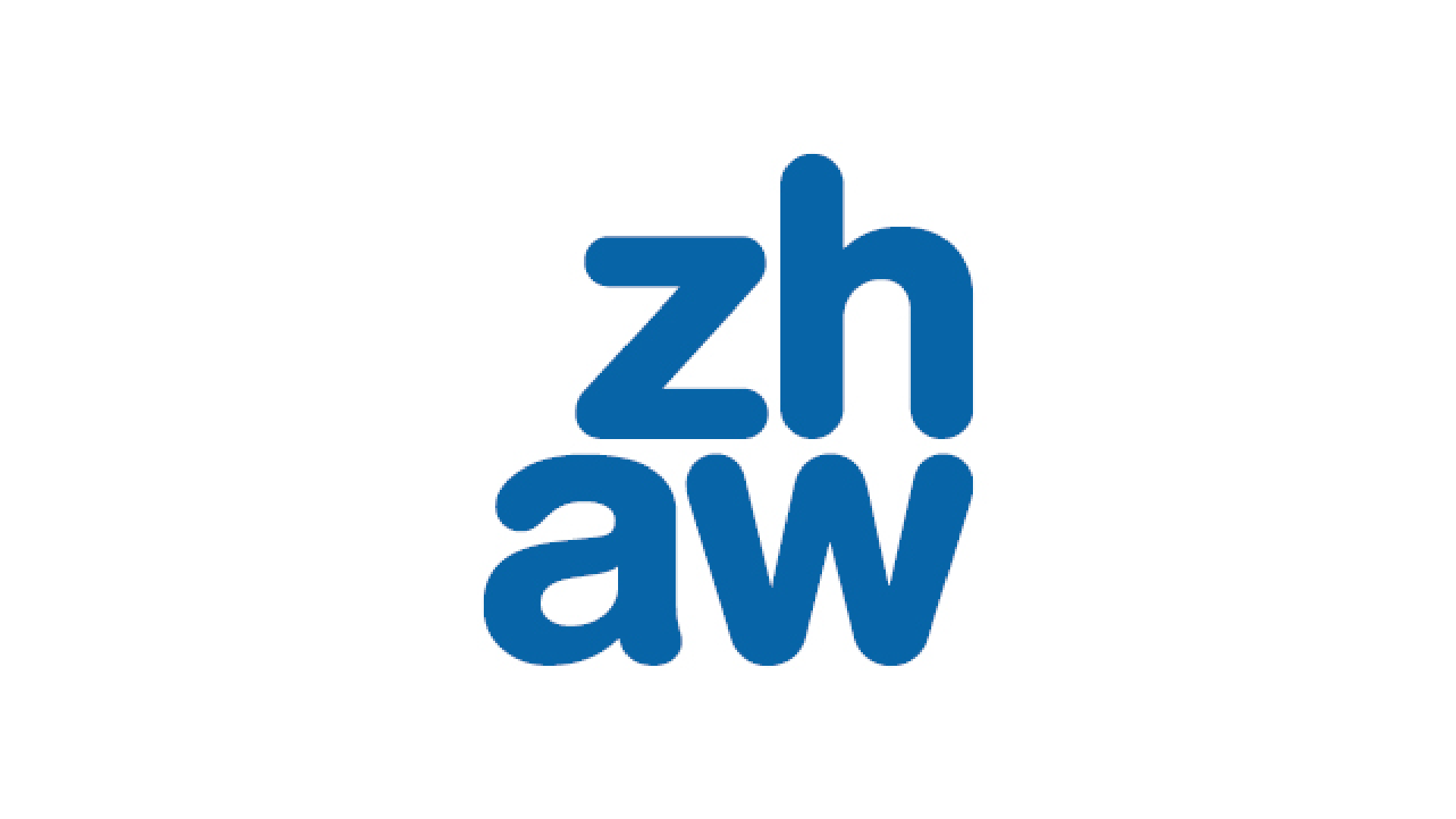
Participative fabrication with recycled timber through digitally augmented processes. This workshop explored the interaction between manual craft and digital fabrication processes through the collaborative development and fabrication of parametrically controlled furniture design. This furniture is imagined as a functional bench consisting of a multitude of different elements, each neighboring designer has the possibility of influencing the next stage of the design.
The fabrication system is based on a flexible assembly system based on timber-only connections, manipulated and adapted using a custom parametric configurator made with ShapeDiver. The configurator makes it possible to export the information that is used to cut the pieces, this process is done with the use of a Shaper Tool machine (portable CNC router).
The system is easily applicable and hightly flexible, the final artefact is the result of both individual and collaborative decisions that are directly executed through a participative fabrication process.
Credits & Publications
ZHAW Institute for Building Technology and Process, part of the Future of Construction 2024 workshops
Collaborators: Yves Ebnöther (workshop lead), Dr. Konrad Graser, David Jenny, Edurne Morales
Students: Radoslav Sovjak, Petr Krejcirik, Camila Moreira Dyevre
Industry Partner and Sponsoring: SBB
Photos and videos: Yves Ebnöther, David Jenny, Edurne Morales
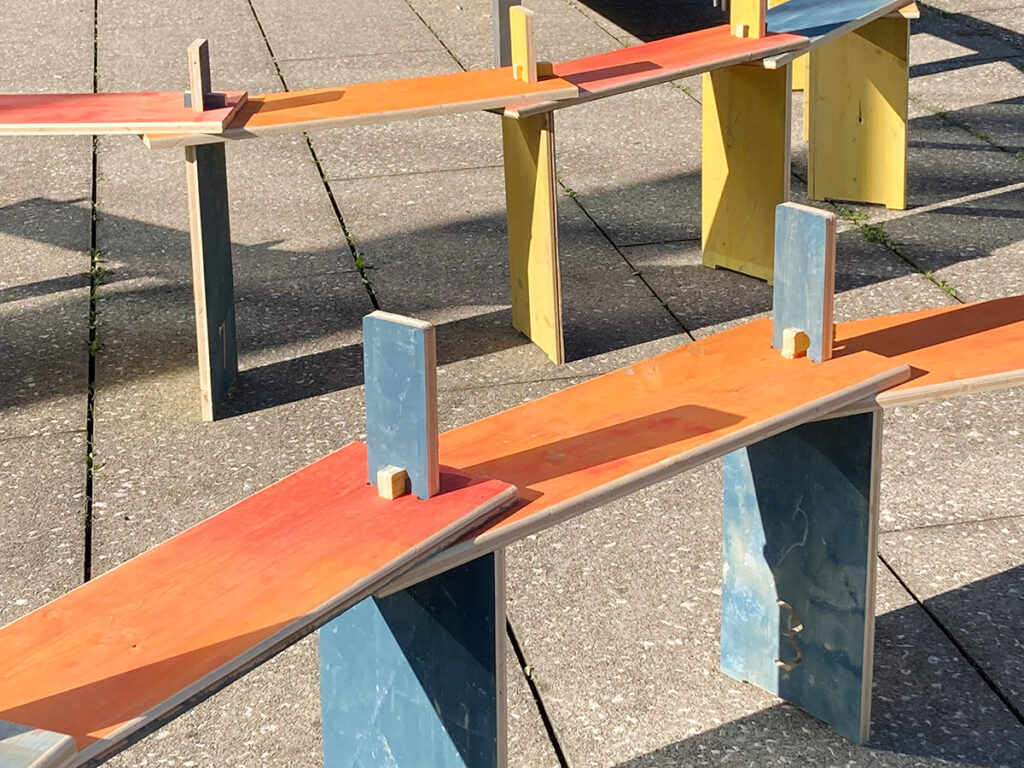
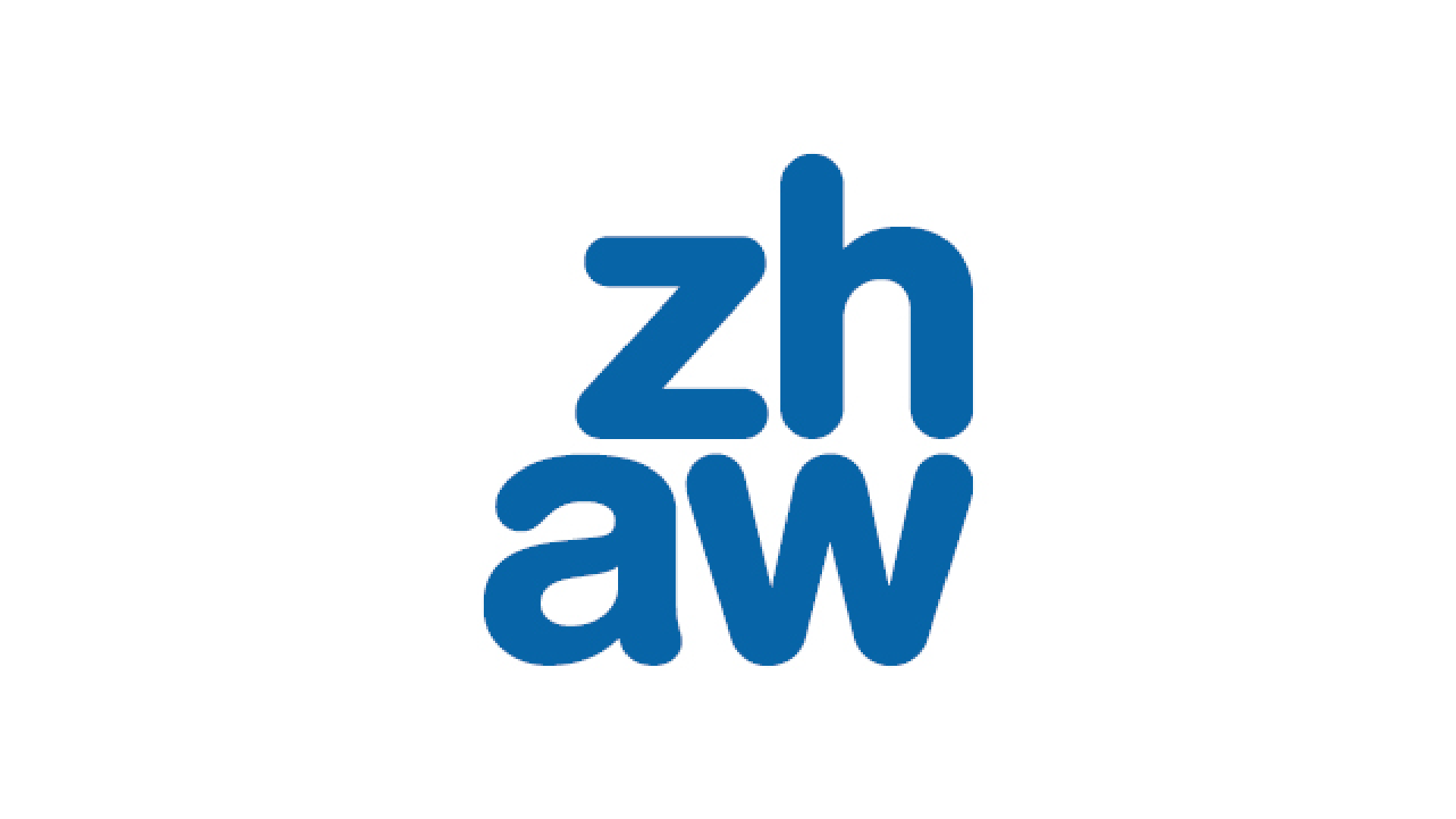